The importance of Leak Reduction and Refrigerant Recovery
20 Slides3.40 MB
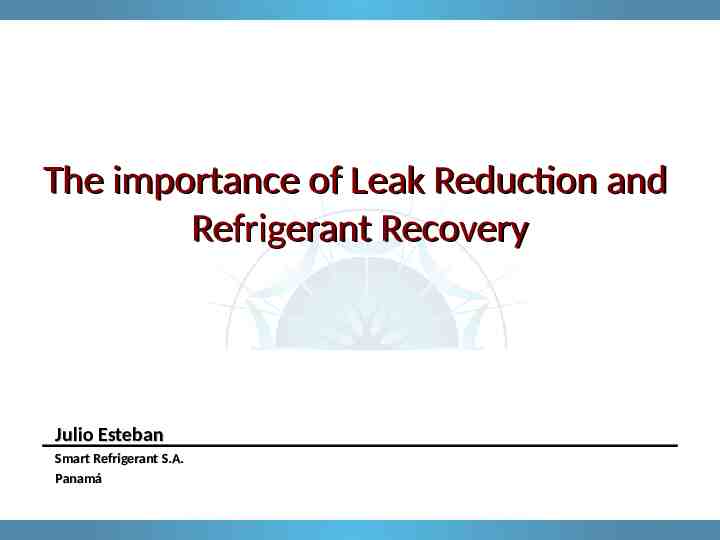
The importance of Leak Reduction and Refrigerant Recovery Julio Esteban Smart Refrigerant S.A. Panamá
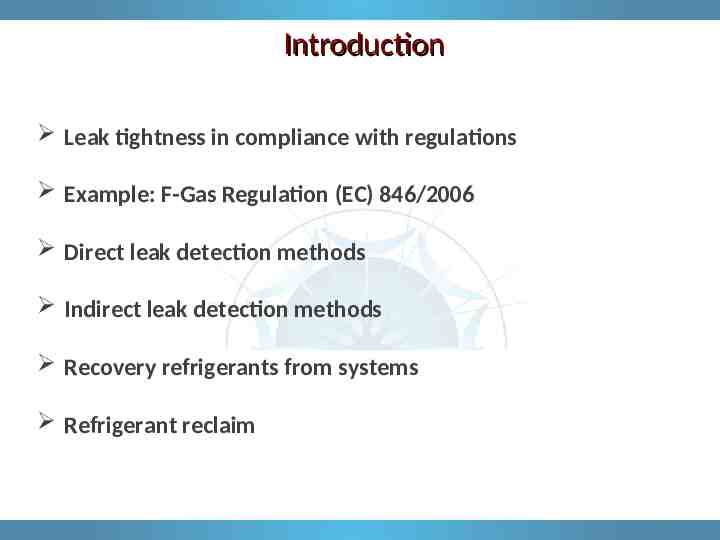
Introduction Leak tightness in compliance with regulations Example: F-Gas Regulation (EC) 846/2006 Direct leak detection methods Indirect leak detection methods Recovery refrigerants from systems Refrigerant reclaim
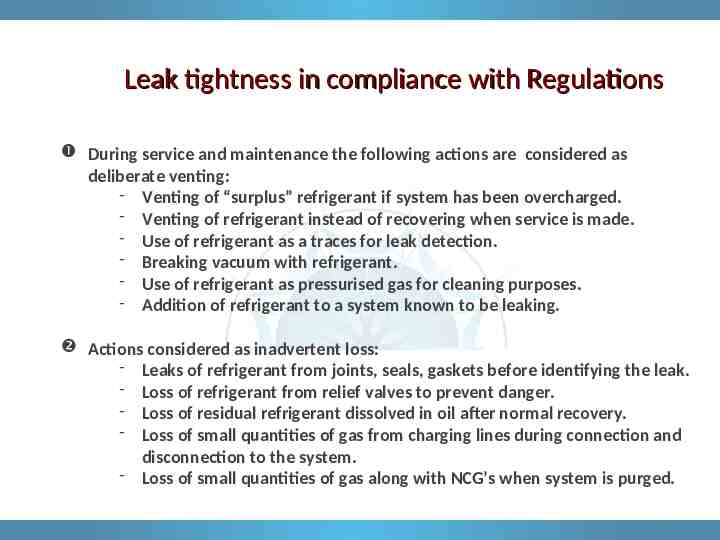
Leak tightness in compliance with Regulations During service and maintenance the following actions are considered as deliberate venting: - Venting of “surplus” refrigerant if system has been overcharged. - Venting of refrigerant instead of recovering when service is made. - Use of refrigerant as a traces for leak detection. - Breaking vacuum with refrigerant. - Use of refrigerant as pressurised gas for cleaning purposes. - Addition of refrigerant to a system known to be leaking. Actions considered as inadvertent loss: - Leaks of refrigerant from joints, seals, gaskets before identifying the leak. - Loss of refrigerant from relief valves to prevent danger. - Loss of residual refrigerant dissolved in oil after normal recovery. - Loss of small quantities of gas from charging lines during connection and disconnection to the system. - Loss of small quantities of gas along with NCG’s when system is purged.
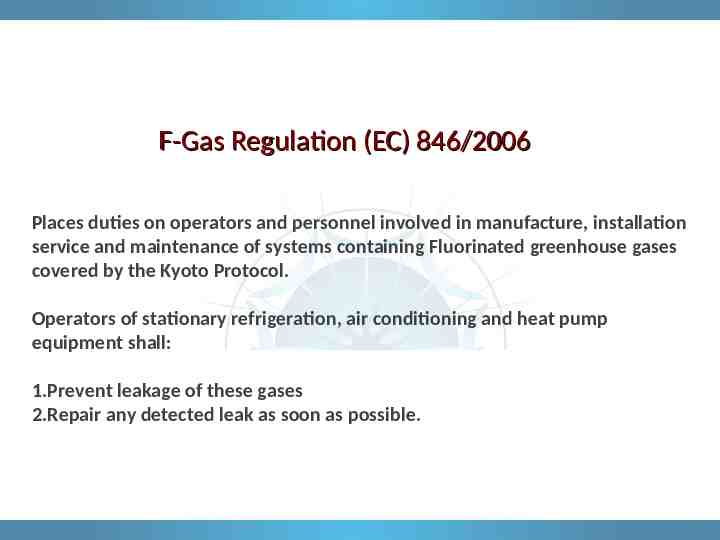
F-Gas Regulation (EC) 846/2006 Places duties on operators and personnel involved in manufacture, installation service and maintenance of systems containing Fluorinated greenhouse gases covered by the Kyoto Protocol. Operators of stationary refrigeration, air conditioning and heat pump equipment shall: 1.Prevent leakage of these gases 2.Repair any detected leak as soon as possible.
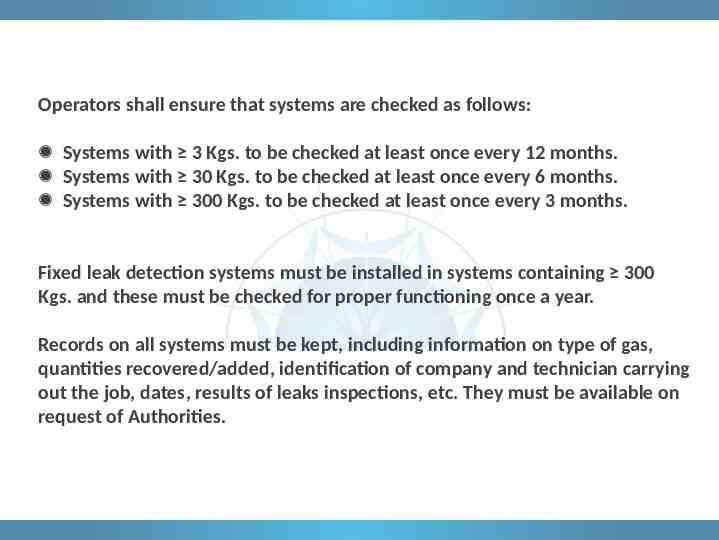
Operators shall ensure that systems are checked as follows: Systems with 3 Kgs. to be checked at least once every 12 months. Systems with 30 Kgs. to be checked at least once every 6 months. Systems with 300 Kgs. to be checked at least once every 3 months. Fixed leak detection systems must be installed in systems containing 300 Kgs. and these must be checked for proper functioning once a year. Records on all systems must be kept, including information on type of gas, quantities recovered/added, identification of company and technician carrying out the job, dates, results of leaks inspections, etc. They must be available on request of Authorities.
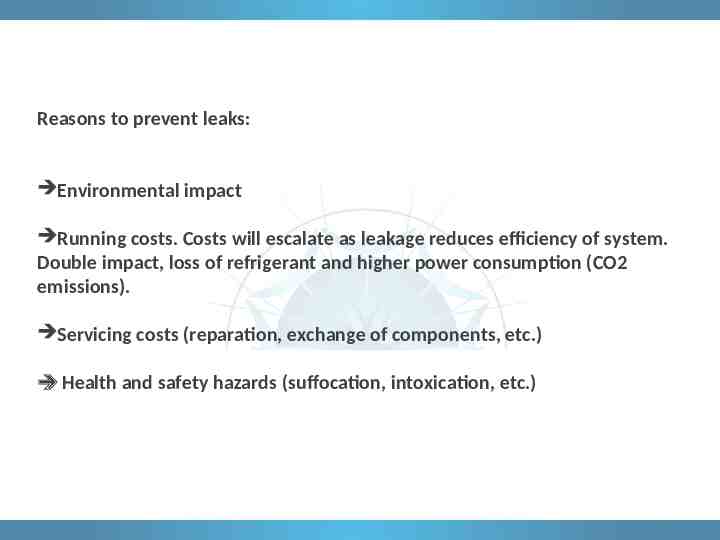
Reasons to prevent leaks: Environmental impact Running costs. Costs will escalate as leakage reduces efficiency of system. Double impact, loss of refrigerant and higher power consumption (CO2 emissions). Servicing costs (reparation, exchange of components, etc.) Health and safety hazards (suffocation, intoxication, etc.)
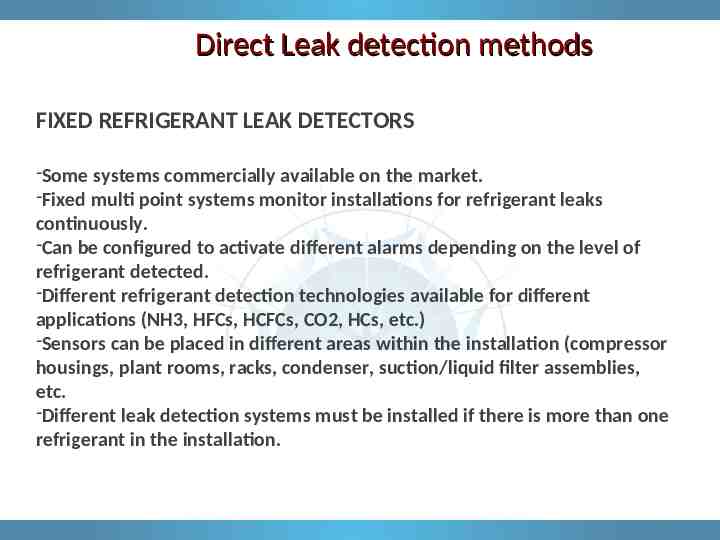
Direct Leak detection methods FIXED REFRIGERANT LEAK DETECTORS -Some systems commercially available on the market. -Fixed multi point systems monitor installations for refrigerant leaks continuously. -Can be configured to activate different alarms depending on the level of refrigerant detected. -Different refrigerant detection technologies available for different applications (NH3, HFCs, HCFCs, CO2, HCs, etc.) -Sensors can be placed in different areas within the installation (compressor housings, plant rooms, racks, condenser, suction/liquid filter assemblies, etc. -Different leak detection systems must be installed if there is more than one refrigerant in the installation.
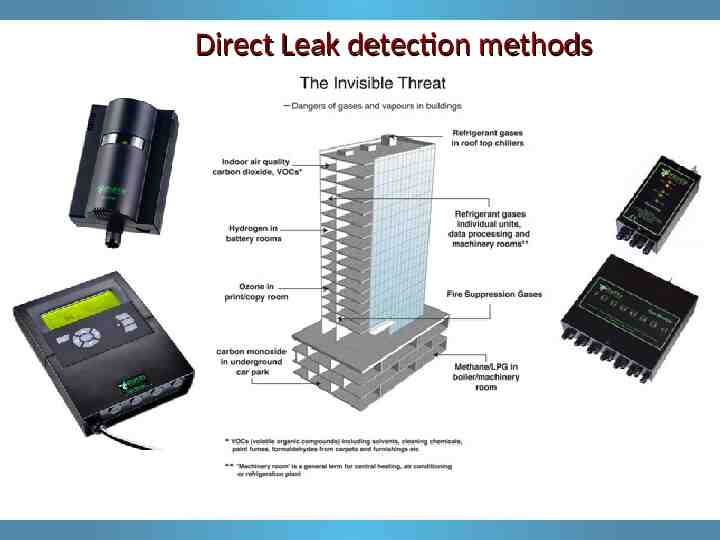
Direct Leak detection methods
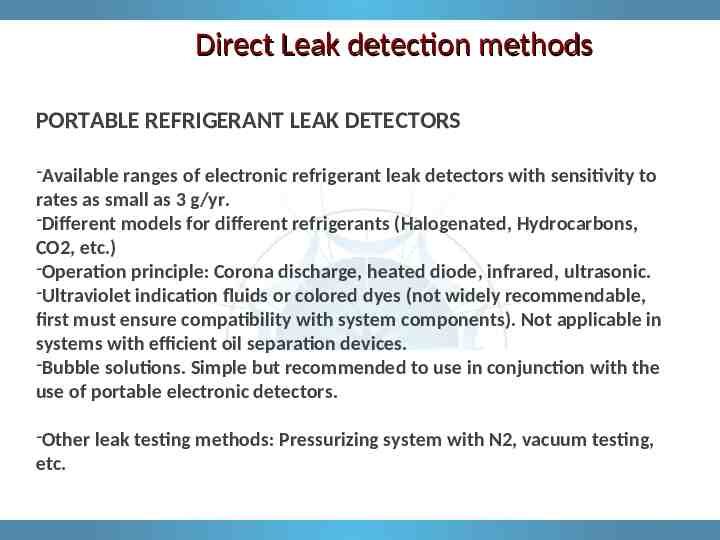
Direct Leak detection methods PORTABLE REFRIGERANT LEAK DETECTORS -Available ranges of electronic refrigerant leak detectors with sensitivity to rates as small as 3 g/yr. -Different models for different refrigerants (Halogenated, Hydrocarbons, CO2, etc.) -Operation principle: Corona discharge, heated diode, infrared, ultrasonic. -Ultraviolet indication fluids or colored dyes (not widely recommendable, first must ensure compatibility with system components). Not applicable in systems with efficient oil separation devices. -Bubble solutions. Simple but recommended to use in conjunction with the use of portable electronic detectors. -Other leak testing methods: Pressurizing system with N2, vacuum testing, etc.
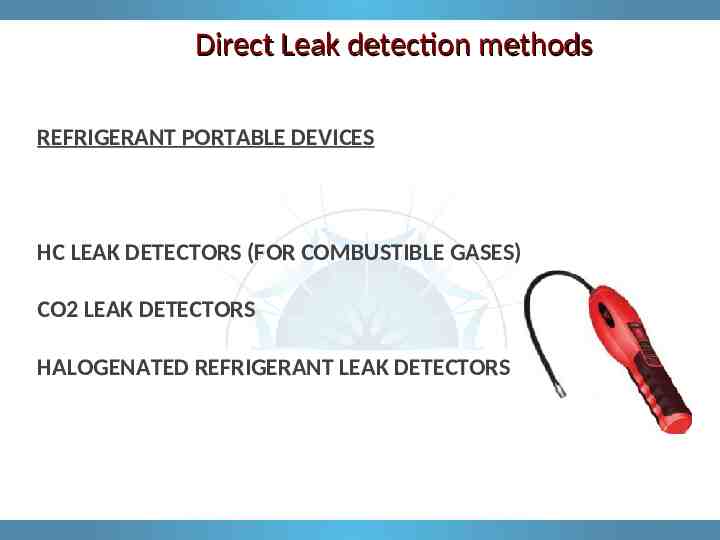
Direct Leak detection methods REFRIGERANT PORTABLE DEVICES HC LEAK DETECTORS (FOR COMBUSTIBLE GASES) CO2 LEAK DETECTORS HALOGENATED REFRIGERANT LEAK DETECTORS
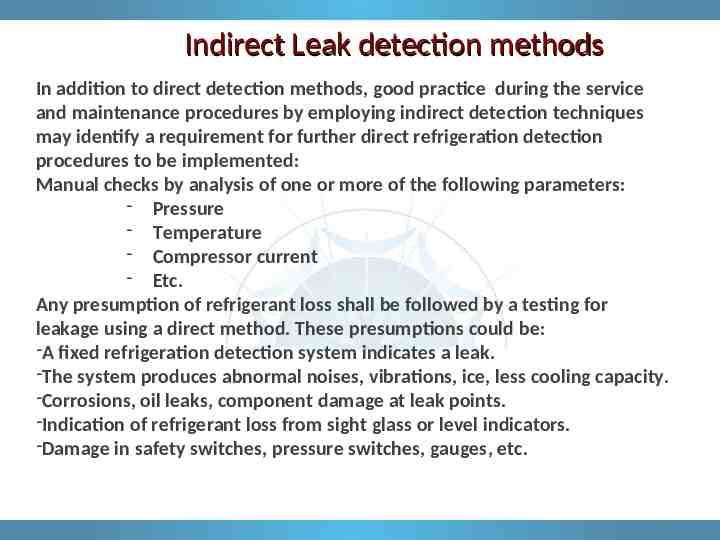
Indirect Leak detection methods In addition to direct detection methods, good practice during the service and maintenance procedures by employing indirect detection techniques may identify a requirement for further direct refrigeration detection procedures to be implemented: Manual checks by analysis of one or more of the following parameters: - Pressure - Temperature - Compressor current - Etc. Any presumption of refrigerant loss shall be followed by a testing for leakage using a direct method. These presumptions could be: -A fixed refrigeration detection system indicates a leak. -The system produces abnormal noises, vibrations, ice, less cooling capacity. -Corrosions, oil leaks, component damage at leak points. -Indication of refrigerant loss from sight glass or level indicators. -Damage in safety switches, pressure switches, gauges, etc.
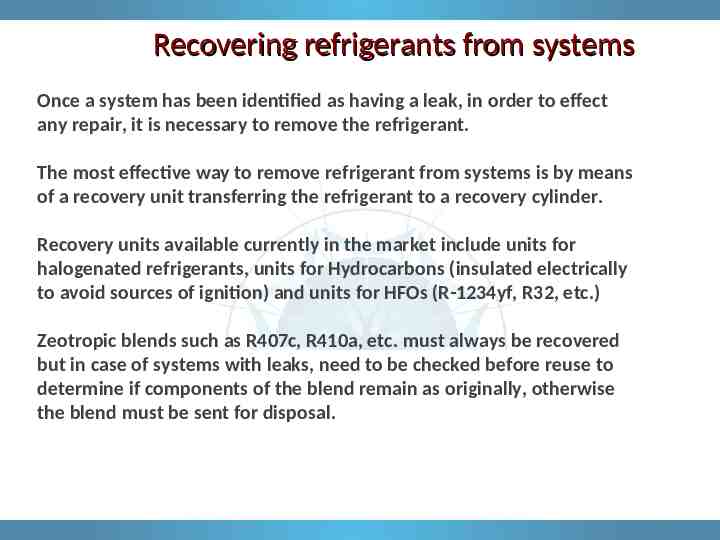
Recovering refrigerants from systems Once a system has been identified as having a leak, in order to effect any repair, it is necessary to remove the refrigerant. The most effective way to remove refrigerant from systems is by means of a recovery unit transferring the refrigerant to a recovery cylinder. Recovery units available currently in the market include units for halogenated refrigerants, units for Hydrocarbons (insulated electrically to avoid sources of ignition) and units for HFOs (R-1234yf, R32, etc.) Zeotropic blends such as R407c, R410a, etc. must always be recovered but in case of systems with leaks, need to be checked before reuse to determine if components of the blend remain as originally, otherwise the blend must be sent for disposal.

Recovering refrigerants from systems Recovery unit for Halogenated refrigerants Recovery unit for HCs and HFOs
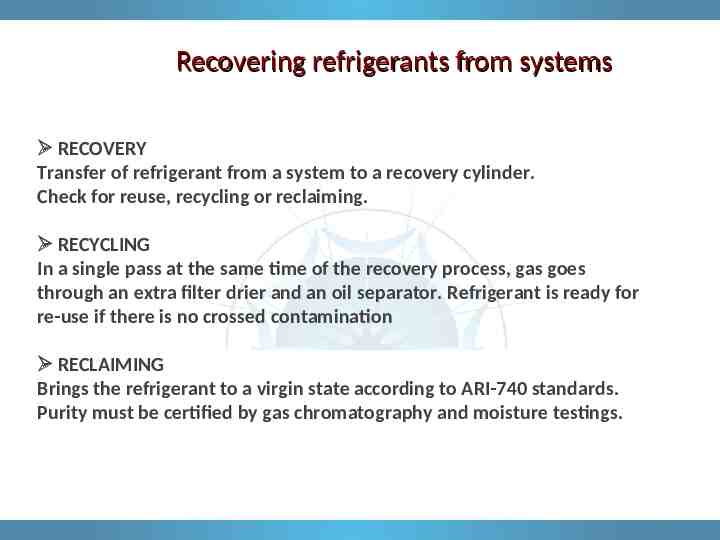
Recovering refrigerants from systems RECOVERY Transfer of refrigerant from a system to a recovery cylinder. Check for reuse, recycling or reclaiming. RECYCLING In a single pass at the same time of the recovery process, gas goes through an extra filter drier and an oil separator. Refrigerant is ready for re-use if there is no crossed contamination RECLAIMING Brings the refrigerant to a virgin state according to ARI-740 standards. Purity must be certified by gas chromatography and moisture testings.
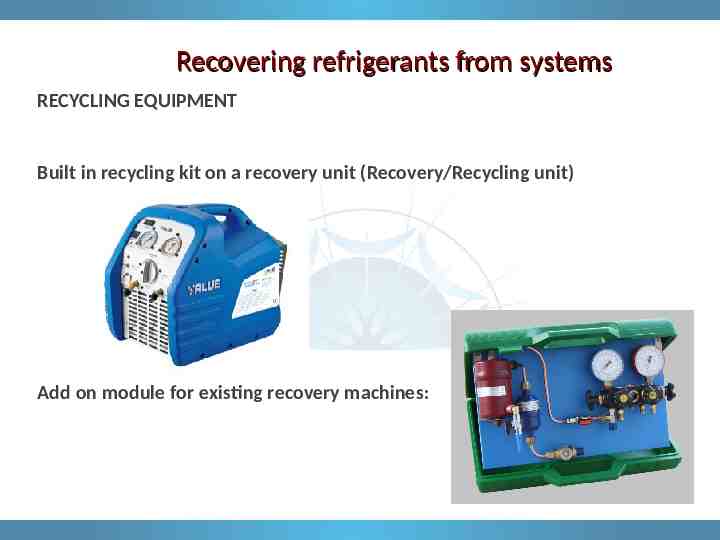
Recovering refrigerants from systems RECYCLING EQUIPMENT Built in recycling kit on a recovery unit (Recovery/Recycling unit) Add on module for existing recovery machines:
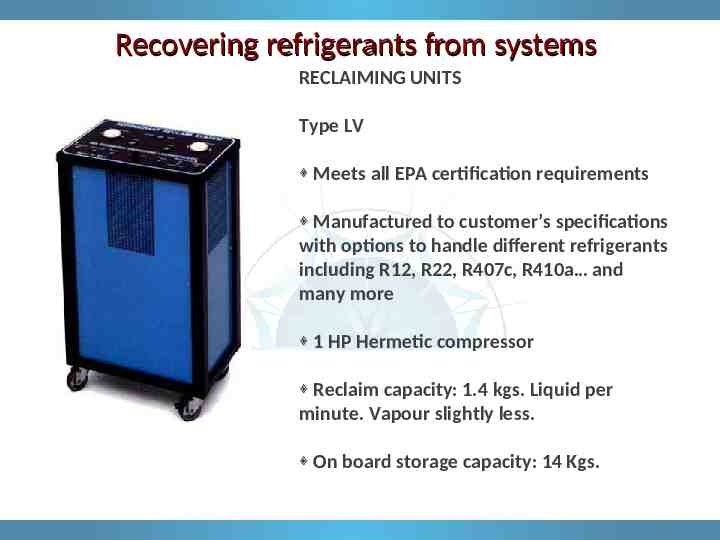
Recovering refrigerants from systems RECLAIMING UNITS Type LV Meets all EPA certification requirements Manufactured to customer’s specifications with options to handle different refrigerants including R12, R22, R407c, R410a and many more 1 HP Hermetic compressor Reclaim capacity: 1.4 kgs. Liquid per minute. Vapour slightly less. On board storage capacity: 14 Kgs.
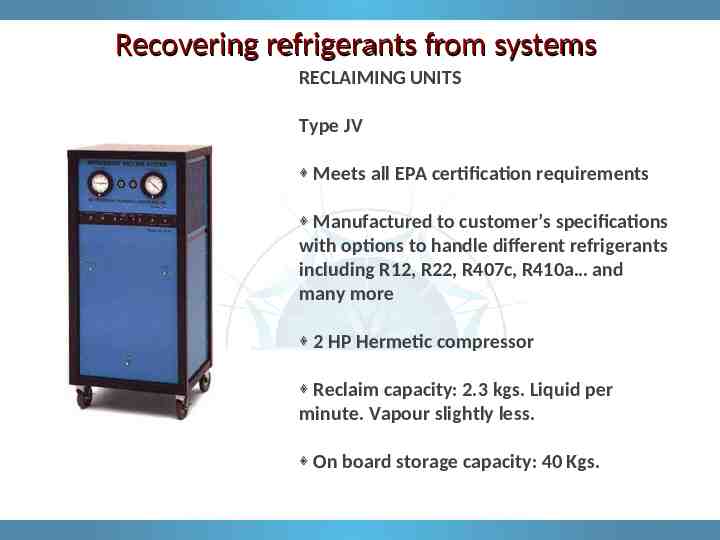
Recovering refrigerants from systems RECLAIMING UNITS Type JV Meets all EPA certification requirements Manufactured to customer’s specifications with options to handle different refrigerants including R12, R22, R407c, R410a and many more 2 HP Hermetic compressor Reclaim capacity: 2.3 kgs. Liquid per minute. Vapour slightly less. On board storage capacity: 40 Kgs.
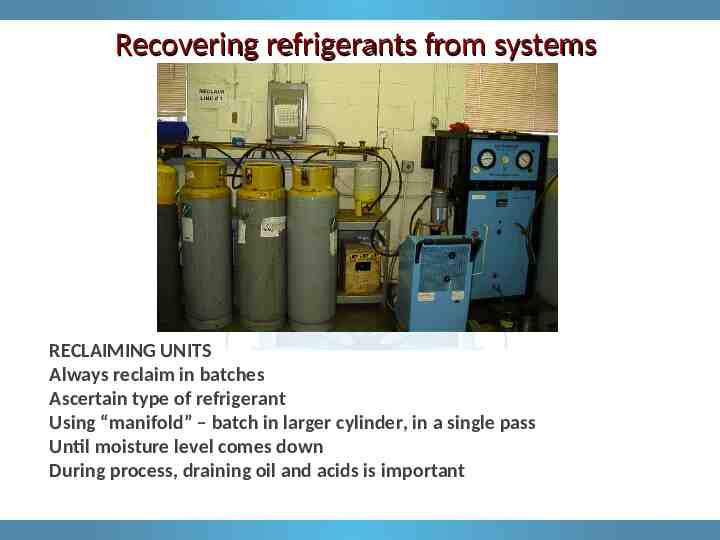
Recovering refrigerants from systems RECLAIMING UNITS Always reclaim in batches Ascertain type of refrigerant Using “manifold” – batch in larger cylinder, in a single pass Until moisture level comes down During process, draining oil and acids is important
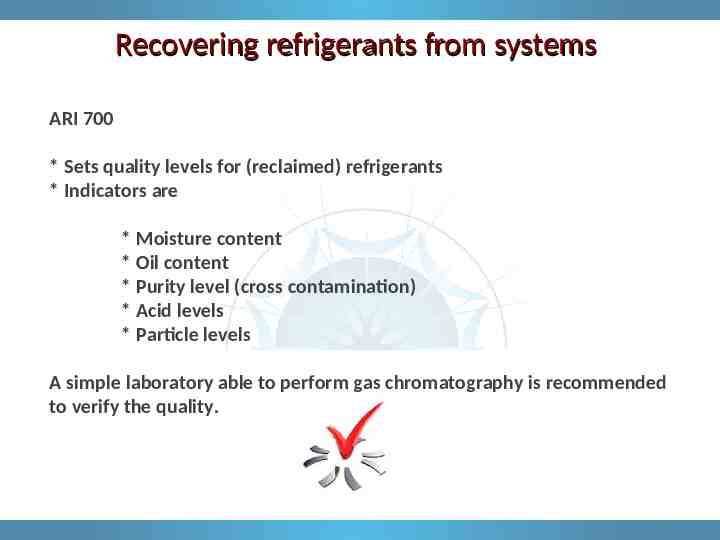
Recovering refrigerants from systems ARI 700 * Sets quality levels for (reclaimed) refrigerants * Indicators are * Moisture content * Oil content * Purity level (cross contamination) * Acid levels * Particle levels A simple laboratory able to perform gas chromatography is recommended to verify the quality.
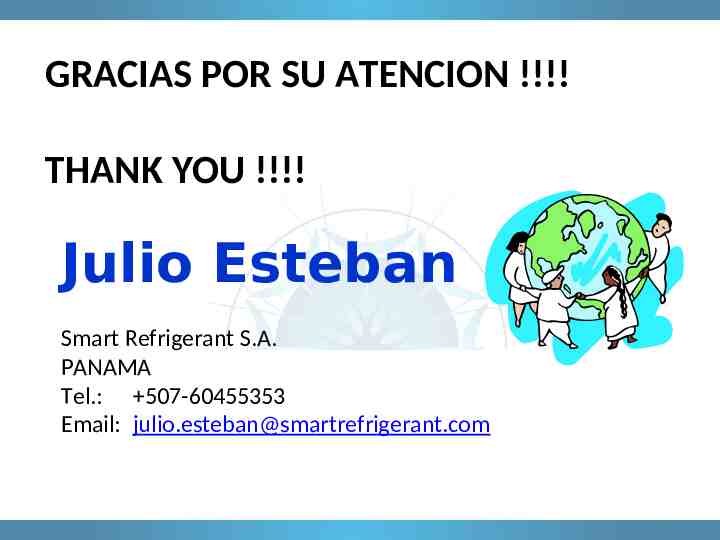
GRACIAS POR SU ATENCION !!!! THANK YOU !!!! Julio Esteban Smart Refrigerant S.A. PANAMA Tel.: 507-60455353 Email: [email protected]