A multi criteria decision making model for vehicle routing problem in
15 Slides272.75 KB
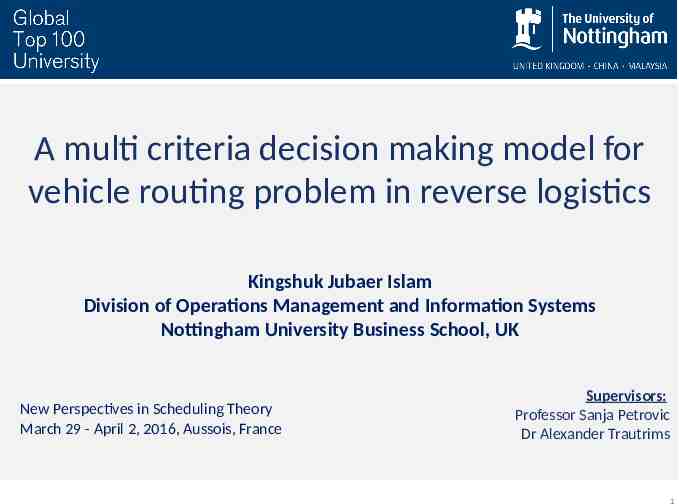
A multi criteria decision making model for vehicle routing problem in reverse logistics Kingshuk Jubaer Islam Division of Operations Management and Information Systems Nottingham University Business School, UK New Perspectives in Scheduling Theory March 29 - April 2, 2016, Aussois, France Supervisors: Professor Sanja Petrovic Dr Alexander Trautrims 1
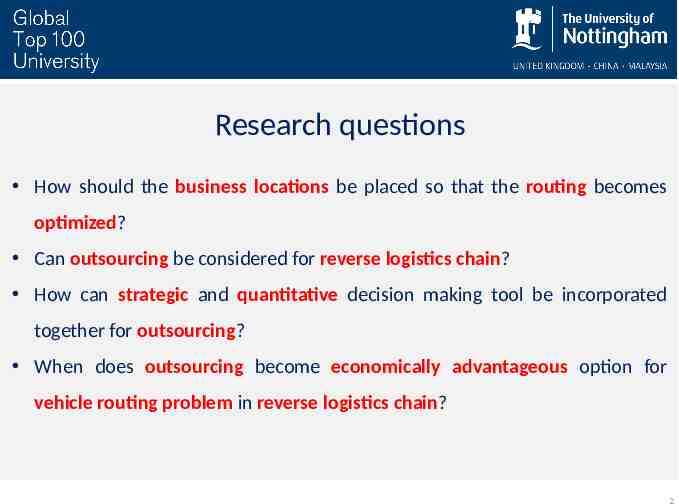
Research questions How should the business locations be placed so that the routing becomes optimized? Can outsourcing be considered for reverse logistics chain? How can strategic and quantitative decision making tool be incorporated together for outsourcing? When does outsourcing become economically advantageous option for vehicle routing problem in reverse logistics chain? 2
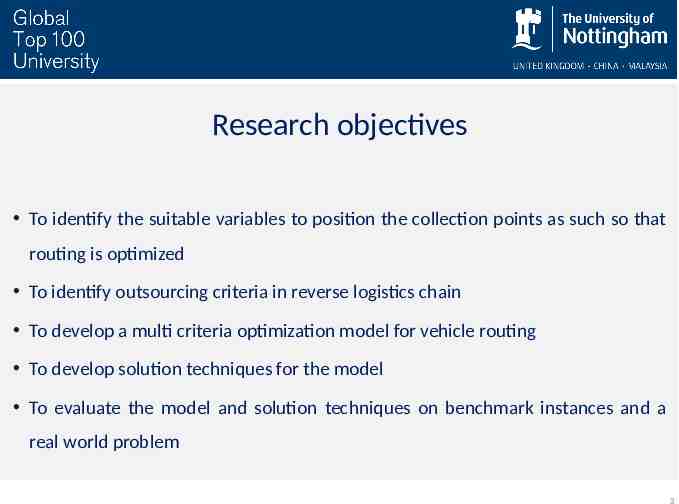
Research objectives To identify the suitable variables to position the collection points as such so that routing is optimized To identify outsourcing criteria in reverse logistics chain To develop a multi criteria optimization model for vehicle routing To develop solution techniques for the model To evaluate the model and solution techniques on benchmark instances and a real world problem 3
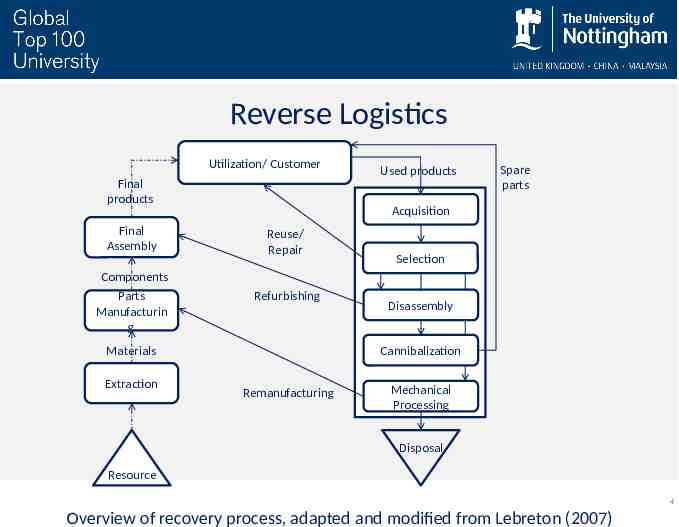
Reverse Logistics Utilization/ Customer Final products Spare parts Acquisition Final Assembly Reuse/ Repair Components Parts Manufacturin g Refurbishing Materials Extraction Used products Selection Disassembly Cannibalization Remanufacturing Mechanical Processing Disposal Resource 4 Overview of recovery process, adapted and modified from Lebreton (2007)
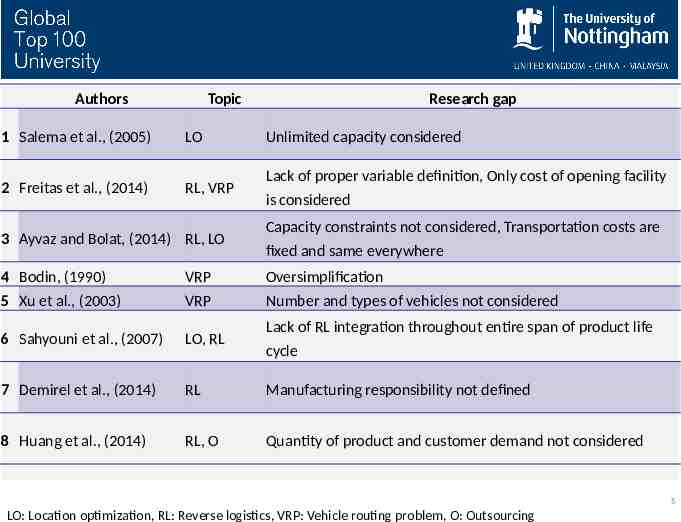
Authors Topic Research gap 1 Salema et al., (2005) LO Unlimited capacity considered 2 Freitas et al., (2014) RL, VRP Lack of proper variable definition, Only cost of opening facility is considered 3 Ayvaz and Bolat, (2014) RL, LO Capacity constraints not considered, Transportation costs are fixed and same everywhere 4 Bodin, (1990) VRP Oversimplification 5 Xu et al., (2003) VRP Number and types of vehicles not considered 6 Sahyouni et al., (2007) LO, RL Lack of RL integration throughout entire span of product life cycle 7 Demirel et al., (2014) RL Manufacturing responsibility not defined 8 Huang et al., (2014) RL, O Quantity of product and customer demand not considered 5 LO: Location optimization, RL: Reverse logistics, VRP: Vehicle routing problem, O: Outsourcing
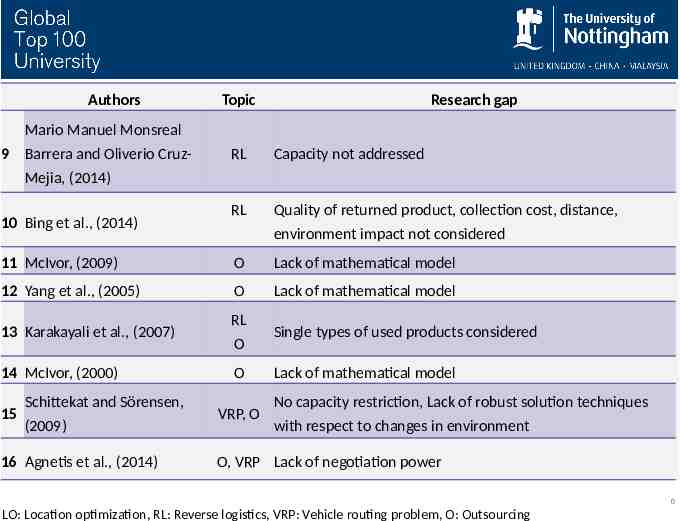
Authors Topic Research gap Mario Manuel Monsreal 9 Barrera and Oliverio CruzMejia, (2014) RL Capacity not addressed RL Quality of returned product, collection cost, distance, environment impact not considered 11 McIvor, (2009) O Lack of mathematical model 12 Yang et al., (2005) O Lack of mathematical model 13 Karakayali et al., (2007) RL O Single types of used products considered 14 McIvor, (2000) O Lack of mathematical model 10 Bing et al., (2014) 15 Schittekat and Sörensen, (2009) 16 Agnetis et al., (2014) VRP, O No capacity restriction, Lack of robust solution techniques with respect to changes in environment O, VRP Lack of negotiation power 6 LO: Location optimization, RL: Reverse logistics, VRP: Vehicle routing problem, O: Outsourcing
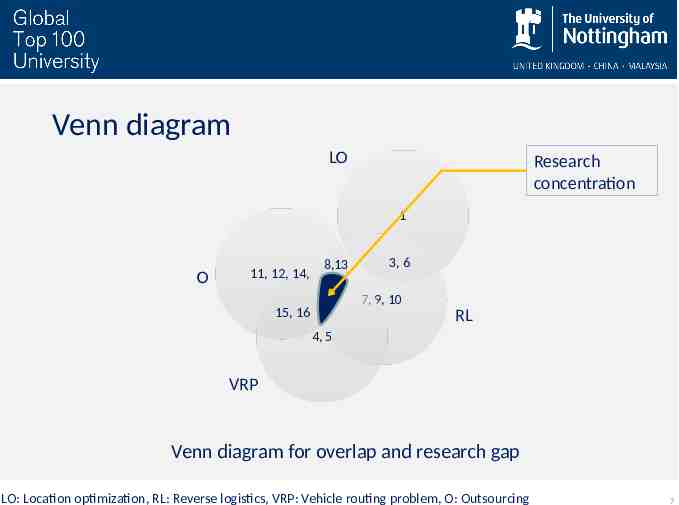
Venn diagram LO Research concentration 1 O 11, 12, 14, 8,13 3, 6 7, 9, 10 15, 16 RL 4, 5 VRP Venn diagram for overlap and research gap LO: Location optimization, RL: Reverse logistics, VRP: Vehicle routing problem, O: Outsourcing 7
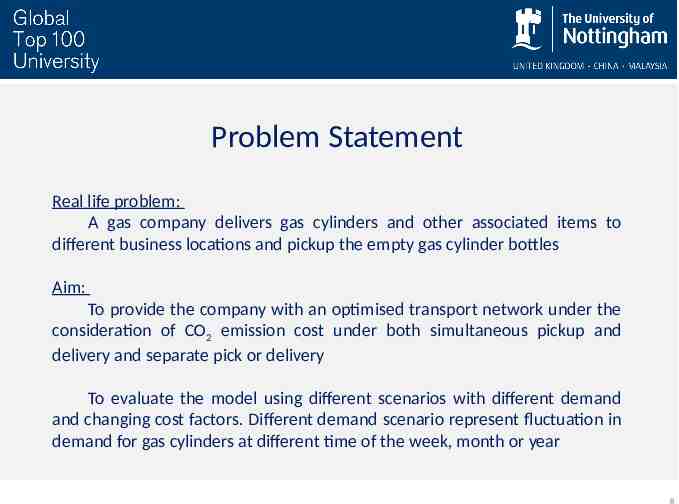
Problem Statement Real life problem: A gas company delivers gas cylinders and other associated items to different business locations and pickup the empty gas cylinder bottles Aim: To provide the company with an optimised transport network under the consideration of CO2 emission cost under both simultaneous pickup and delivery and separate pick or delivery To evaluate the model using different scenarios with different demand and changing cost factors. Different demand scenario represent fluctuation in demand for gas cylinders at different time of the week, month or year 8
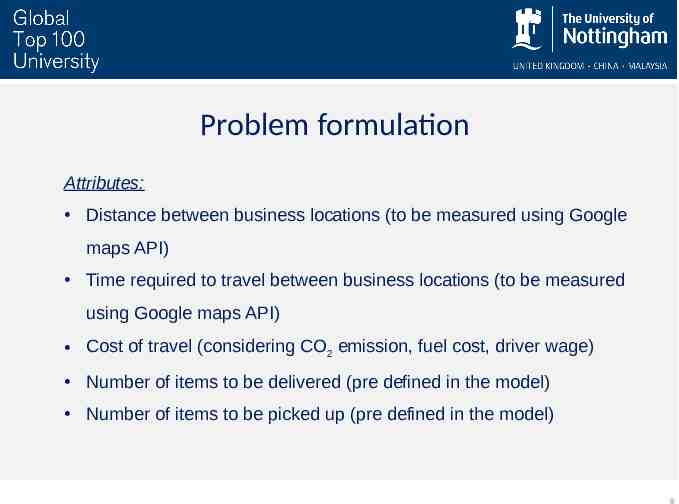
Problem formulation Attributes: Distance between business locations (to be measured using Google maps API) Time required to travel between business locations (to be measured using Google maps API) Cost of travel (considering CO2 emission, fuel cost, driver wage) Number of items to be delivered (pre defined in the model) Number of items to be picked up (pre defined in the model) 9
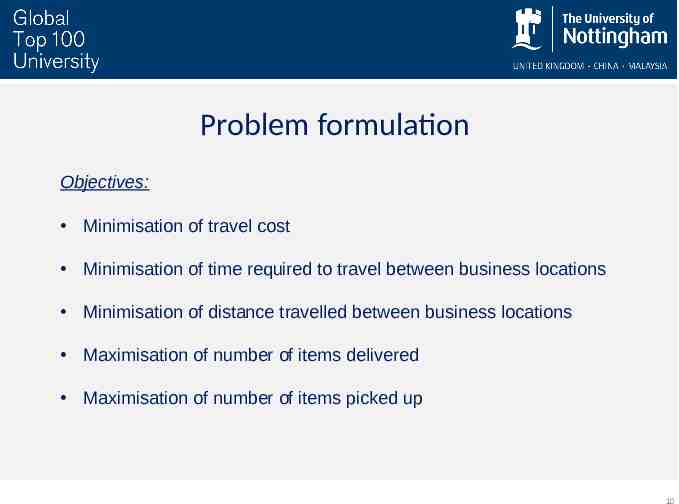
Problem formulation Objectives: Minimisation of travel cost Minimisation of time required to travel between business locations Minimisation of distance travelled between business locations Maximisation of number of items delivered Maximisation of number of items picked up 10
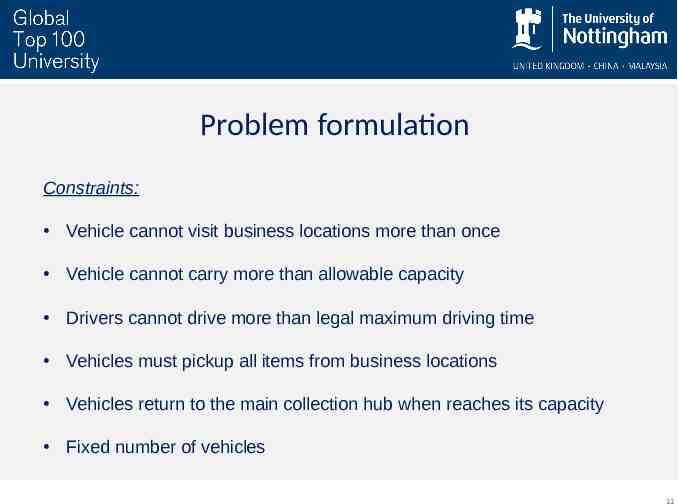
Problem formulation Constraints: Vehicle cannot visit business locations more than once Vehicle cannot carry more than allowable capacity Drivers cannot drive more than legal maximum driving time Vehicles must pickup all items from business locations Vehicles return to the main collection hub when reaches its capacity Fixed number of vehicles 11
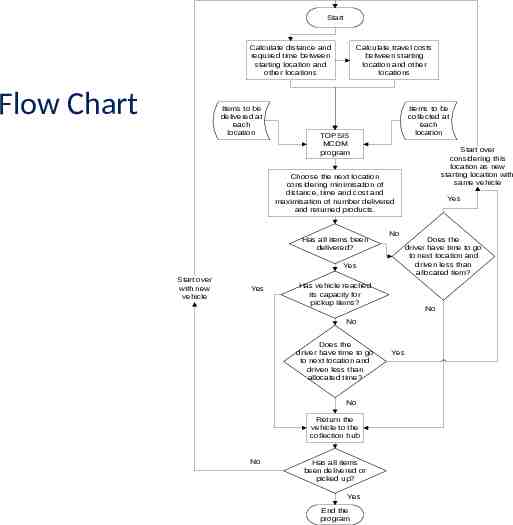
Start Calculate distance and required time between starting location and other locations Flow Chart Items to be delivered at each location Calculate travel costs between starting location and other locations Items to be collected at each location TOPSIS MCDM program Start over considering this location as new starting location with same vehicle Choose the next location considering minimisation of distance, time and cost and maximisation of number delivered and returned products. Has all items been delivered? No Yes Start over with new vehicle Yes Has vehicle reached its capacity for pickup items? No Return the vehicle to the collection hub No Has all items been delivered or picked up? Yes End the program Does the driver have time to go to next location and driven less than allocated tiem? No No Does the driver have time to go to next location and Yes driven less than allocated time? Yes Yes
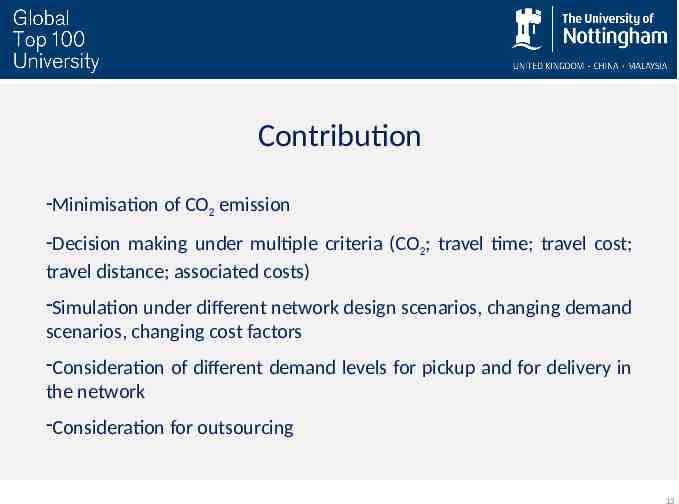
Contribution -Minimisation of CO2 emission -Decision making under multiple criteria (CO2; travel time; travel cost; travel distance; associated costs) -Simulation under different network design scenarios, changing demand scenarios, changing cost factors -Consideration of different demand levels for pickup and for delivery in the network -Consideration for outsourcing 13
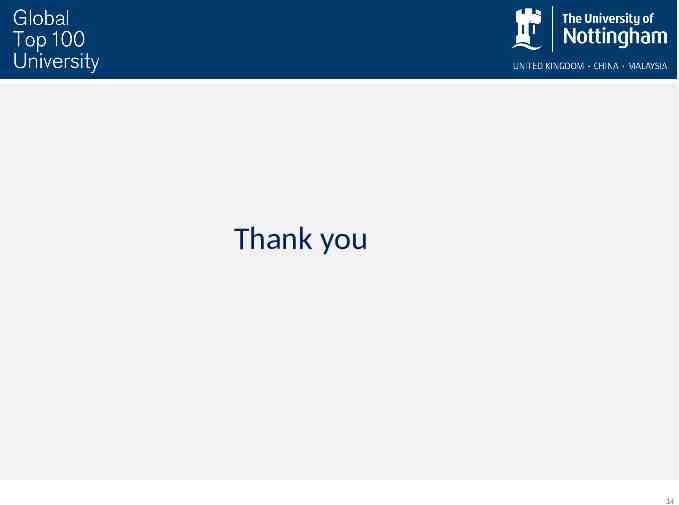
Thank you 14
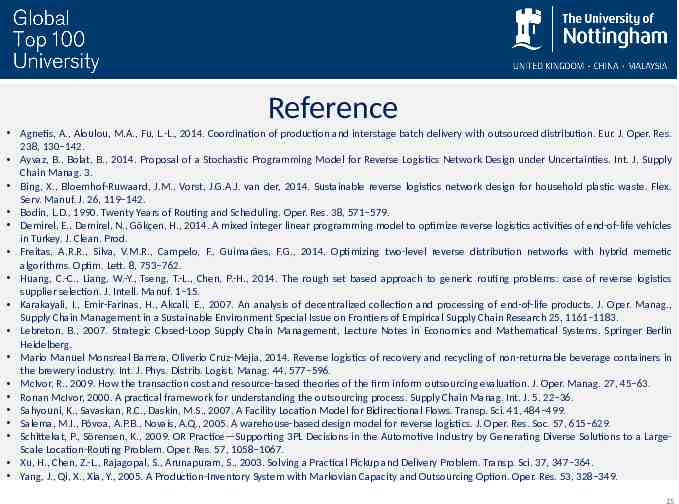
Reference Agnetis, A., Aloulou, M.A., Fu, L.-L., 2014. Coordination of production and interstage batch delivery with outsourced distribution. Eur. J. Oper. Res. 238, 130–142. Ayvaz, B., Bolat, B., 2014. Proposal of a Stochastic Programming Model for Reverse Logistics Network Design under Uncertainties. Int. J. Supply Chain Manag. 3. Bing, X., Bloemhof-Ruwaard, J.M., Vorst, J.G.A.J. van der, 2014. Sustainable reverse logistics network design for household plastic waste. Flex. Serv. Manuf. J. 26, 119–142. Bodin, L.D., 1990. Twenty Years of Routing and Scheduling. Oper. Res. 38, 571–579. Demirel, E., Demirel, N., Gökçen, H., 2014. A mixed integer linear programming model to optimize reverse logistics activities of end-of-life vehicles in Turkey. J. Clean. Prod. Freitas, A.R.R., Silva, V.M.R., Campelo, F., Guimarães, F.G., 2014. Optimizing two-level reverse distribution networks with hybrid memetic algorithms. Optim. Lett. 8, 753–762. Huang, C.-C., Liang, W.-Y., Tseng, T.-L., Chen, P.-H., 2014. The rough set based approach to generic routing problems: case of reverse logistics supplier selection. J. Intell. Manuf. 1–15. Karakayali, I., Emir-Farinas, H., Akcali, E., 2007. An analysis of decentralized collection and processing of end-of-life products. J. Oper. Manag., Supply Chain Management in a Sustainable Environment Special Issue on Frontiers of Empirical Supply Chain Research 25, 1161–1183. Lebreton, B., 2007. Strategic Closed-Loop Supply Chain Management, Lecture Notes in Economics and Mathematical Systems. Springer Berlin Heidelberg. Mario Manuel Monsreal Barrera, Oliverio Cruz-Mejia, 2014. Reverse logistics of recovery and recycling of non-returnable beverage containers in the brewery industry. Int. J. Phys. Distrib. Logist. Manag. 44, 577–596. McIvor, R., 2009. How the transaction cost and resource-based theories of the firm inform outsourcing evaluation. J. Oper. Manag. 27, 45–63. Ronan McIvor, 2000. A practical framework for understanding the outsourcing process. Supply Chain Manag. Int. J. 5, 22–36. Sahyouni, K., Savaskan, R.C., Daskin, M.S., 2007. A Facility Location Model for Bidirectional Flows. Transp. Sci. 41, 484–499. Salema, M.I., Póvoa, A.P.B., Novais, A.Q., 2005. A warehouse-based design model for reverse logistics. J. Oper. Res. Soc. 57, 615–629. Schittekat, P., Sörensen, K., 2009. OR Practice—Supporting 3PL Decisions in the Automotive Industry by Generating Diverse Solutions to a LargeScale Location-Routing Problem. Oper. Res. 57, 1058–1067. Xu, H., Chen, Z.-L., Rajagopal, S., Arunapuram, S., 2003. Solving a Practical Pickup and Delivery Problem. Transp. Sci. 37, 347–364. Yang, J., Qi, X., Xia, Y., 2005. A Production-Inventory System with Markovian Capacity and Outsourcing Option. Oper. Res. 53, 328–349. 15