Managing Safety&Health in Construction Bureau of Workers’ Compensation
54 Slides5.38 MB
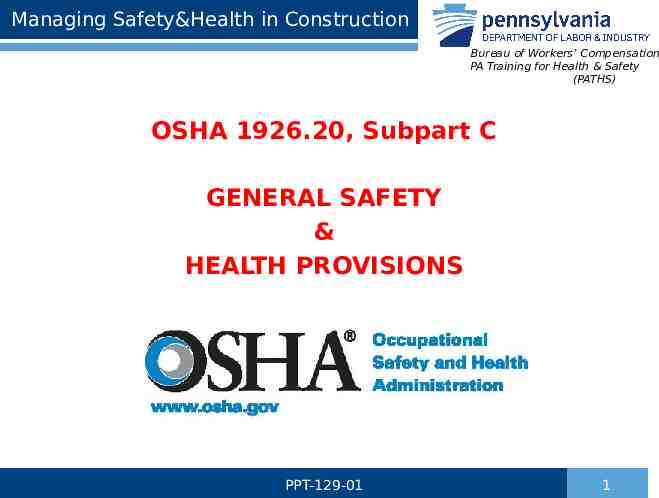
Managing Safety&Health in Construction Bureau of Workers’ Compensation PA Training for Health & Safety (PATHS) OSHA 1926.20, Subpart C GENERAL SAFETY & HEALTH PROVISIONS PPT-129-01 1
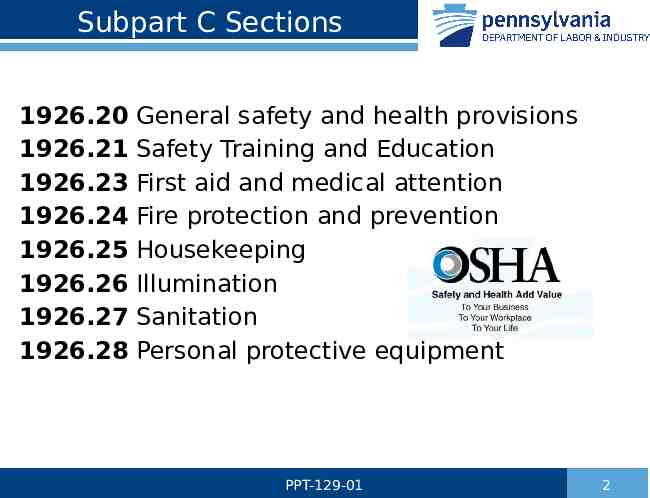
Subpart C Sections 1926.20 1926.21 1926.23 1926.24 1926.25 1926.26 1926.27 1926.28 General safety and health provisions Safety Training and Education First aid and medical attention Fire protection and prevention Housekeeping Illumination Sanitation Personal protective equipment PPT-129-01 2
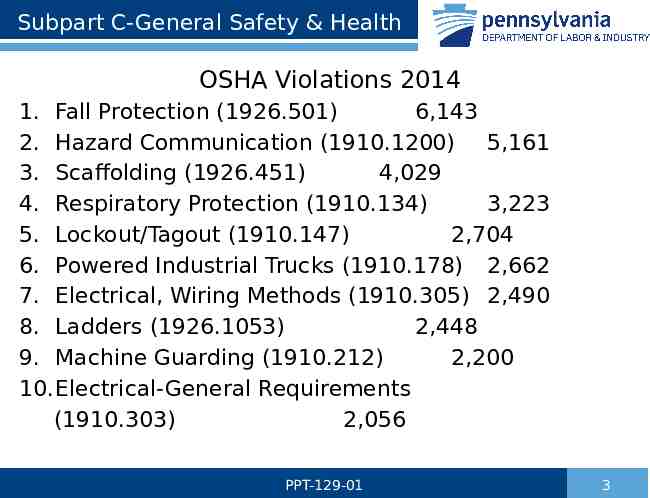
Subpart C-General Safety & Health OSHA Violations 2014 1. Fall Protection (1926.501) 6,143 2. Hazard Communication (1910.1200) 5,161 3. Scaffolding (1926.451) 4,029 4. Respiratory Protection (1910.134) 3,223 5. Lockout/Tagout (1910.147) 2,704 6. Powered Industrial Trucks (1910.178) 2,662 7. Electrical, Wiring Methods (1910.305) 2,490 8. Ladders (1926.1053) 2,448 9. Machine Guarding (1910.212) 2,200 10.Electrical-General Requirements (1910.303) 2,056 PPT-129-01 3
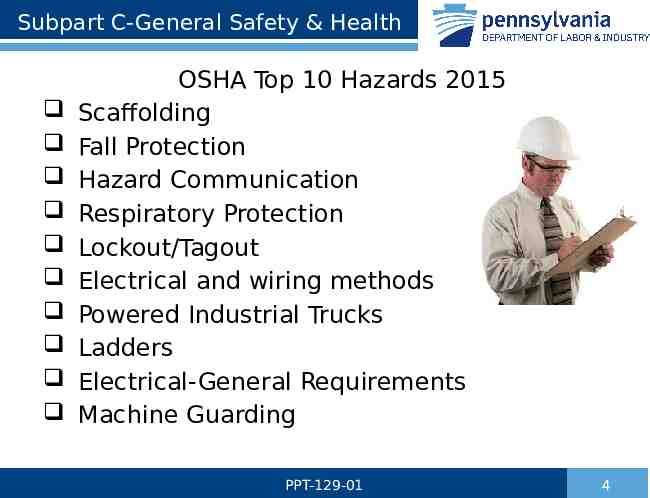
Subpart C-General Safety & Health OSHA Top 10 Hazards 2015 Scaffolding Fall Protection Hazard Communication Respiratory Protection Lockout/Tagout Electrical and wiring methods Powered Industrial Trucks Ladders Electrical-General Requirements Machine Guarding PPT-129-01 4
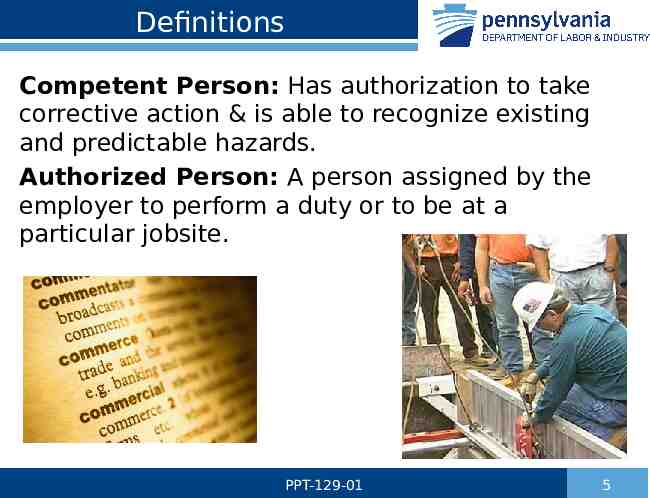
Definitions Competent Person: Has authorization to take corrective action & is able to recognize existing and predictable hazards. Authorized Person: A person assigned by the employer to perform a duty or to be at a particular jobsite. PPT-129-01 5
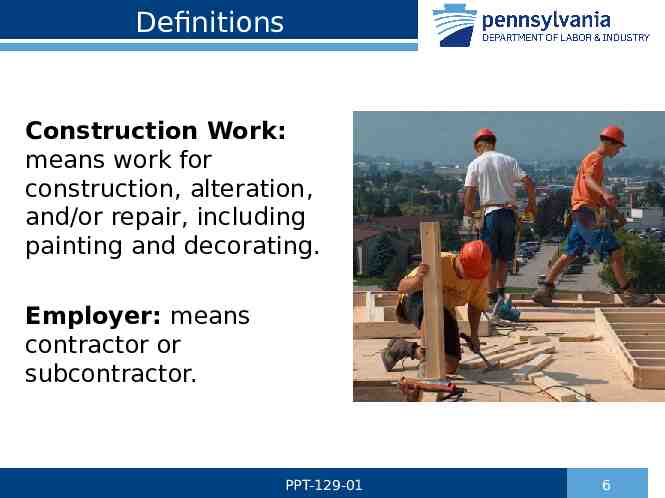
Definitions Construction Work: means work for construction, alteration, and/or repair, including painting and decorating. Employer: means contractor or subcontractor. PPT-129-01 6
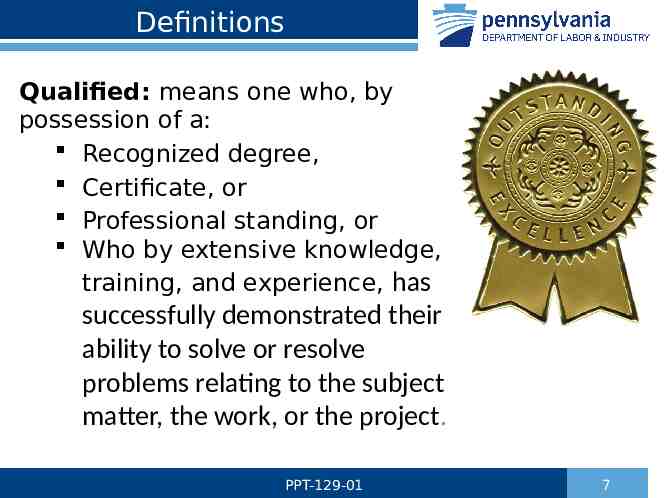
Definitions Qualified: means one who, by possession of a: Recognized degree, Certificate, or Professional standing, or Who by extensive knowledge, training, and experience, has successfully demonstrated their ability to solve or resolve problems relating to the subject matter, the work, or the project. PPT-129-01 7
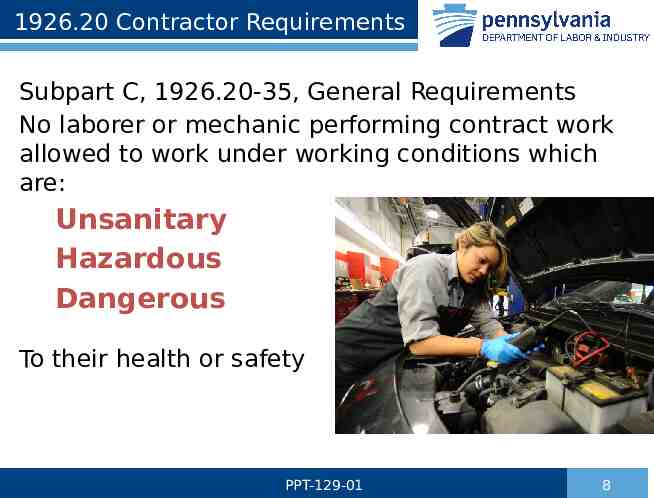
1926.20 Contractor Requirements Subpart C, 1926.20-35, General Requirements No laborer or mechanic performing contract work allowed to work under working conditions which are: Unsanitary Hazardous Dangerous To their health or safety PPT-129-01 8
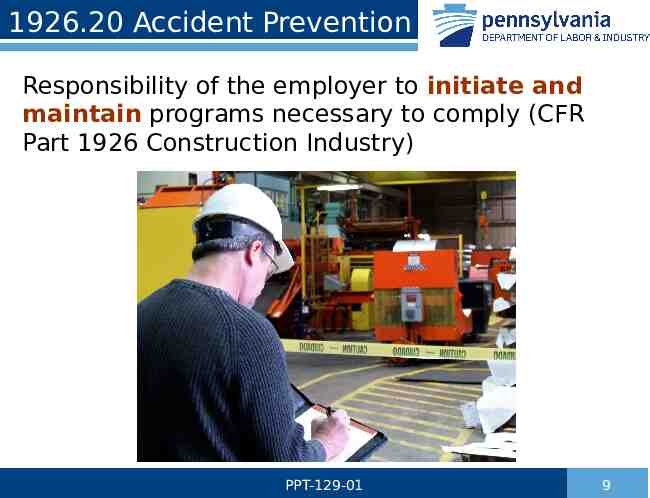
1926.20 Accident Prevention Responsibility of the employer to initiate and maintain programs necessary to comply (CFR Part 1926 Construction Industry) PPT-129-01 9
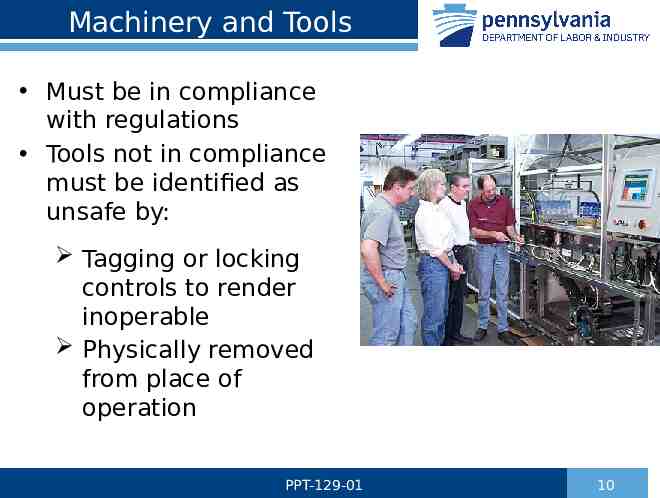
Machinery and Tools Must be in compliance with regulations Tools not in compliance must be identified as unsafe by: Tagging or locking controls to render inoperable Physically removed from place of operation PPT-129-01 10
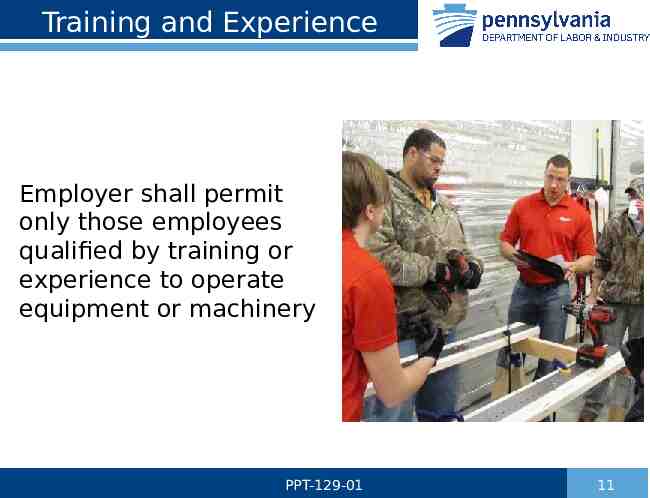
Training and Experience Employer shall permit only those employees qualified by training or experience to operate equipment or machinery PPT-129-01 11
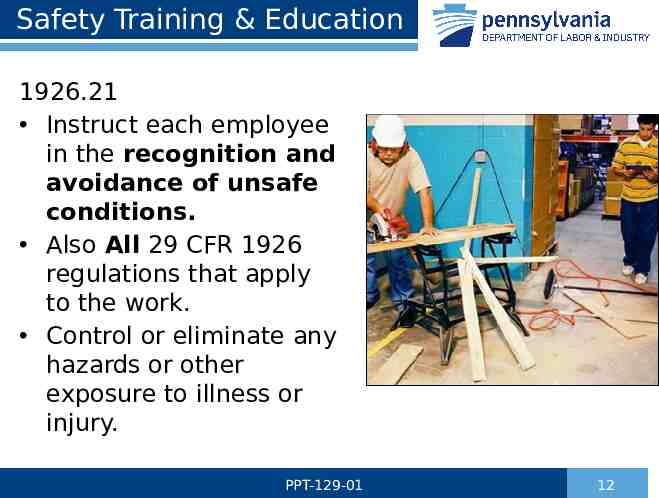
Safety Training & Education 1926.21 Instruct each employee in the recognition and avoidance of unsafe conditions. Also All 29 CFR 1926 regulations that apply to the work. Control or eliminate any hazards or other exposure to illness or injury. PPT-129-01 12
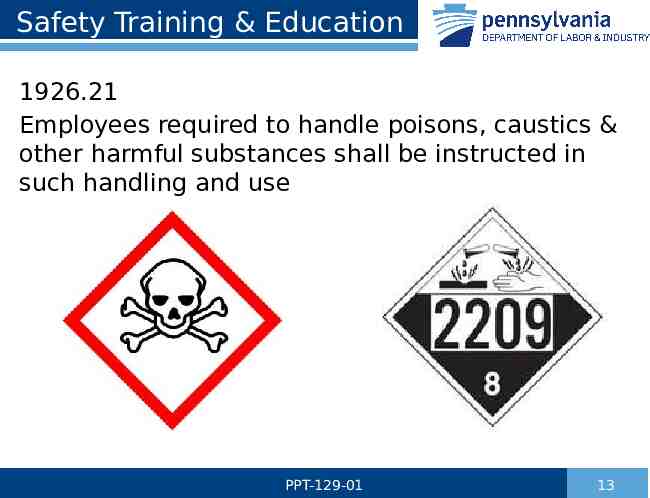
Safety Training & Education 1926.21 Employees required to handle poisons, caustics & other harmful substances shall be instructed in such handling and use PPT-129-01 13
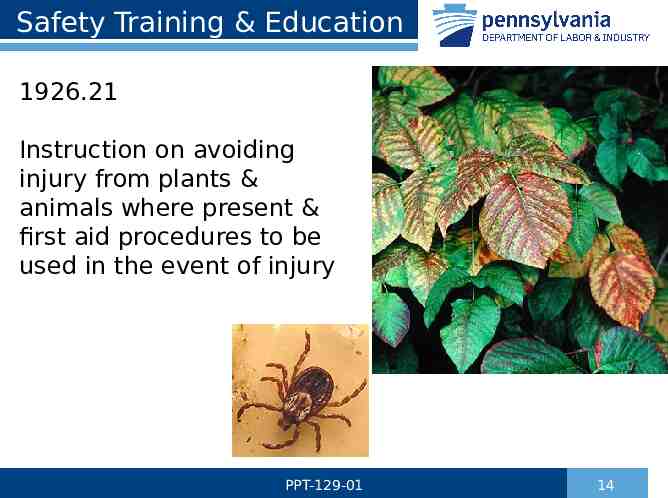
Safety Training & Education 1926.21 Instruction on avoiding injury from plants & animals where present & first aid procedures to be used in the event of injury PPT-129-01 14
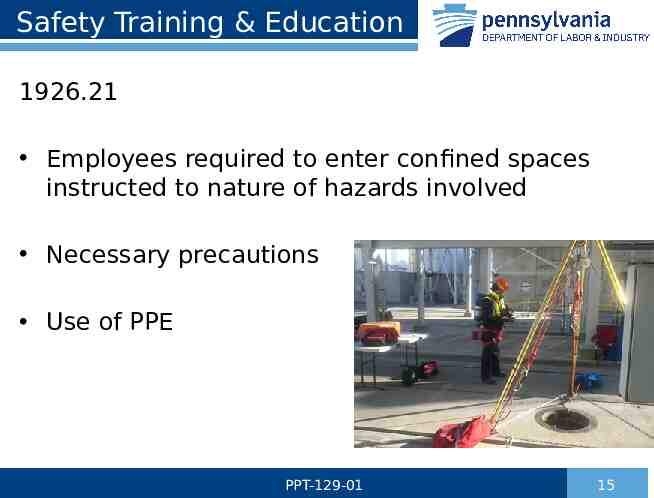
Safety Training & Education 1926.21 Employees required to enter confined spaces instructed to nature of hazards involved Necessary precautions Use of PPE PPT-129-01 15
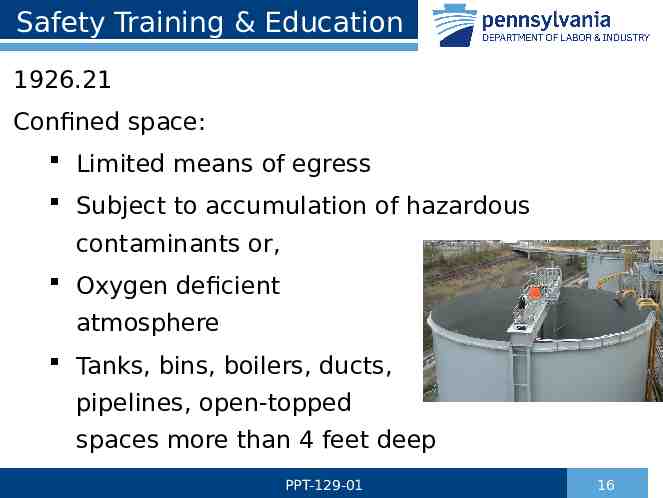
Safety Training & Education 1926.21 Confined space: Limited means of egress Subject to accumulation of hazardous contaminants or, Oxygen deficient atmosphere Tanks, bins, boilers, ducts, pipelines, open-topped spaces more than 4 feet deep PPT-129-01 16
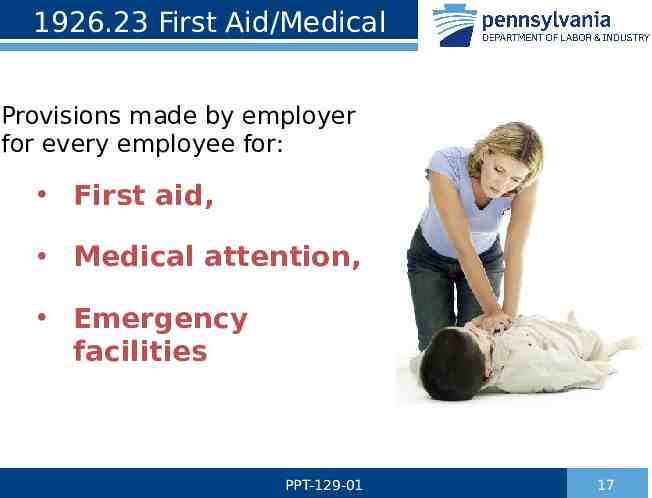
1926.23 First Aid/Medical Provisions made by employer for every employee for: First aid, Medical attention, Emergency facilities PPT-129-01 17
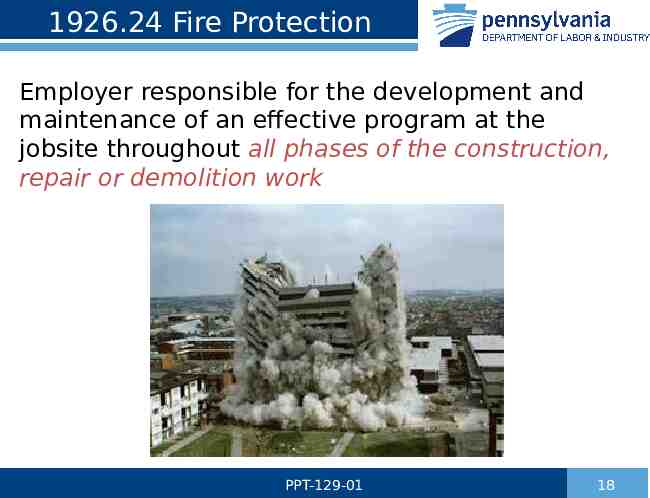
1926.24 Fire Protection Employer responsible for the development and maintenance of an effective program at the jobsite throughout all phases of the construction, repair or demolition work PPT-129-01 18
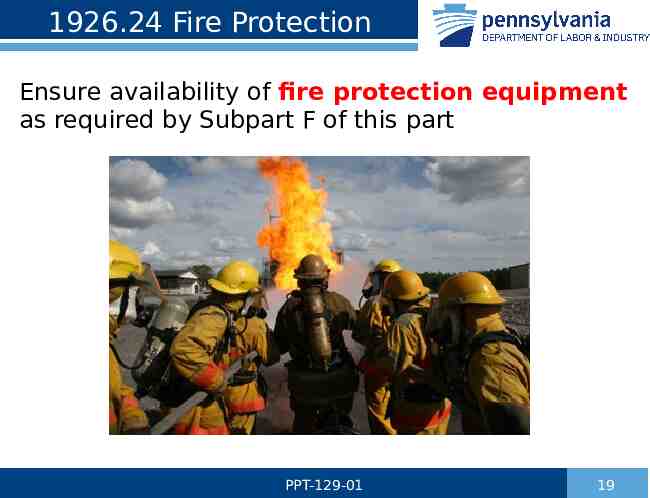
1926.24 Fire Protection Ensure availability of fire protection equipment as required by Subpart F of this part PPT-129-01 19
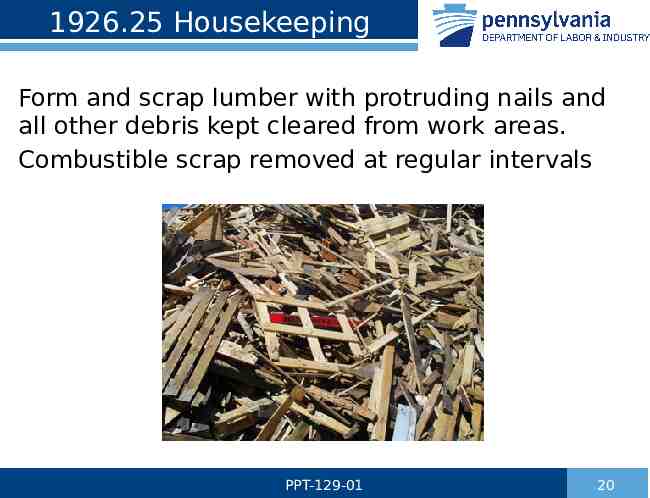
1926.25 Housekeeping Form and scrap lumber with protruding nails and all other debris kept cleared from work areas. Combustible scrap removed at regular intervals PPT-129-01 20
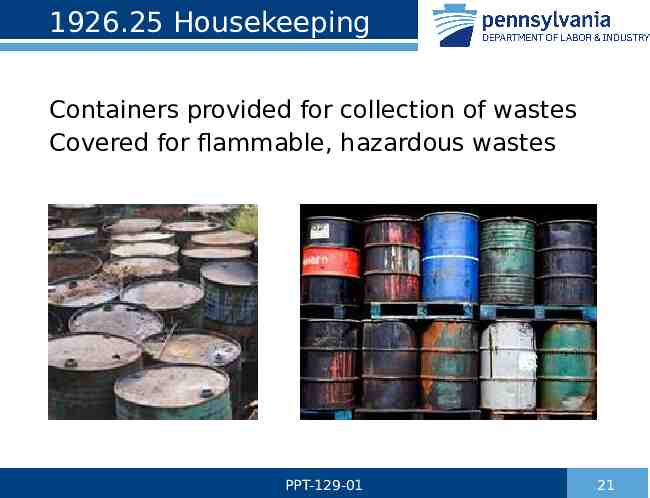
1926.25 Housekeeping Containers provided for collection of wastes Covered for flammable, hazardous wastes PPT-129-01 21
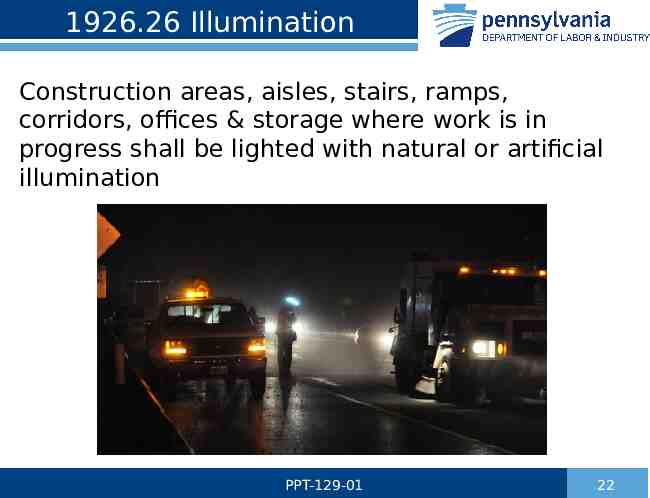
1926.26 Illumination Construction areas, aisles, stairs, ramps, corridors, offices & storage where work is in progress shall be lighted with natural or artificial illumination PPT-129-01 22
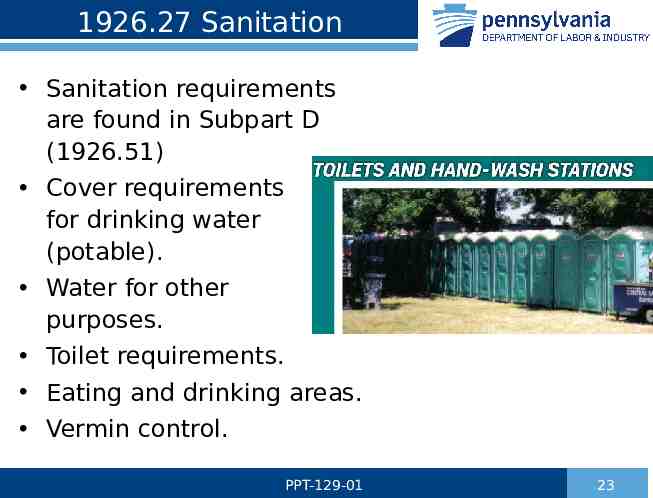
1926.27 Sanitation Sanitation requirements are found in Subpart D (1926.51) Cover requirements for drinking water (potable). Water for other purposes. Toilet requirements. Eating and drinking areas. Vermin control. PPT-129-01 23
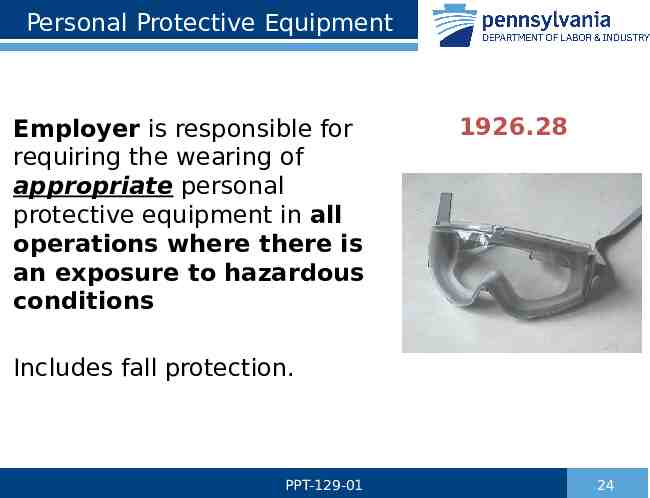
Personal Protective Equipment Employer is responsible for requiring the wearing of appropriate personal protective equipment in all operations where there is an exposure to hazardous conditions 1926.28 Includes fall protection. PPT-129-01 24
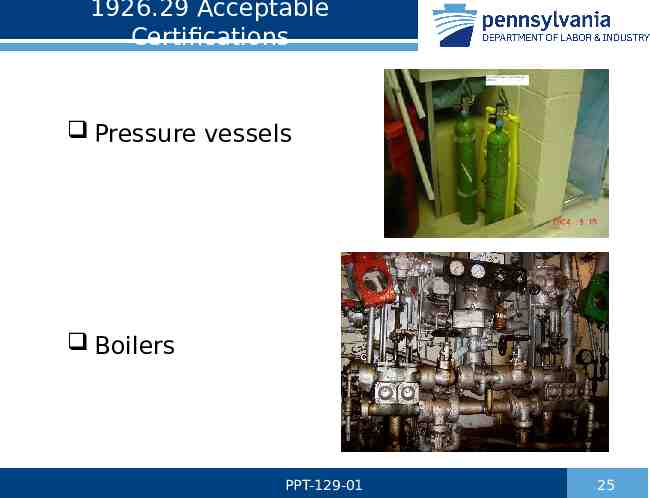
1926.29 Acceptable Certifications Pressure vessels Boilers PPT-129-01 25
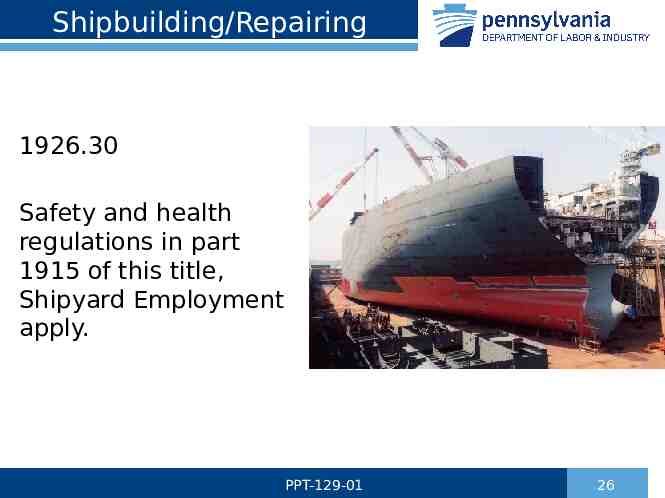
Shipbuilding/Repairing 1926.30 Safety and health regulations in part 1915 of this title, Shipyard Employment apply. PPT-129-01 26
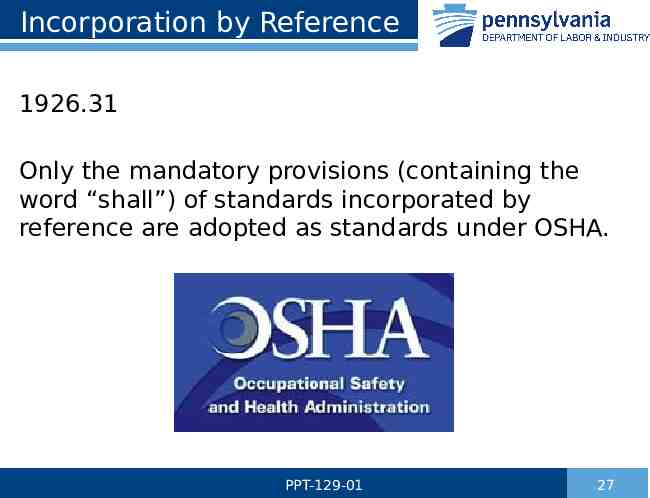
Incorporation by Reference 1926.31 Only the mandatory provisions (containing the word “shall”) of standards incorporated by reference are adopted as standards under OSHA. PPT-129-01 27
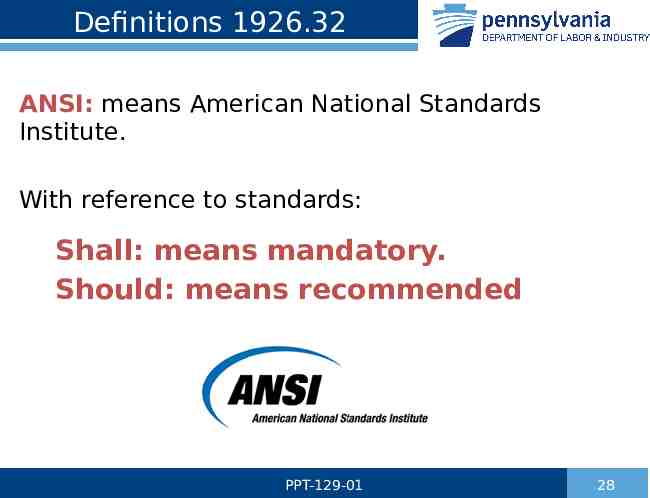
Definitions 1926.32 ANSI: means American National Standards Institute. With reference to standards: Shall: means mandatory. Should: means recommended PPT-129-01 28
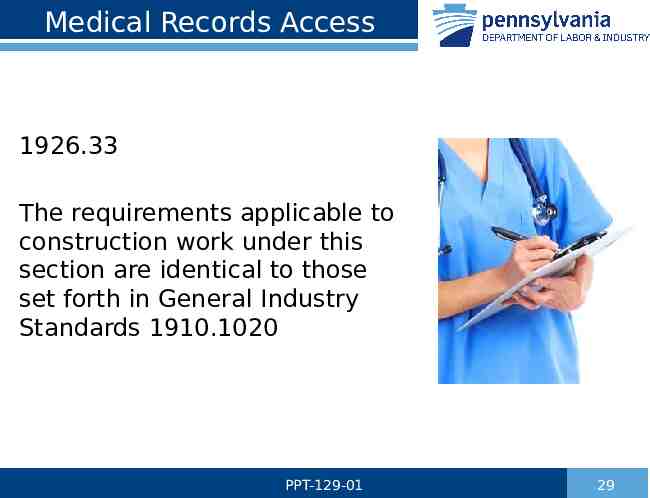
Medical Records Access 1926.33 The requirements applicable to construction work under this section are identical to those set forth in General Industry Standards 1910.1020 PPT-129-01 29
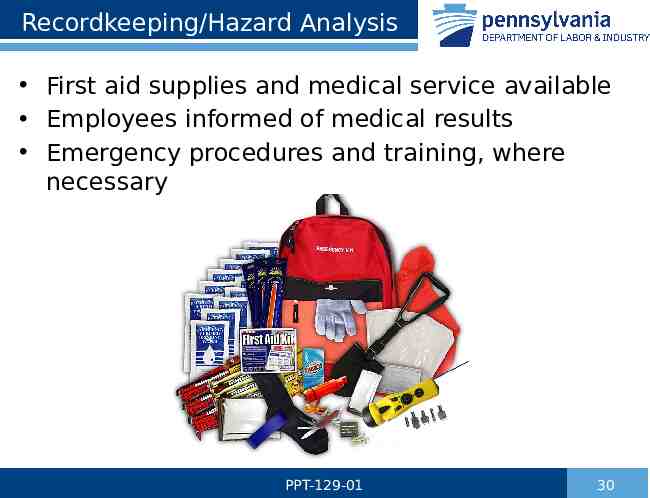
Recordkeeping/Hazard Analysis First aid supplies and medical service available Employees informed of medical results Emergency procedures and training, where necessary PPT-129-01 30
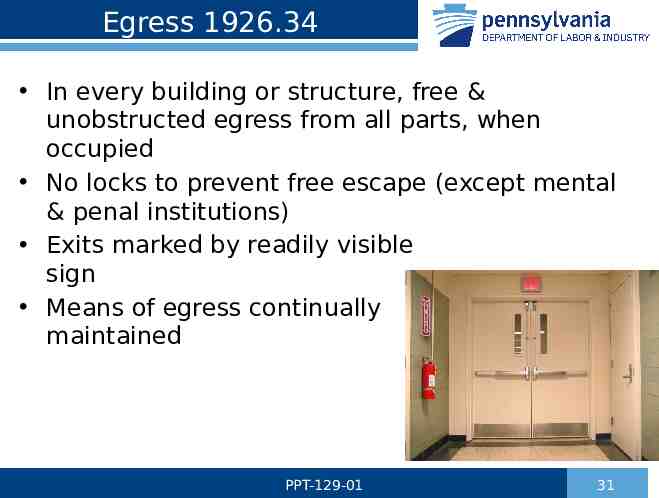
Egress 1926.34 In every building or structure, free & unobstructed egress from all parts, when occupied No locks to prevent free escape (except mental & penal institutions) Exits marked by readily visible sign Means of egress continually maintained PPT-129-01 31
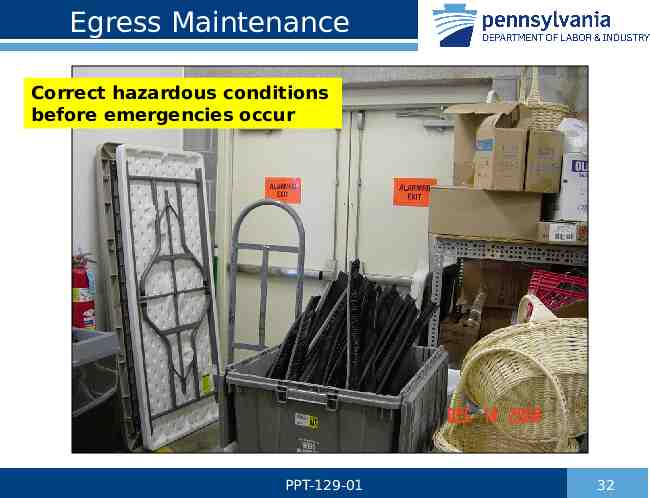
Egress Maintenance Correct hazardous conditions before emergencies occur PPT-129-01 32
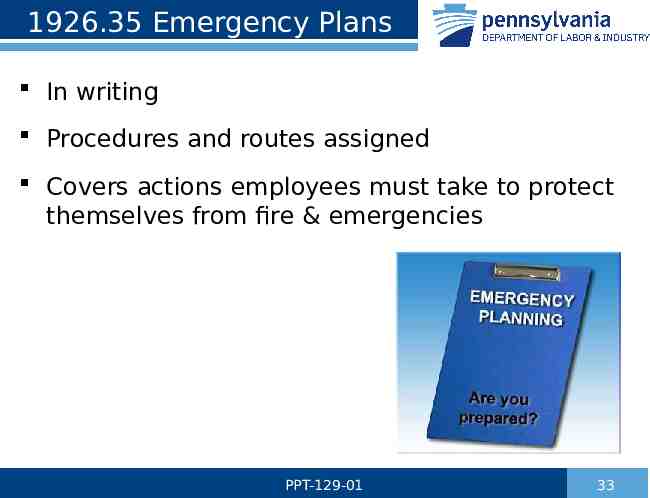
1926.35 Emergency Plans In writing Procedures and routes assigned Covers actions employees must take to protect themselves from fire & emergencies PPT-129-01 33
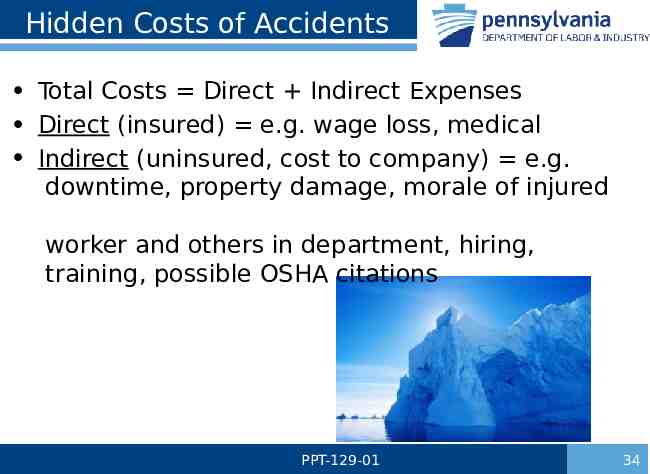
Hidden Costs of Accidents Total Costs Direct Indirect Expenses Direct (insured) e.g. wage loss, medical Indirect (uninsured, cost to company) e.g. downtime, property damage, morale of injured worker and others in department, hiring, training, possible OSHA citations PPT-129-01 34
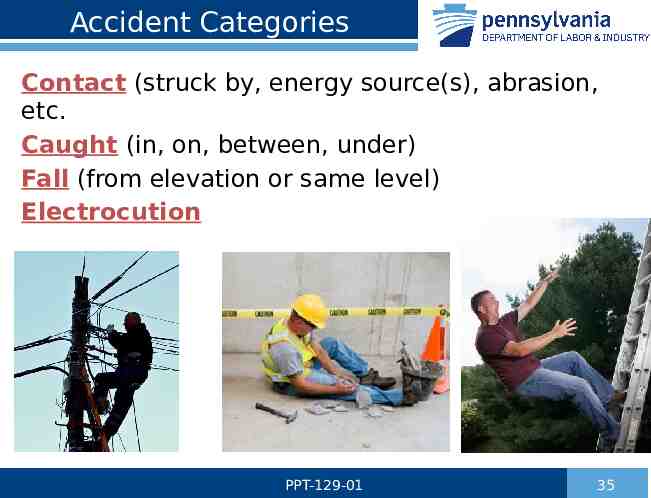
Accident Categories Contact (struck by, energy source(s), abrasion, etc. Caught (in, on, between, under) Fall (from elevation or same level) Electrocution PPT-129-01 35
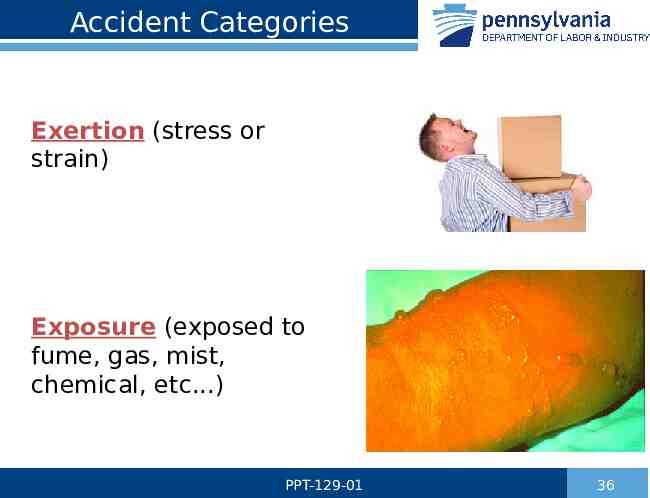
Accident Categories Exertion (stress or strain) Exposure (exposed to fume, gas, mist, chemical, etc.) PPT-129-01 36
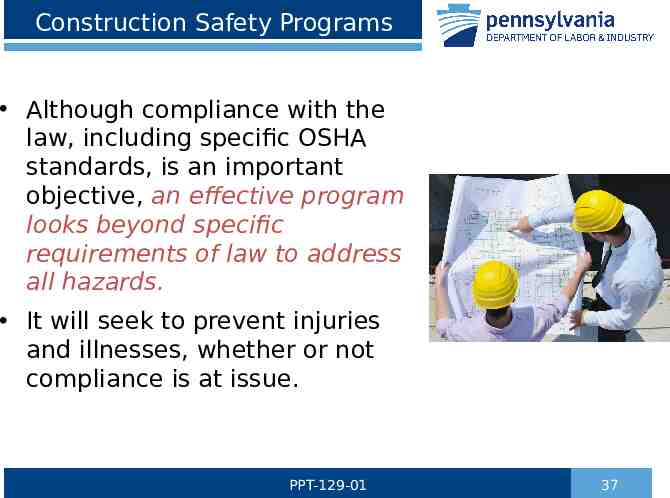
Construction Safety Programs Although compliance with the law, including specific OSHA standards, is an important objective, an effective program looks beyond specific requirements of law to address all hazards. It will seek to prevent injuries and illnesses, whether or not compliance is at issue. PPT-129-01 37
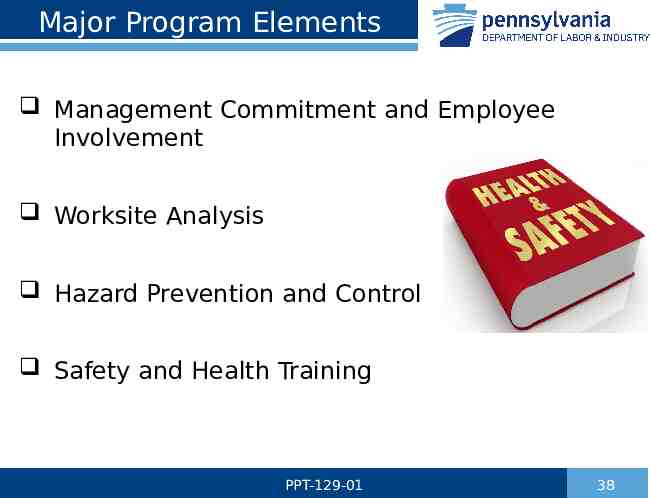
Major Program Elements Management Commitment and Employee Involvement Worksite Analysis Hazard Prevention and Control Safety and Health Training PPT-129-01 38
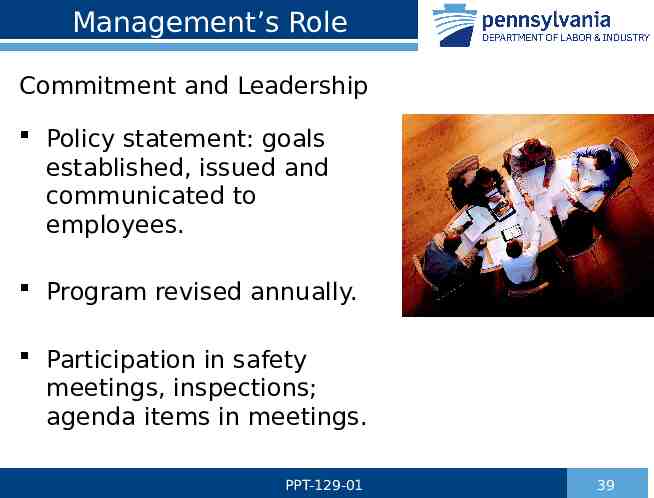
Management’s Role Commitment and Leadership Policy statement: goals established, issued and communicated to employees. Program revised annually. Participation in safety meetings, inspections; agenda items in meetings. PPT-129-01 39
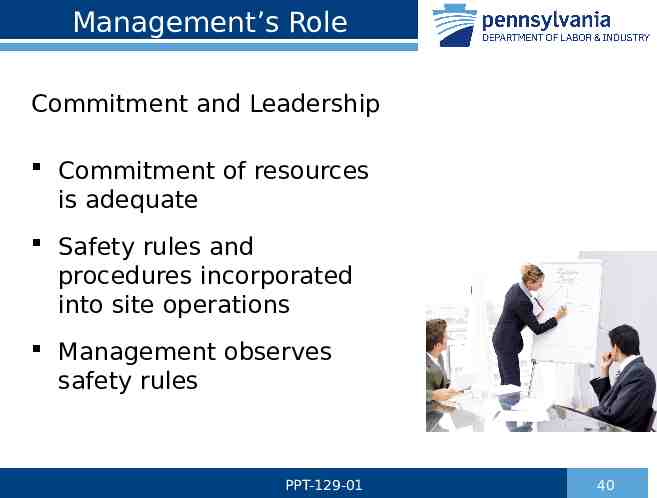
Management’s Role Commitment and Leadership Commitment of resources is adequate Safety rules and procedures incorporated into site operations Management observes safety rules PPT-129-01 40
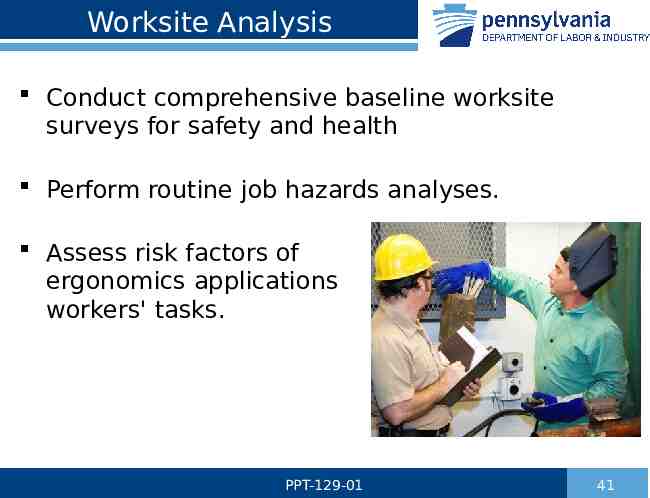
Worksite Analysis Conduct comprehensive baseline worksite surveys for safety and health Perform routine job hazards analyses. Assess risk factors of ergonomics applications workers' tasks. PPT-129-01 to 41
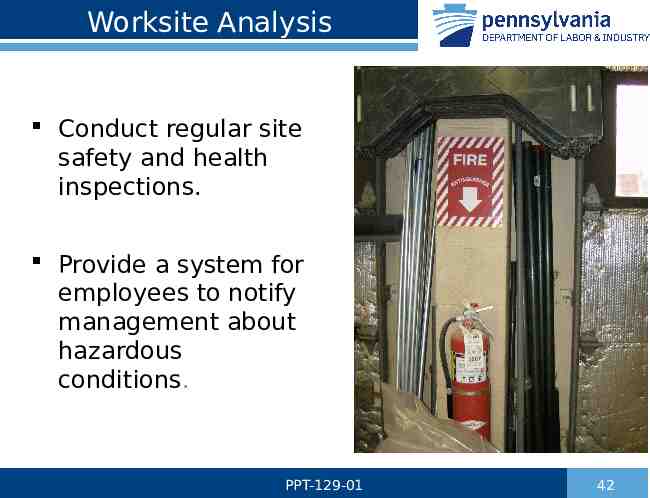
Worksite Analysis Conduct regular site safety and health inspections. Provide a system for employees to notify management about hazardous conditions. PPT-129-01 42
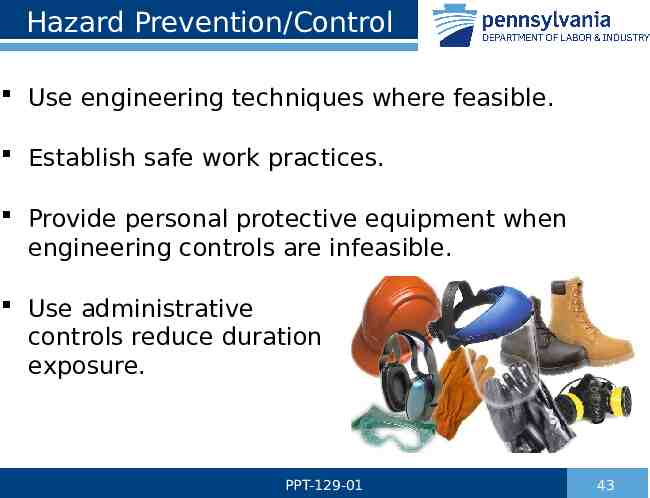
Hazard Prevention/Control Use engineering techniques where feasible. Establish safe work practices. Provide personal protective equipment when engineering controls are infeasible. Use administrative controls reduce duration exposure. PPT-129-01 of 43

Hazard Prevention/Control o Maintain the facility and equipment to prevent breakdowns. o Plan and prepare for emergencies, and conduct training and emergency drills. o Establish a medical program that includes first aid onsite. PPT-129-01 44
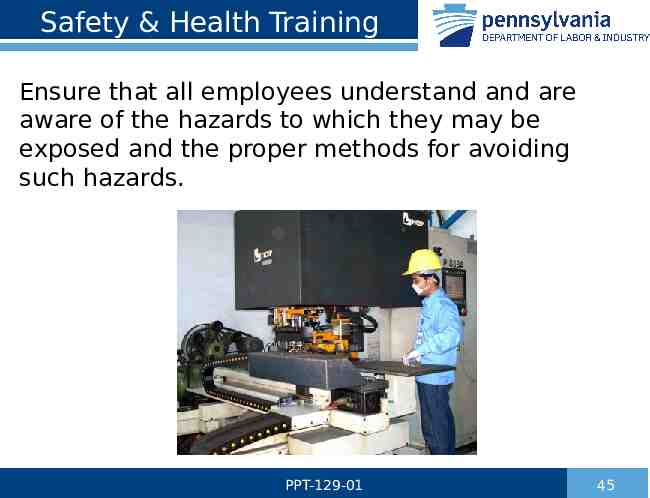
Safety & Health Training Ensure that all employees understand and are aware of the hazards to which they may be exposed and the proper methods for avoiding such hazards. PPT-129-01 45
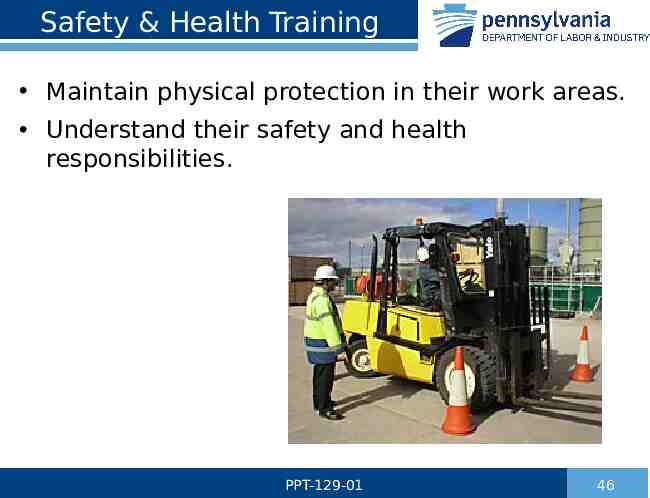
Safety & Health Training Maintain physical protection in their work areas. Understand their safety and health responsibilities. PPT-129-01 46
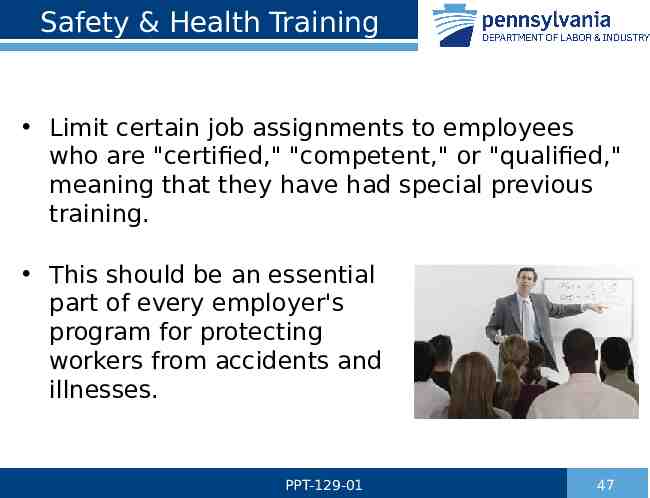
Safety & Health Training Limit certain job assignments to employees who are "certified," "competent," or "qualified," meaning that they have had special previous training. This should be an essential part of every employer's program for protecting workers from accidents and illnesses. PPT-129-01 47
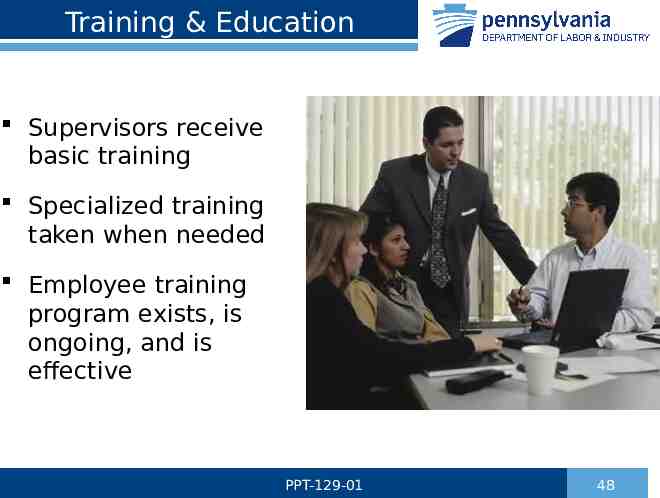
Training & Education Supervisors receive basic training Specialized training taken when needed Employee training program exists, is ongoing, and is effective PPT-129-01 48
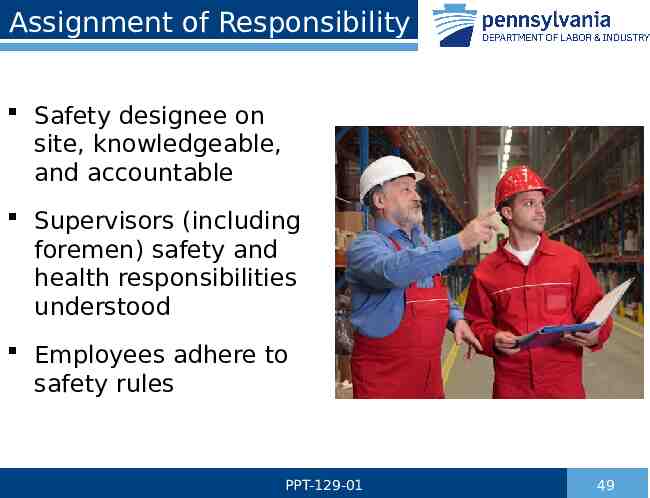
Assignment of Responsibility Safety designee on site, knowledgeable, and accountable Supervisors (including foremen) safety and health responsibilities understood Employees adhere to safety rules PPT-129-01 49
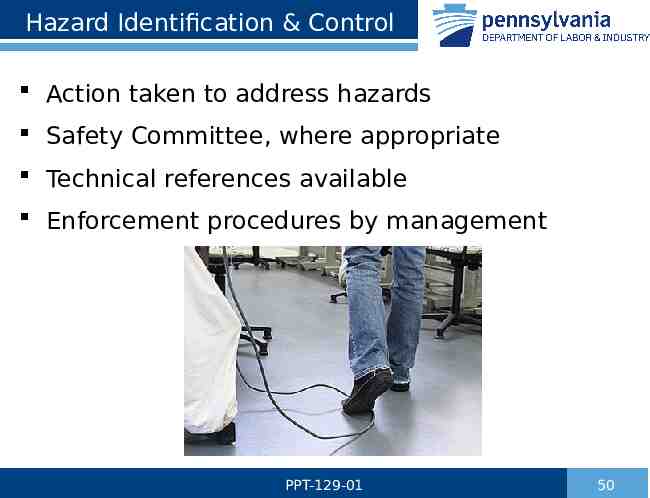
Hazard Identification & Control Action taken to address hazards Safety Committee, where appropriate Technical references available Enforcement procedures by management PPT-129-01 50
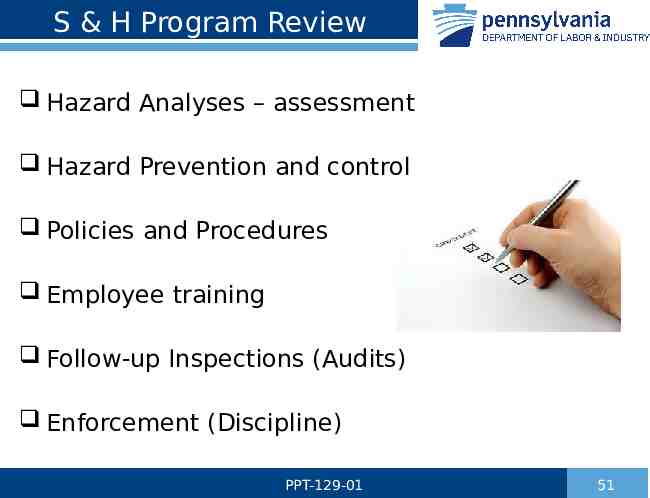
S & H Program Review Hazard Analyses – assessment Hazard Prevention and control Policies and Procedures Employee training Follow-up Inspections (Audits) Enforcement (Discipline) PPT-129-01 51
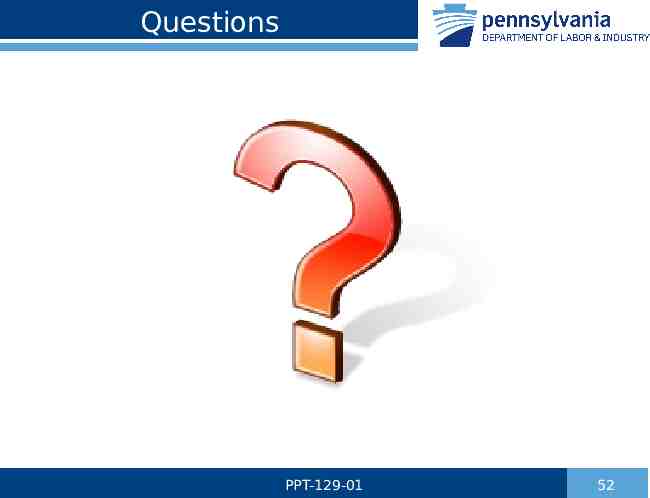
Questions PPT-129-01 52
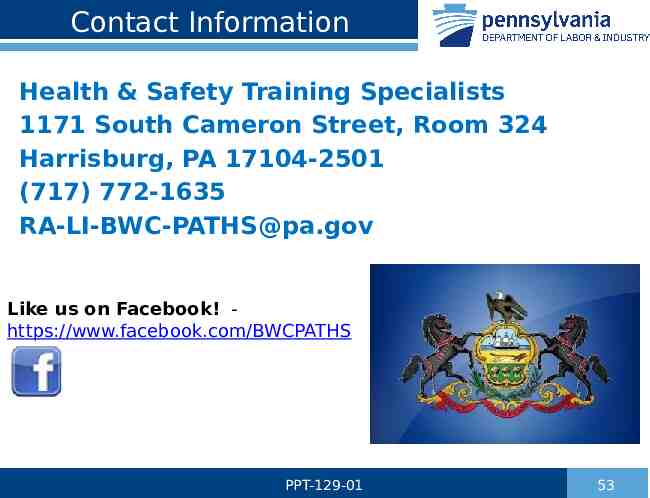
Contact Information Health & Safety Training Specialists 1171 South Cameron Street, Room 324 Harrisburg, PA 17104-2501 (717) 772-1635 [email protected] Like us on Facebook! https://www.facebook.com/BWCPATHS PPT-129-01 53
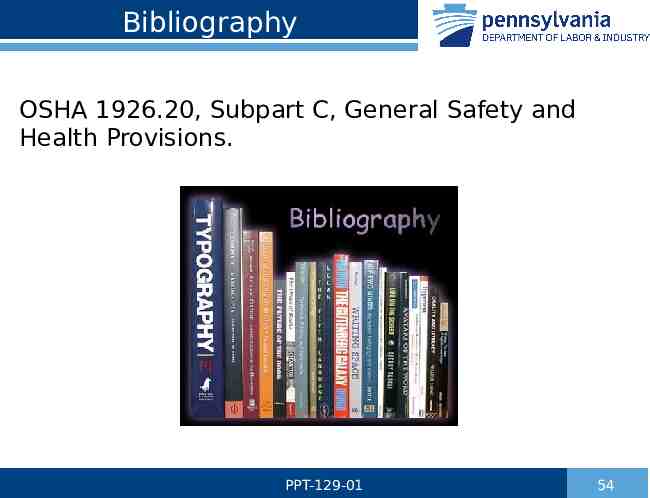
Bibliography OSHA 1926.20, Subpart C, General Safety and Health Provisions. PPT-129-01 54