OSHA’s Respirable Crystalline Silica Dust Standard & The Pest Control
44 Slides3.55 MB
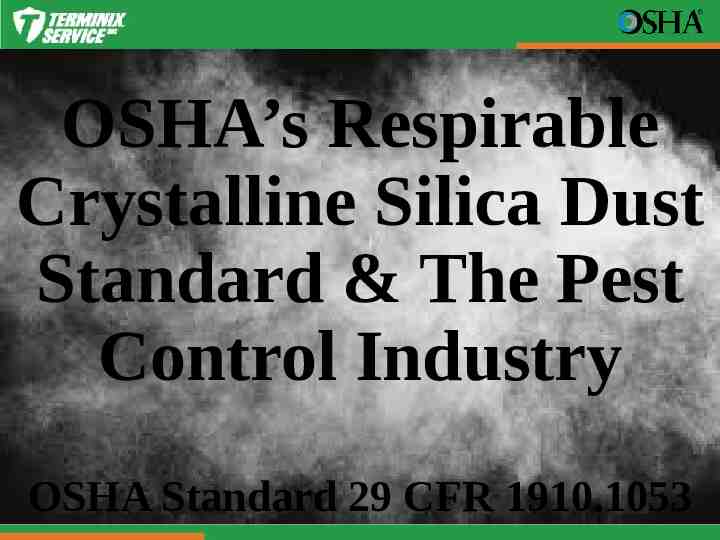
OSHA’s Respirable Crystalline Silica Dust Standard & The Pest Control Industry OSHA Standard 29 CFR 1910.1053

What is Silica? It is a chemical compound: an oxide of silicon; SiO2 It is commonly found in nature as quartz, but makes up sand and glass (major component of rocks and mountains). One of the most complex and most abundant families of materials. Also produced synthetically.
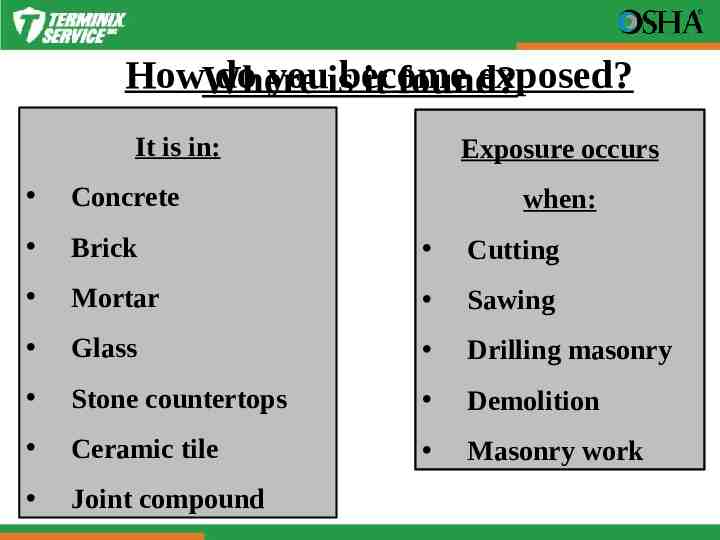
HowWhere do youisbecome exposed? it found? It is in: Exposure occurs Concrete Brick Cutting Mortar Sawing Glass Drilling masonry Stone countertops Demolition Ceramic tile Masonry work Joint compound when:
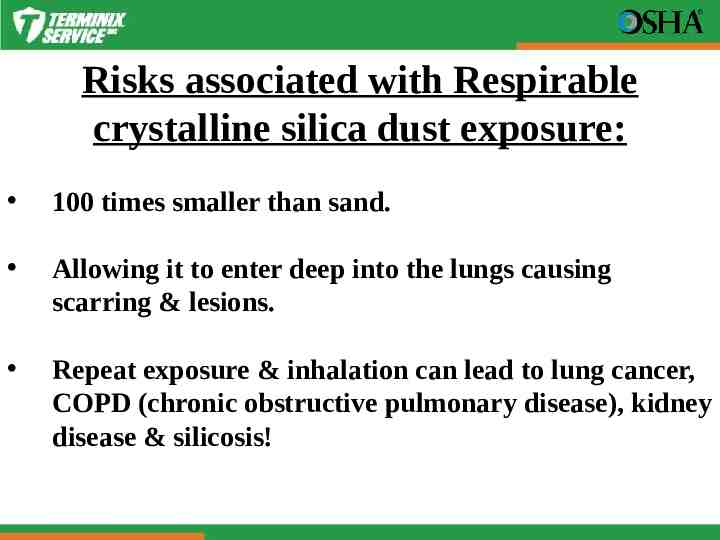
Risks associated with Respirable crystalline silica dust exposure: 100 times smaller than sand. Allowing it to enter deep into the lungs causing scarring & lesions. Repeat exposure & inhalation can lead to lung cancer, COPD (chronic obstructive pulmonary disease), kidney disease & silicosis!
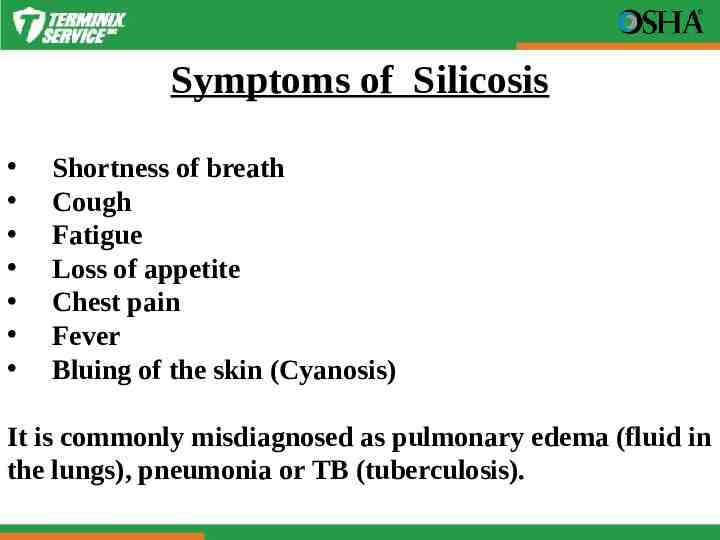
Symptoms of Silicosis Shortness of breath Cough Fatigue Loss of appetite Chest pain Fever Bluing of the skin (Cyanosis) It is commonly misdiagnosed as pulmonary edema (fluid in the lungs), pneumonia or TB (tuberculosis).
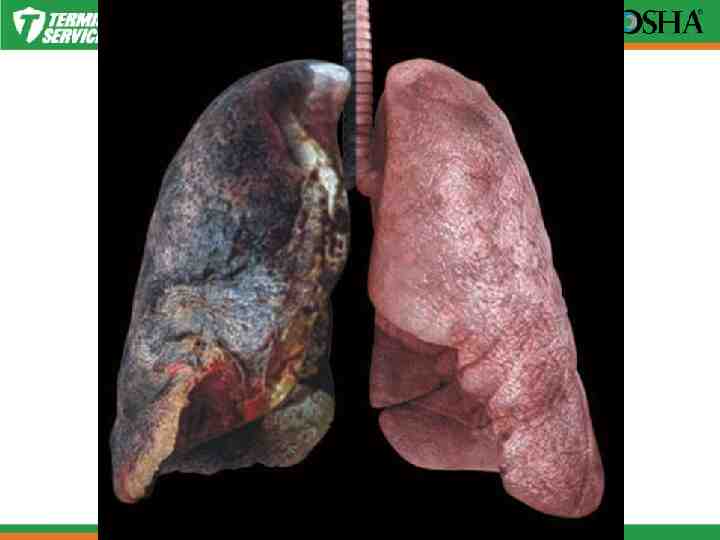
The risks of Silicosis Currently, there is no treatment or therapy for Silicosis! The damage is irreversible! People with silicosis have a much higher risk of contracting tuberculosis!
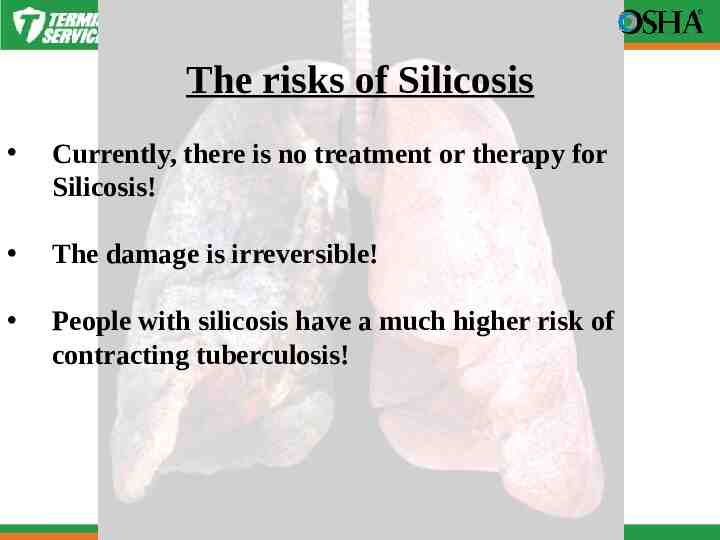
A Few Questions To Ask Yourself Does your company perform services that require you to be in compliance with the standard? (Liquid termite treatment, masonry work, tile work ) If so, is it part of your company’s OSHA Hazard Communication, Hazard Assessment & Respiratory Protection Plans? If so, do you have adequate written training programs & procedures in place with documentation to be in compliance?
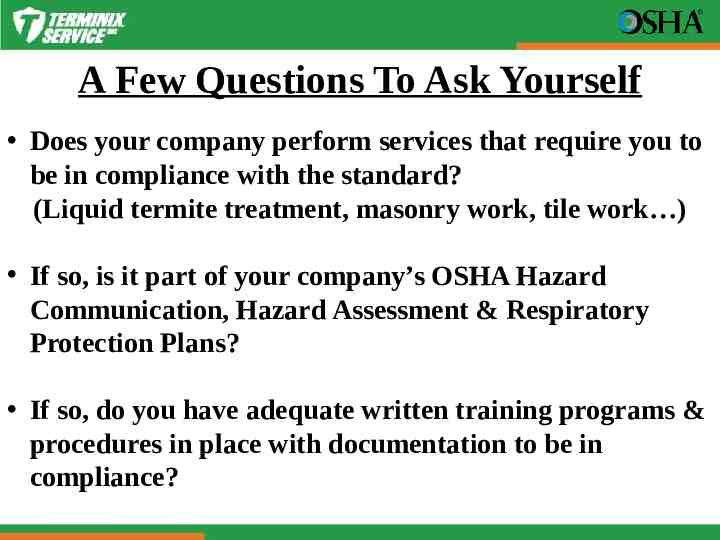
A Few Questions To Ask Yourself How many of you perform some type of liquid termiticide treatment where drilling masonry and sweeping of masonry dust is involved (Liquid spot, EP/LI & comprehensive termite treatments)?
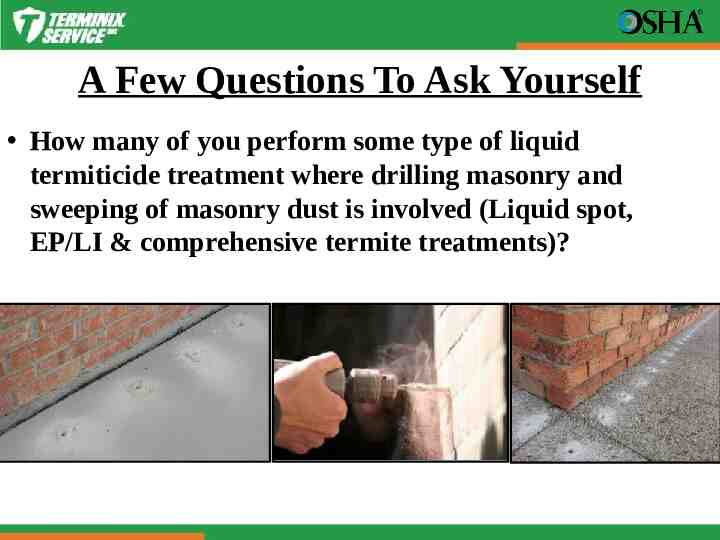
Does the standard apply to you? The NEW construction standard began being enforced on September 23rd, 2017. These are the OSHA Respirable Crystalline Silica in Construction (29 CFR 1910.1053) standards for PELs: 8-hour time weighted average (TWA) permissible exposure limit (PEL) of 50 µg/m3 Action level (AL) of 25 µg/m3. WHAT DOES THIS MEAN?
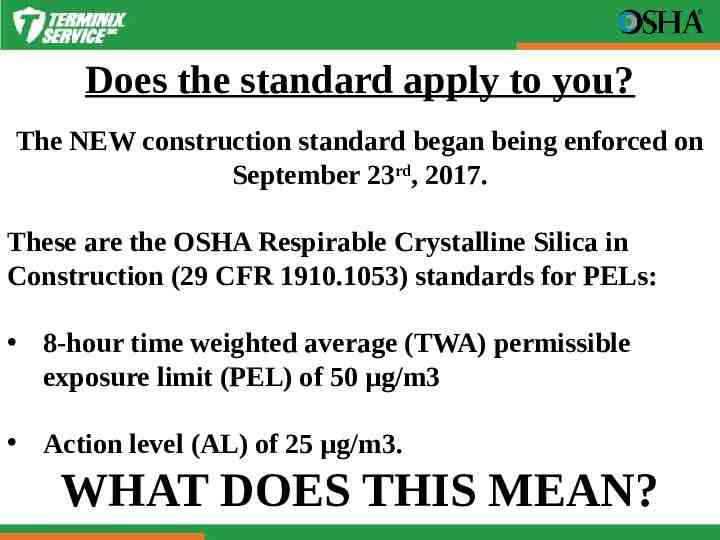
1926.1153(c)(1) For each employee engaged in a task identified in Table 1 of the standard, the employer shall fully and properly implement the engineering controls, work practices, and respiratory protection specified for the task in Table 1; UNLESS the employer assesses and limits the exposure of the employee to respirable crystalline silica in accordance with paragraph (d) of this section.
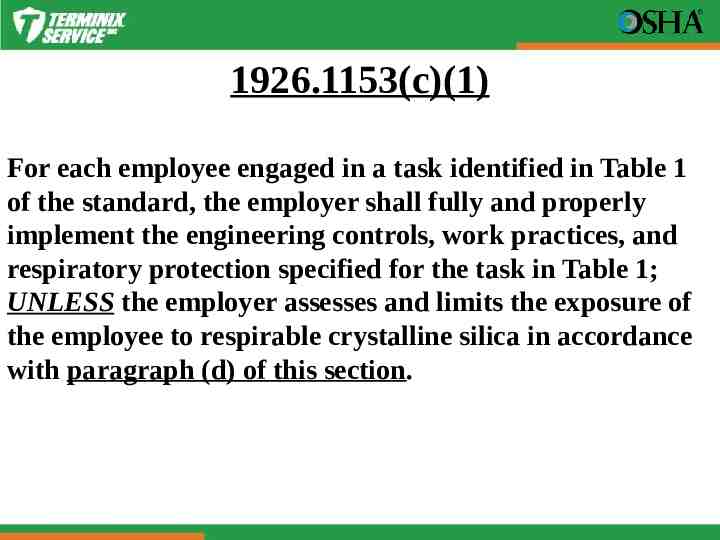
The OSHA “Small Entity Compliance Guide” is a great tool to analyze what you need to do for your company. “Where employees perform tasks that involve exposure to respirable crystalline silica for a very short period of time, exposures for many tasks will be below 25 μg/m3 as an 8-hour TWA.“ “For example, if a termite tech using hand-held rotary hammer drill has a duration of exposure 15 minutes or less, the 8-hour TWA exposure can reasonably be anticipated to remain under the 25 μg/m3 threshold (assuming there is no more exposure for the remainder of the shift), then the standard would not apply.”
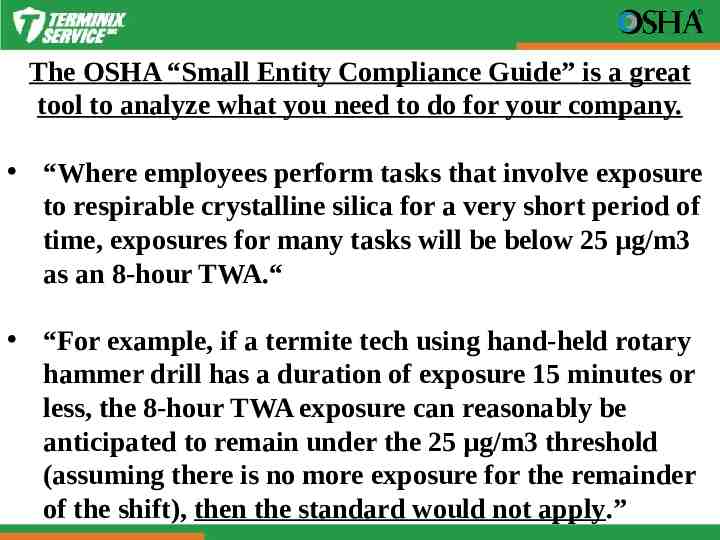
Is t he r of w e a or k n y r r o r e h ind perf esear t e h d e w ust t orm chHA a d n d ry? S a a e O m d t o a e t Iosvet in etd th for r h e he p c t e x e h r S e w ? p e e s t e e o a e c t a e d s n n y y n a t o p w d l w o c “ p e a o o l H I l r m n n e a d r d t L ” rol u u E ? o P s t tr y no So
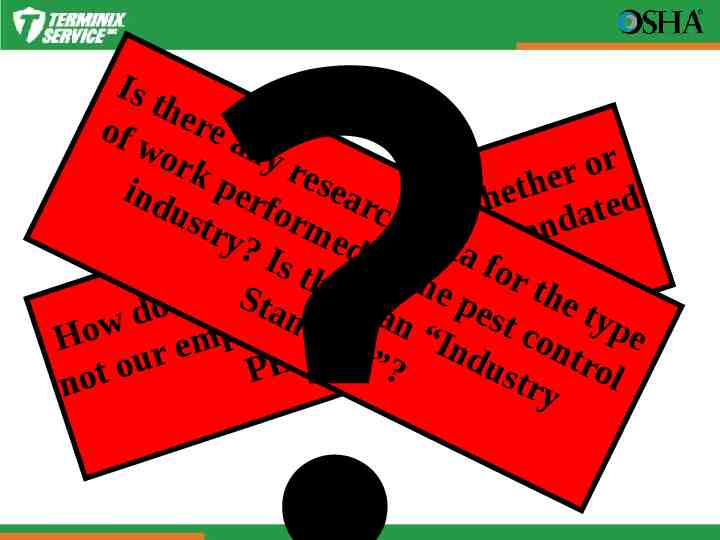
You have 2 options: 1. Comply with 1926.1153(c)(1) “Table 1” & implement the engineering and work practice control methods. Or 2. Assess and limit the exposure of the employee to respirable crystalline silica in accordance with paragraph 1926.1153(d). Section (vii) of “Table 1” lists the required engineering and work practice control methods for drilling. Let’s take a look!
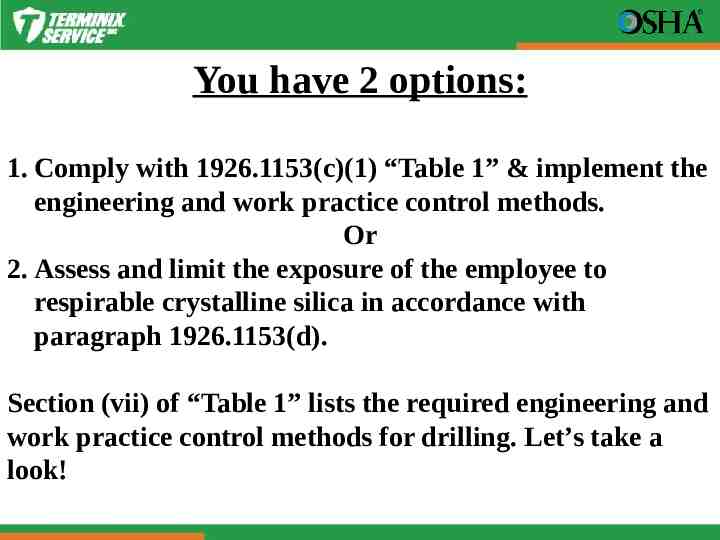
The standard does contain a flexible option for employers whose employees are engaged in the construction tasks listed in Table 1 at 29 CFR 1926.1153(c)(1). Table 1—Specified Exposure Control Methods When Working With Materials Containing Crystalline Silica Equipment/task Engineering & Work Practice Control Methods (vii) Handheld and stand-mounted drills (including impact and rotary hammer drills) 1-Use drill equipped with commercially available shroud or cowling with dust collection system. 2-Operate and maintain tool in accordance with manufacturer's instructions to minimize dust emissions. 3-Dust collector must provide the air flow recommended by the tool manufacturer, or greater, and have a filter with 99% or greater efficiency and a filter-cleaning mechanism. 4-Use a HEPA-filtered vacuum when cleaning holes. Required respiratory protection and minimum assigned protection factor (APF) 4 hours/shift None 4 hours/shift None
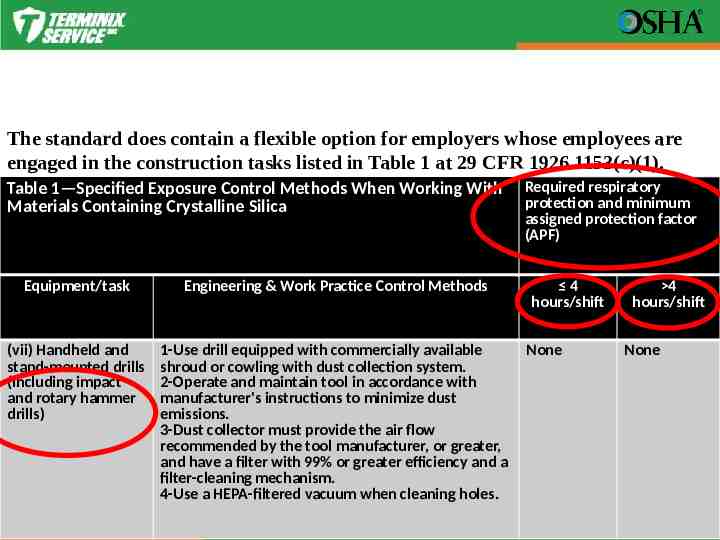
Option 1 – Comply with the standards in “Table 1” The standard does contain a flexible option for employers whose employees are engaged in the construction tasks listed in Table 1 at 29 CFR 1926.1153(c)(1). Table 1—Specified Exposure Control Methods When Working With Materials Containing Crystalline Silica Equipment/task Engineering & Work Practice Control Methods (vii) Handheld and stand-mounted drills (including impact and rotary hammer drills) 1-Use drill equipped with commercially available shroud or cowling with dust collection system. 2-Operate and maintain tool in accordance with manufacturer's instructions to minimize dust emissions. 3-Dust collector must provide the air flow recommended by the tool manufacturer, or greater, and have a filter with 99% or greater efficiency and a filter-cleaning mechanism. 4-Use a HEPA-filtered vacuum when cleaning holes. Required respiratory protection and minimum assigned protection factor (APF) 4 hours/shift None 4 hours/shift None
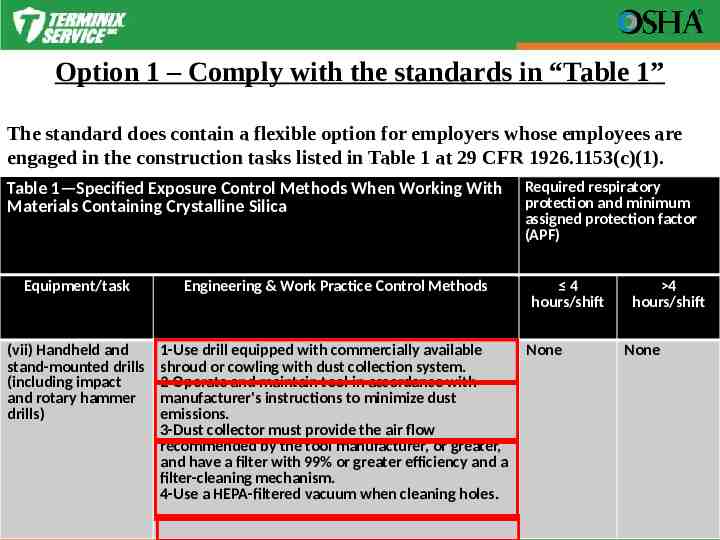
Option 1 – Comply with the standards in “Table 1” The standard does contain a flexible option for employers whose employees are engaged in the construction tasks listed in Table 1 at 29 CFR 1926.1153(c)(1). Table 1—Specified Exposure Control Methods When Working With Materials Containing Crystalline Silica Equipment/task Engineering & Work Practice Control Methods (vii) Handheld and stand-mounted drills (including impact and rotary hammer drills) 1-Use drill equipped with commercially available shroud or cowling with dust collection system. 2-Operate and maintain tool in accordance with manufacturer's instructions to minimize dust emissions. 3-Dust collector must provide the air flow recommended by the tool manufacturer, or greater, and have a filter with 99% or greater efficiency and a filter-cleaning mechanism. 4-Use a HEPA-filtered vacuum when cleaning holes. Required respiratory protection and minimum assigned protection factor (APF) 4 hours/shift None 4 hours/shift None
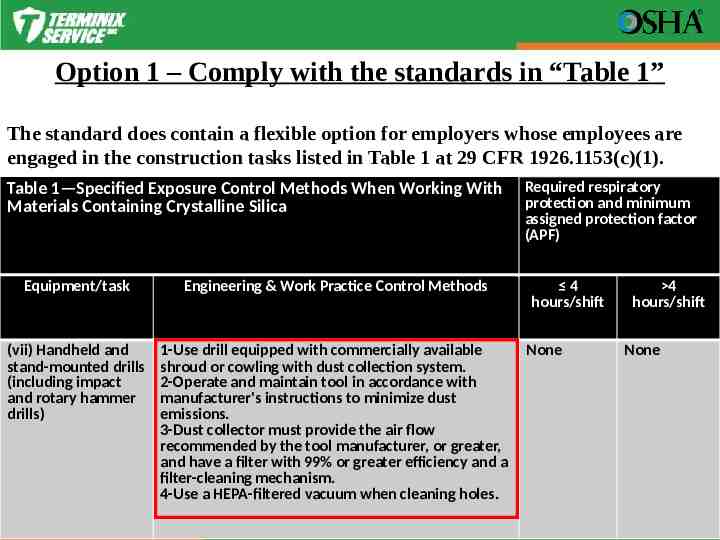
1,2 & 3-Use drill equipped with commercially available shroud or cowling with dust collection system. MSRP 189.95 MSRP 212.00
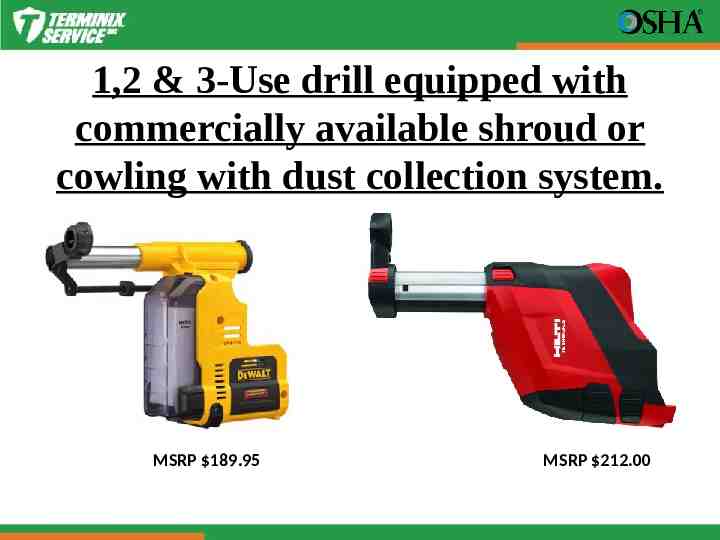
1,2 & 3-Use drill equipped with commercially available shroud or cowling with dust collection system. Note: You still need the HEPA VAC and hose MSRP from 51.50 MSRP from 185.50
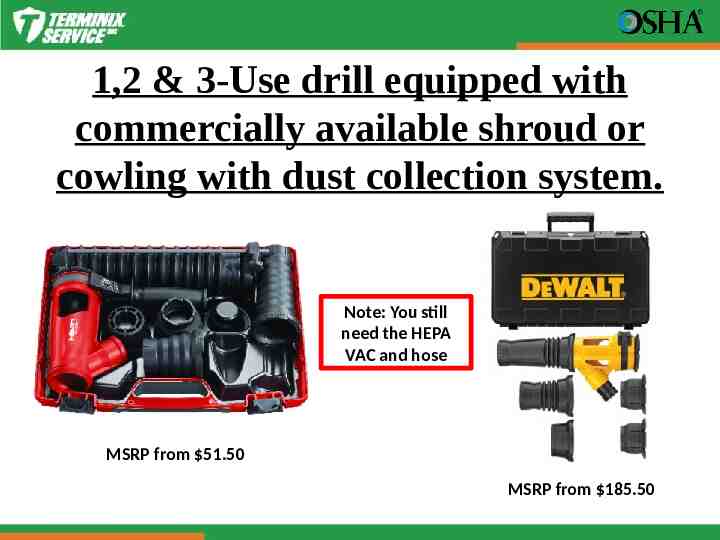
The Standard The standard does contain a flexible option for employers whose employees are engaged in the construction tasks listed in Table 1 at 29 CFR 1926.1153(c)(1). Table 1—Specified Exposure Control Methods When Working With Materials Containing Crystalline Silica Equipment/task Engineering & Work Practice Control Methods (vii) Handheld and stand-mounted drills (including impact and rotary hammer drills) 1-Use drill equipped with commercially available shroud or cowling with dust collection system. 2-Operate and maintain tool in accordance with manufacturer's instructions to minimize dust emissions. 3-Dust collector must provide the air flow recommended by the tool manufacturer, or greater, and have a filter with 99% or greater efficiency and a filter-cleaning mechanism. 4-Use a HEPA-filtered vacuum when cleaning holes. Required respiratory protection and minimum assigned protection factor (APF) 4 hours/shift None 4 hours/shift None
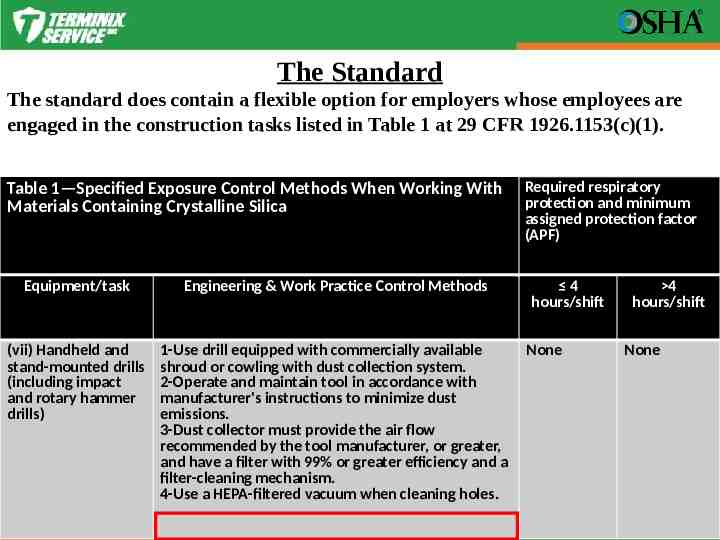
4-Use a HEPA-filtered vacuum when cleaning holes. MSRP from 1,649.00 MSRP from 510.00
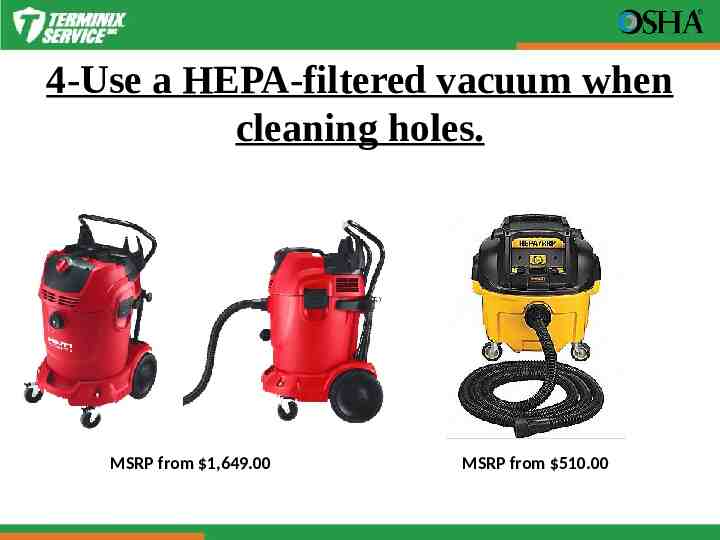
Prices vary but it could cost between 750 to 2,050 to put together 1 set of equipment to comply with the new standard! Depending on the size of your company, it can be a large expense!
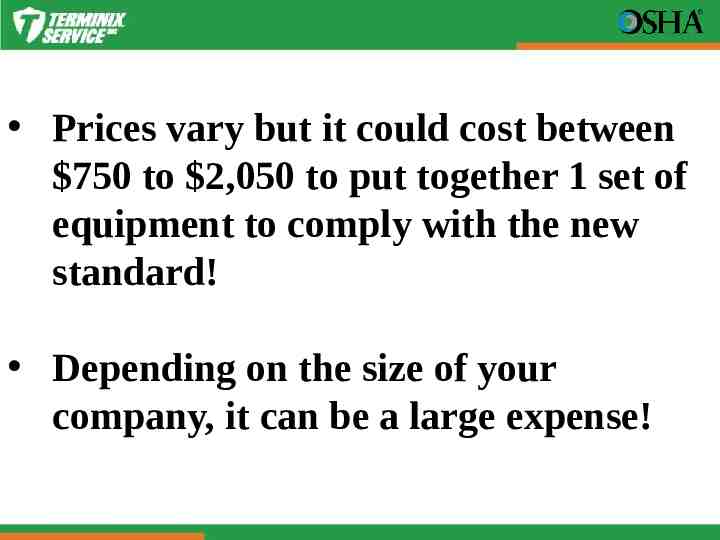
Option 2 : Assessing and limiting the exposure of the employee to respirable crystalline silica in accordance with paragraph 1926.1153(d). 1926.1153(d) - Alternative exposure control methods. For tasks not listed in Table 1, or where the employer does not fully and properly implement the engineering controls, work practices, and respiratory protection described in Table 1: 1926.1153(d)(1) - Permissible exposure limit (PEL). The employer shall ensure that no employee is exposed to an airborne concentration of respirable crystalline silica in excess of 50 μg/m3, calculated as an 8-hour TWA. 1926.1153(d)(2) - Exposure assessment1926.1153(d)(2)(i) - General. The employer shall assess the exposure of each employee who is or may reasonably be expected to be exposed to respirable crystalline silica at or above the action level in accordance with either the performance option in paragraph (d)(2)(ii) or the scheduled monitoring option in paragraph (d)(2)(iii) of this section.
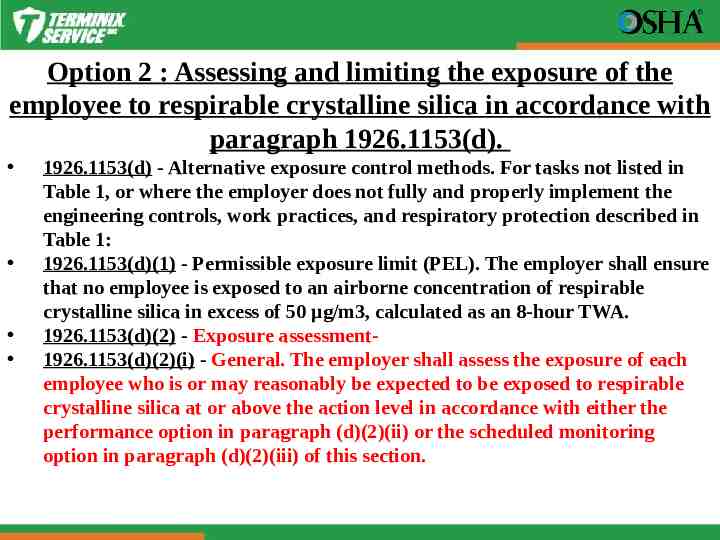
Option 2 : Assessing and limiting the exposure of the employee to respirable crystalline silica in accordance with paragraph 1926.1153(d). 1926.1153(d)(2)(ii) - Performance option. The employer shall assess the 8-hour TWA exposure for each employee on the basis of any combination of air monitoring data or objective data sufficient to accurately characterize employee exposures to respirable crystalline silica. 1926.1153(d)(2)(iii) - Scheduled monitoring option. 1926.1153(d)(2)(iii)(A) - The employer shall perform initial monitoring to assess the 8-hour TWA exposure for each employee on the basis of one or more personal breathing zone air samples that reflect the exposures of employees on each shift, for each job classification, in each work area. Where several employees perform the same tasks on the same shift and in the same work area, the employer may sample a representative fraction of these employees in order to meet this requirement. In representative sampling, the employer shall sample the employee(s) who are expected to have the highest exposure to respirable crystalline silica.
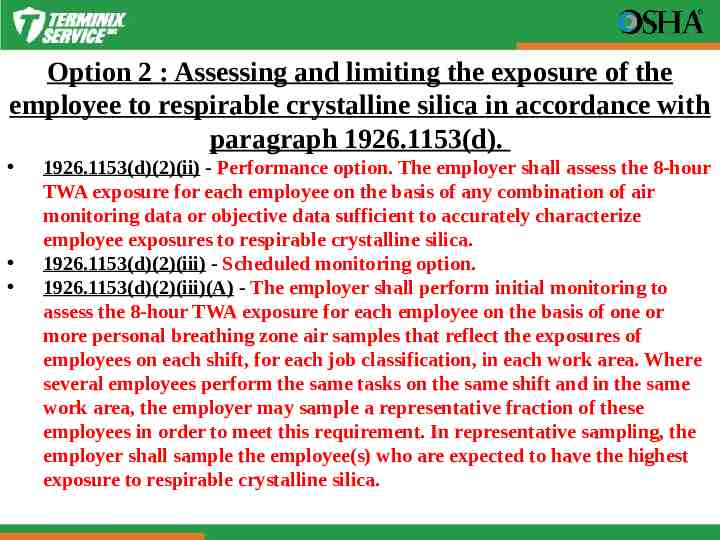
Option 2 : Assessing and limiting the exposure of the employee to respirable crystalline silica in accordance with paragraph 1926.1153(d). 1926.1153(d)(2)(iii)(B) - If initial monitoring indicates that employee exposures are below the action level, the employer may discontinue monitoring for those employees whose exposures are represented by such monitoring. 1926.1153(d)(2)(iii)(C) - Where the most recent exposure monitoring indicates that employee exposures are at or above the action level but at or below the PEL, the employer shall repeat such monitoring within six months of the most recent monitoring. 1926.1153(d)(2)(iii)(D) - Where the most recent exposure monitoring indicates that employee exposures are above the PEL, the employer shall repeat such monitoring within three months of the most recent monitoring.
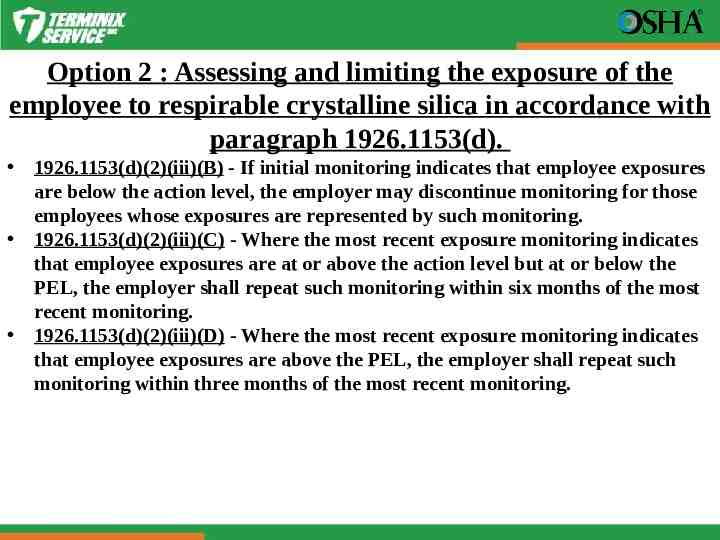
Option 2 : Assessing and limiting the exposure of the employee to respirable crystalline silica in accordance with paragraph 1926.1153(d). 1926.1153(d)(2)(iii)(E) - Where the most recent (non-initial) exposure monitoring indicates that employee exposures are below the action level, the employer shall repeat such monitoring within six months of the most recent monitoring until two consecutive measurements, taken seven or more days apart, are below the action level, at which time the employer may discontinue monitoring for those employees whose exposures are represented by such monitoring, except as otherwise provided in paragraph (d)(2)(iv) of this section. 1926.1153(d)(2)(iv) - Reassessment of exposures. The employer shall reassess exposures whenever a change in the production, process, control equipment, personnel, or work practices may reasonably be expected to result in new or additional exposures at or above the action level, or when the employer has any reason to believe that new or additional exposures at or above the action level have occurred.
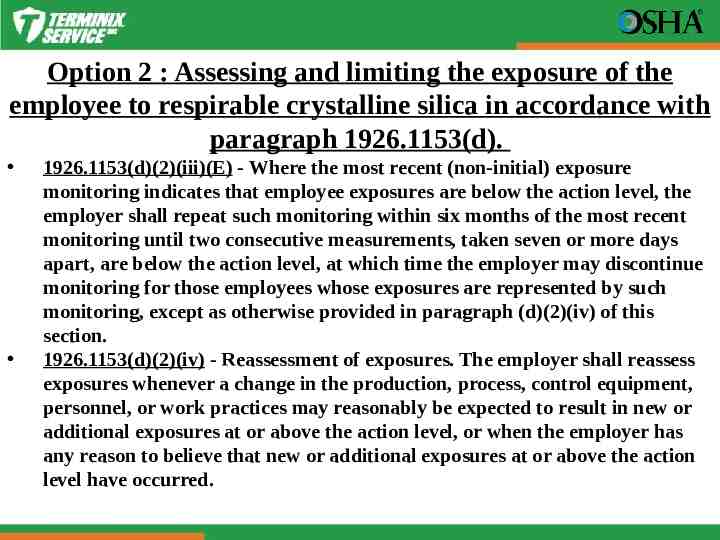
Option 2 : Assessing and limiting the exposure of the employee to respirable crystalline silica in accordance with paragraph 1926.1153(d). 1926.1153(d)(2)(v) - Methods of sample analysis. The employer shall ensure that all samples taken to satisfy the monitoring requirements of paragraph (d) (2) of this section are evaluated by a laboratory that analyzes air samples for respirable crystalline silica in accordance with the procedures in Appendix A to this section. 1926.1153(d)(2)(vi) - Employee notification of assessment results. 1926.1153(d)(2)(vi)(A) - Within five working days after completing an exposure assessment in accordance with paragraph (d)(2) of this section, the employer shall individually notify each affected employee in writing of the results of that assessment or post the results in an appropriate location accessible to all affected employees. 1926.1153(d)(2)(vi)(B) - Whenever an exposure assessment indicates that employee exposure is above the PEL, the employer shall describe in the written notification the corrective action being taken to reduce employee exposure to or below the PEL.
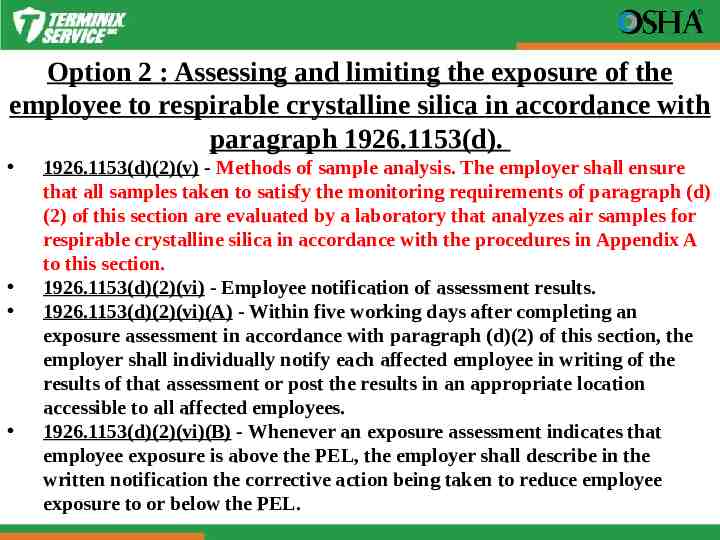
Option 2 : Assessing and limiting the exposure of the employee to respirable crystalline silica in accordance with paragraph 1926.1153(d). 1926.1153(d)(2)(vii) - Observation of monitoring. 1926.1153(d)(2)(vii)(A) - Where air monitoring is performed to comply with the requirements of this section, the employer shall provide affected employees or their designated representatives an opportunity to observe any monitoring of employee exposure to respirable crystalline silica. 1926.1153(d)(2)(vii)(B) - When observation of monitoring requires entry into an area where the use of protective clothing or equipment is required for any workplace hazard, the employer shall provide the observer with protective clothing and equipment at no cost and shall ensure that the observer uses such clothing and equipment. 1926.1153(d)(3) - Methods of compliance-
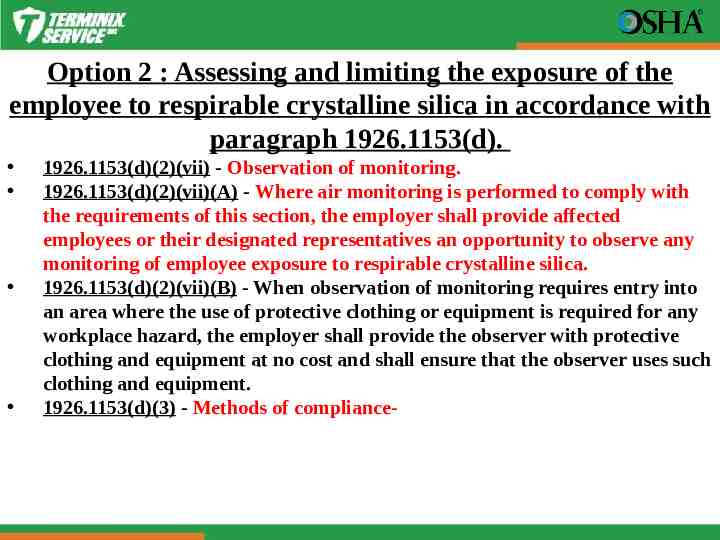
Option 2 : Assessing and limiting the exposure of the employee to respirable crystalline silica in accordance with paragraph 1926.1153(d). 1926.1153(d)(3)(i) - Engineering and work practice controls. The employer shall use engineering and work practice controls to reduce and maintain employee exposure to respirable crystalline silica to or below the PEL, unless the employer can demonstrate that such controls are not feasible. Wherever such feasible engineering and work practice controls are not sufficient to reduce employee exposure to or below the PEL, the employer shall nonetheless use them to reduce employee exposure to the lowest feasible level and shall supplement them with the use of respiratory protection that complies with the requirements of paragraph (e) of this section.
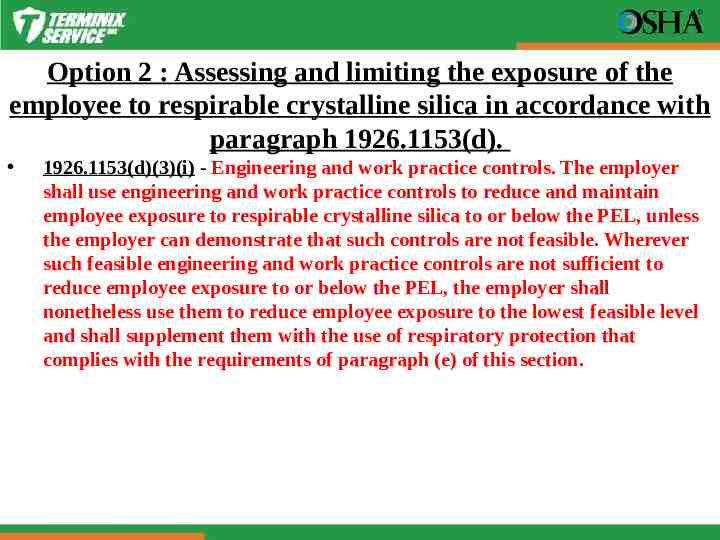
Option 2 : Assessing and limiting the exposure of the employee to respirable crystalline silica in accordance with paragraph 1926.1153(d). So . Who has the available resources to hire a certified company to perform an “Industrial Hygiene Study” to determine whether or not your employees fall above or below the OSHA TWA & AL PELs set in the standard so you can determine whether or not you need to purchase equipment to comply with “Table 1”?
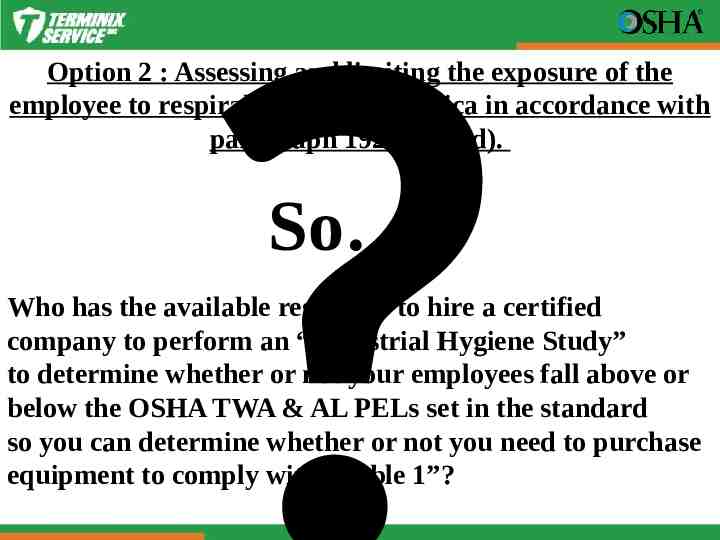
How many of you are members of NPMA?
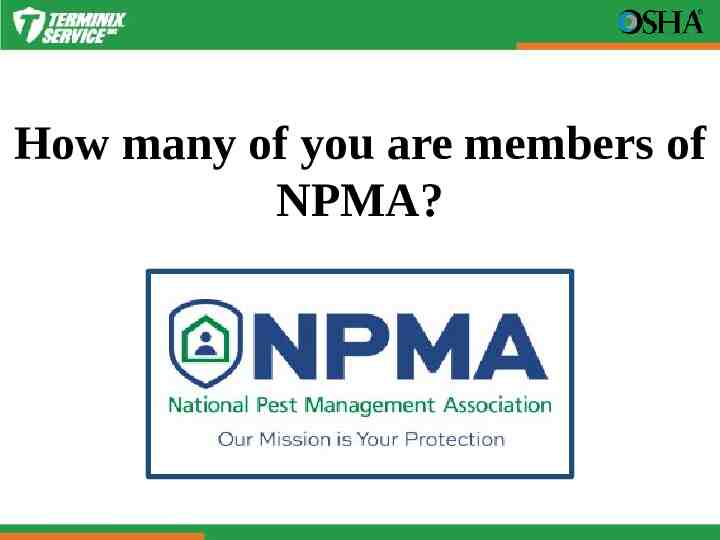
NPMA had an Industrial Hygiene Study performed earlier this year with 2 member companies. The study evaluated respirable crystalline silica (RCS) levels for 2 member company employees when performing a termite treatment. Based on data collected from two sites, TWA exposures during Exterior Perimeter/ Localized Interior treatment (EP/LI) should not exceed the AL if total drilling is less than 4 hours per day. This assumes an outdoor to indoor drilling ratio of 10:1.
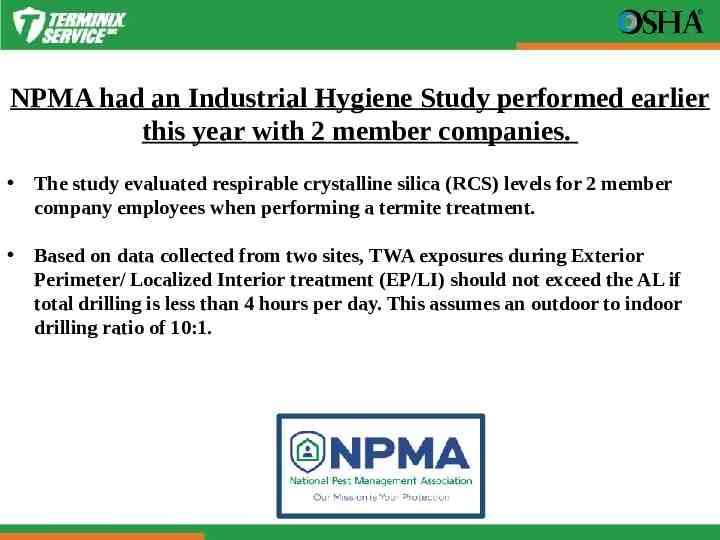
Estimating TWA exposures during a conventional termite treatment is more challenging than the EP/LI treatment because of the varied ratio of indoor vs. outdoor drilling between members. To calculate TWA’s, we assumed that outdoor drilling would be 50% of indoor drilling. Based on that assumption and maximum exposure data, the AL could be exceeded if more than 40 minutes of indoor drilling was performed. A statistical analysis was performed and the arithmetic mean of log normal distribution for 60 minutes of indoor drilling is 21.25 ug/m3 which is below the AL. The analysis also indicates that for 60 minutes of indoor drilling there is a 30% probability of exceeding the AL. The air sampling data demonstrates a log normal distribution.
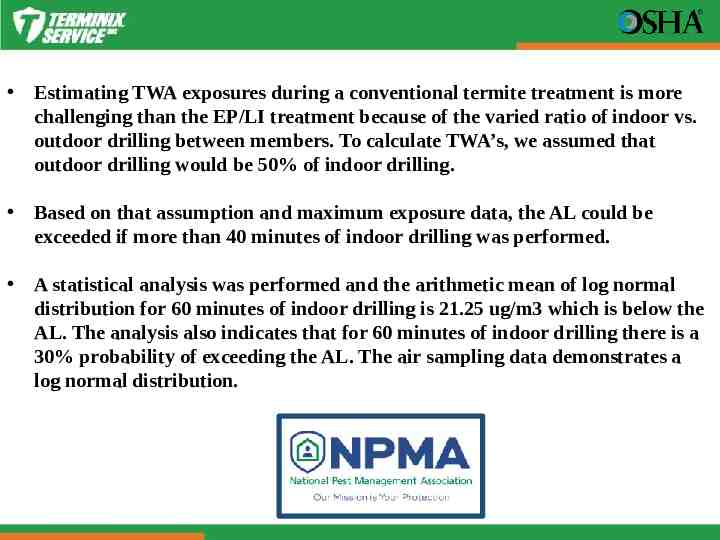
Good news! Whether or not you are a NPMA member, NPMA has made the Industrial Hygiene Study available to everyone industry wide. They also have a customizable control plan that you can use to update your Hazard Communication, Hazard Assessment & Respiratory Protection Plans. You can access this information free of charge @ https://www.qualityprotools.org/osha-toolbox/respirable-silica/ To log into the website, just enter the word “osha” as the User Name & Password.
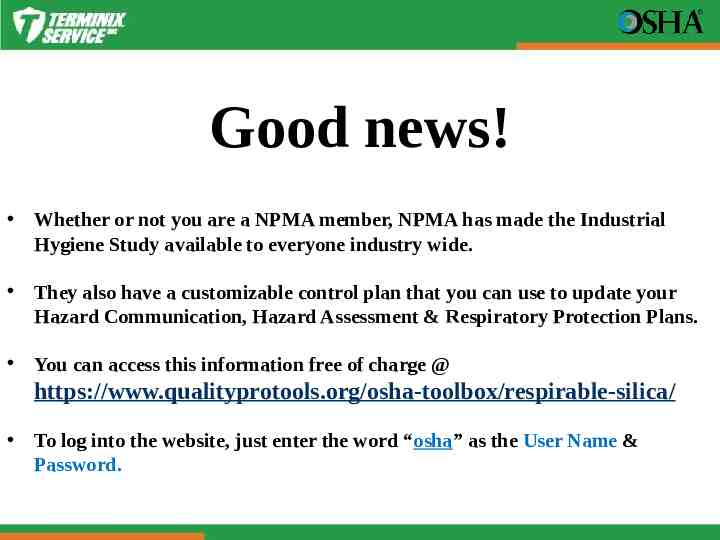
Industrial Hygiene Study Based on data collected from NPMA member companies, 95% of all liquid termite treatments are EP/LI (Exterior Perimeter/Localized Interior) treatments & 5% are conventional comprehensive treatments. TWA exposures during (EP/LI) treatments should not exceed the AL if total drilling is less than 4 hours per day. This assumes an outdoor to indoor drilling ratio of 10:1.

Industrial Hygiene Study Estimating TWA exposures during a conventional termite treatment is more challenging than an EP/LI treatment because of the varied ratio of indoor vs. outdoor drilling between members. For conventional treatments, where indoor drilling may equal outdoor drilling (50:50 ratio), the AL could be exceeded if more than 40 minutes of indoor drilling was performed.
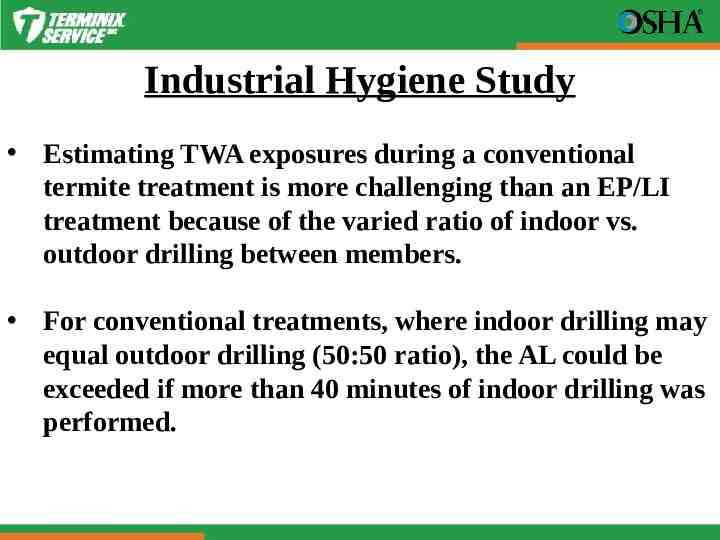
Compliance with 1926.1153(c)(1) If you limit each employee to 4 hours per day drilling masonry on EP/LI treatments you should not have to comply with the engineering & work practice control methods in “Table 1” except using a HEPA vacuum for dust collection. When interior drilling is performed on an EP/LI treatment, if you limit interior drilling to 40 minutes per day you should not have to comply with the engineering & work practice control methods in “Table 1” except using a HEPA vacuum for dust collection.
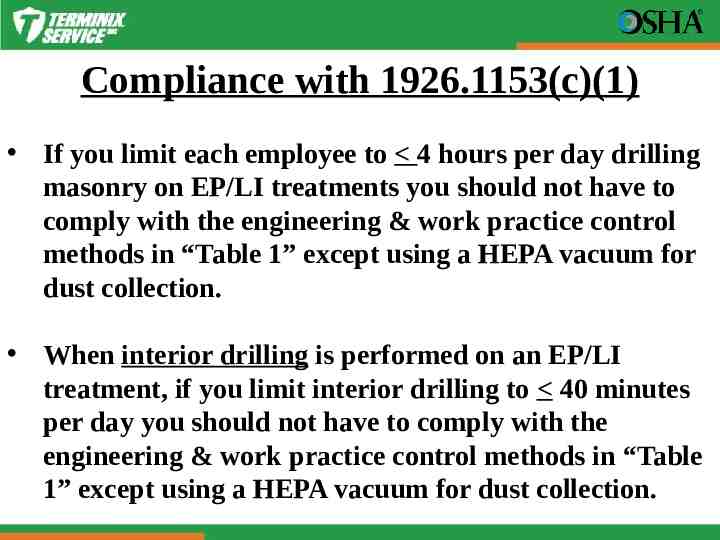
Compliance with 1926.1153(c)(1) The results of the study will allow you to set your Hazard Communication, Hazard Assessment & Respiratory Protection Plans to allow technicians to perform most liquid termite treatments without having to comply with everything on “Table 1” except using a HEPA vacuum for dust collection. **** Using a HEPA vacuum or **** wet sweeping methods MUST be used for dust collection!
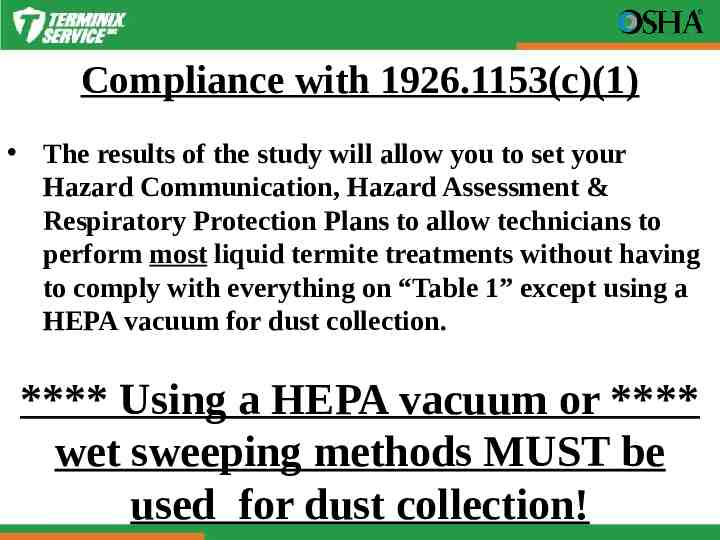
So far we have covered 1926.1153(a) through (d) but there are 5 more sections of the standard: 1926.1153(e) Respiratory protection 1926.1153(f) Housekeeping 1926.1153(g) Written exposure control plan 1926.1153(h) Medical surveillance 1926.1153(i) Communication of respirable crystalline silica hazards to employees
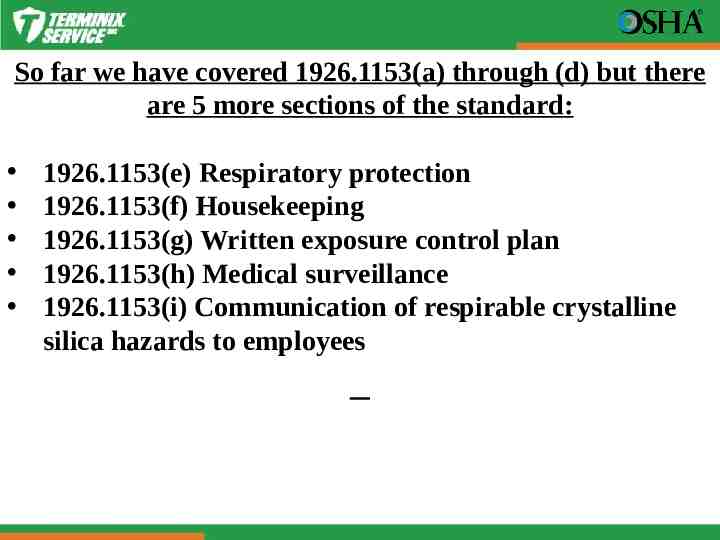
Regardless of your chosen method, the standard states you MUST: Provide respiratory protection when required; Restrict housekeeping practices that expose employees to Respirable crystalline silica where feasible alternatives are available; Establish & implement a written exposure plan, including a competent person;
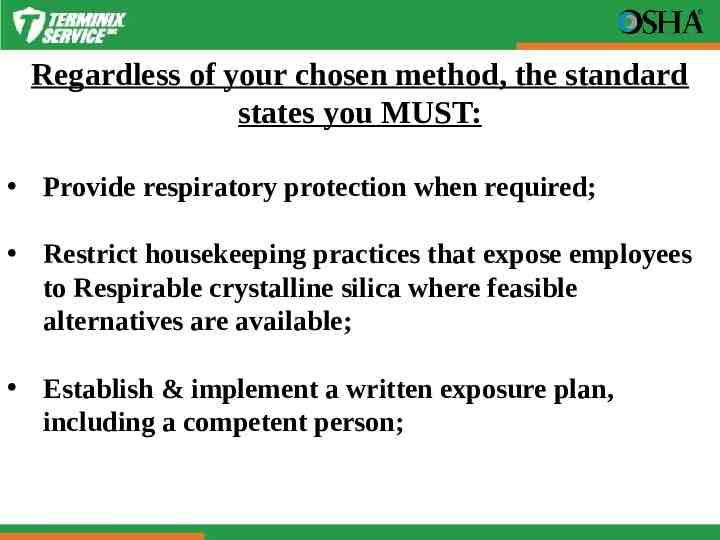
Regardless of your chosen method, you MUST: Offer medical exams to employees who will be required to wear a respirator under the standard for 30 days or more a year; Communicate hazards & train employees; and Keep records of any medical exams
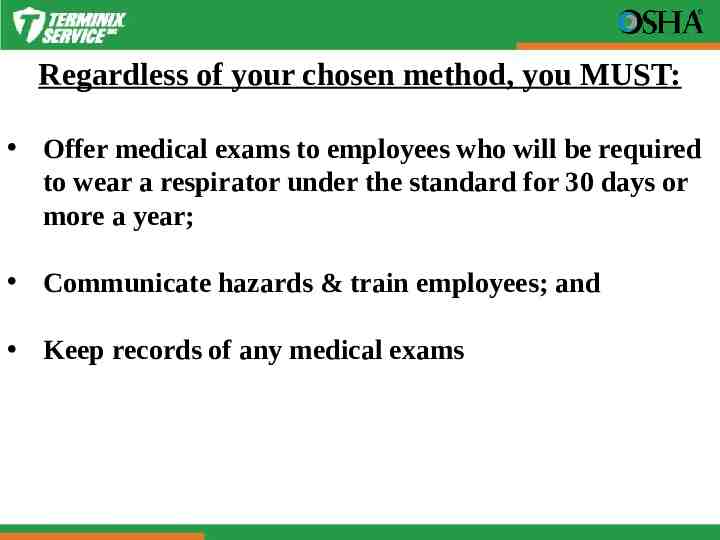
Compliance To ensure you stay in compliance with the standard when updating your Hazard Communication, Hazard Assessment & Respiratory Protection Plans, you can use OSHA’s “Attachment A: Enforcement Guidance” section on OSHA’s website. https://www.osha.gov/laws-regs/ standardinterpretations/2017-10-19
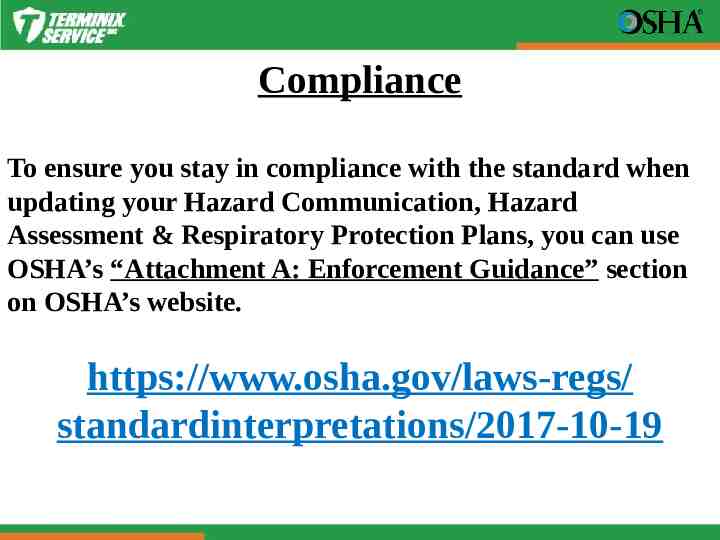
Available Training NPMA also has a course called “OSHA’s Respirable Silica Standard Training” that is available in the on the NPMA @ npmatraining.org Resource Center / Online Learning Center / Occupational Health & Safety The fee for this training is 4.99 for NPMA members & 9.99 for non-members
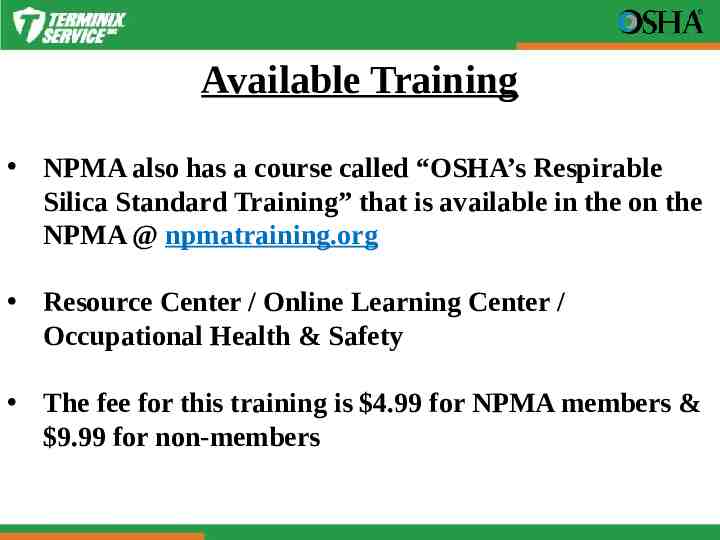
October 1st – 3rd 2018 Thank You! *** Special thanks to our friends at the National Pest Management Association ***
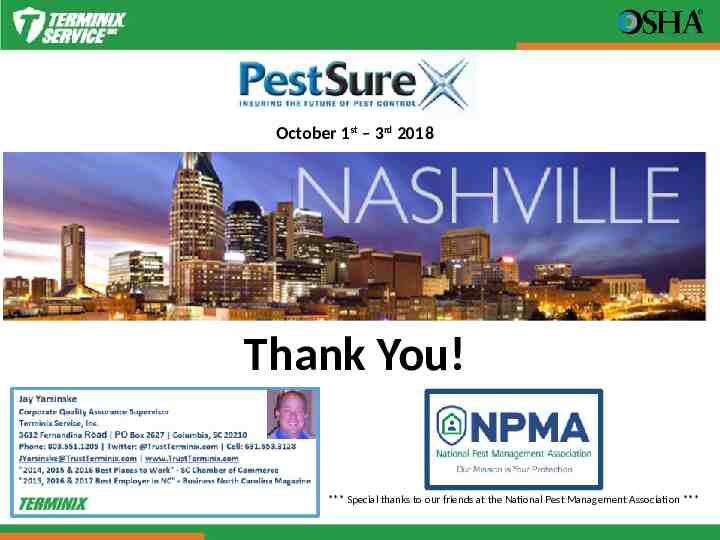