For Food Processing Presented by
23 Slides6.37 MB
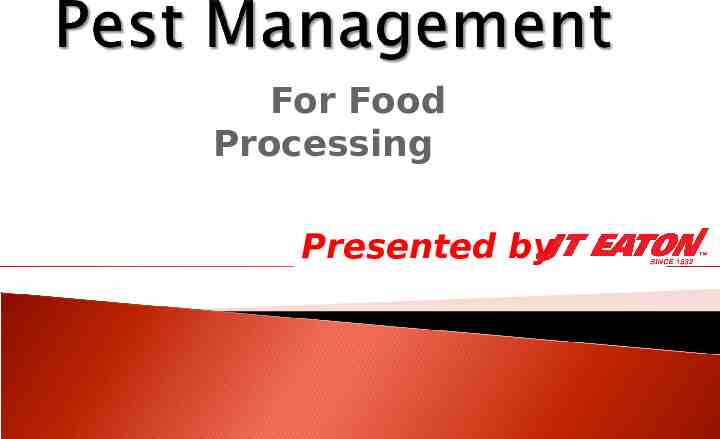
For Food Processing Presented by
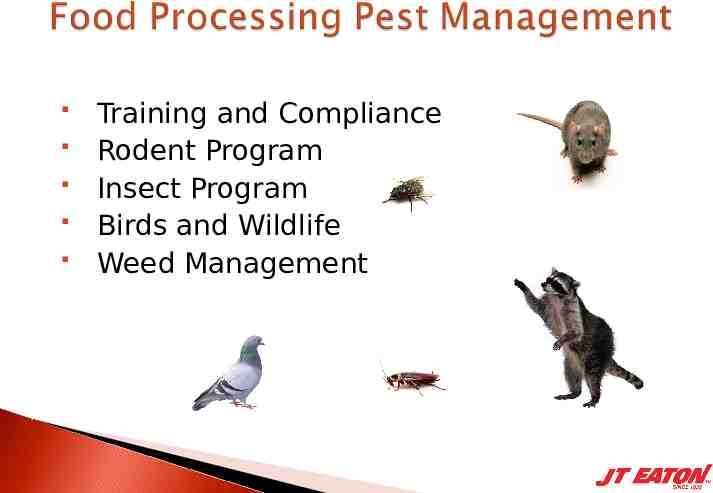
Training and Compliance Rodent Program Insect Program Birds and Wildlife Weed Management
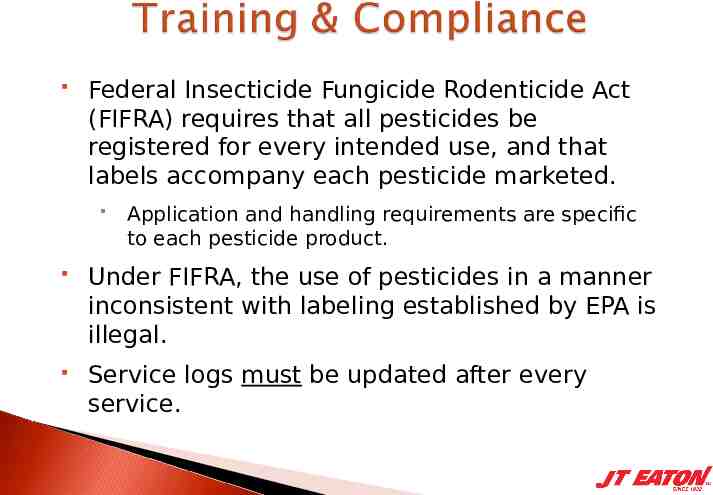
Federal Insecticide Fungicide Rodenticide Act (FIFRA) requires that all pesticides be registered for every intended use, and that labels accompany each pesticide marketed. Application and handling requirements are specific to each pesticide product. Under FIFRA, the use of pesticides in a manner inconsistent with labeling established by EPA is illegal. Service logs must be updated after every service.
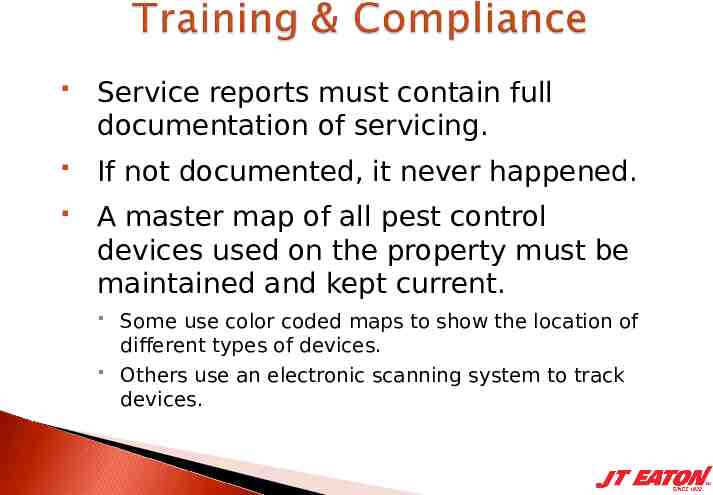
Service reports must contain full documentation of servicing. If not documented, it never happened. A master map of all pest control devices used on the property must be maintained and kept current. Some use color coded maps to show the location of different types of devices. Others use an electronic scanning system to track devices.
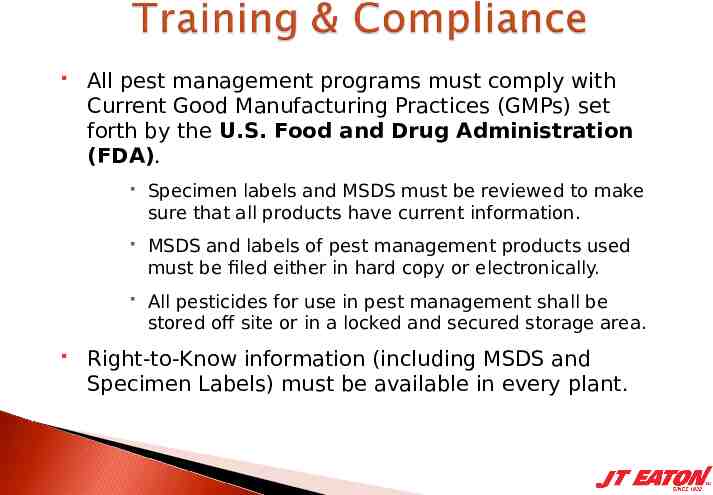
All pest management programs must comply with Current Good Manufacturing Practices (GMPs) set forth by the U.S. Food and Drug Administration (FDA). Specimen labels and MSDS must be reviewed to make sure that all products have current information. MSDS and labels of pest management products used must be filed either in hard copy or electronically. All pesticides for use in pest management shall be stored off site or in a locked and secured storage area. Right-to-Know information (including MSDS and Specimen Labels) must be available in every plant.
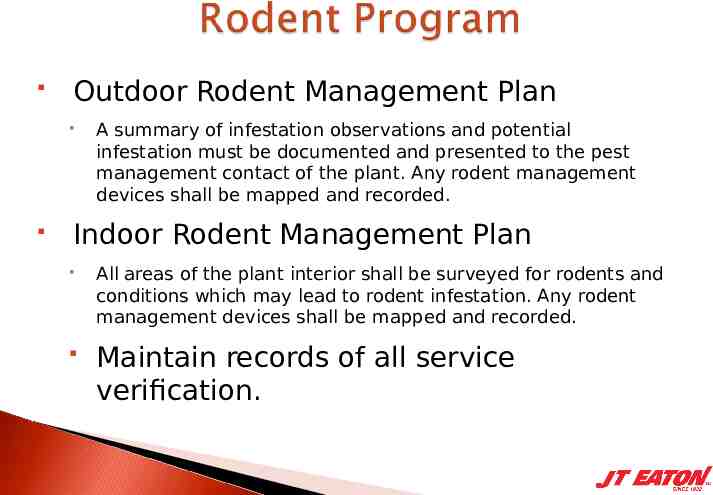
Outdoor Rodent Management Plan A summary of infestation observations and potential infestation must be documented and presented to the pest management contact of the plant. Any rodent management devices shall be mapped and recorded. Indoor Rodent Management Plan All areas of the plant interior shall be surveyed for rodents and conditions which may lead to rodent infestation. Any rodent management devices shall be mapped and recorded. Maintain records of all service verification.
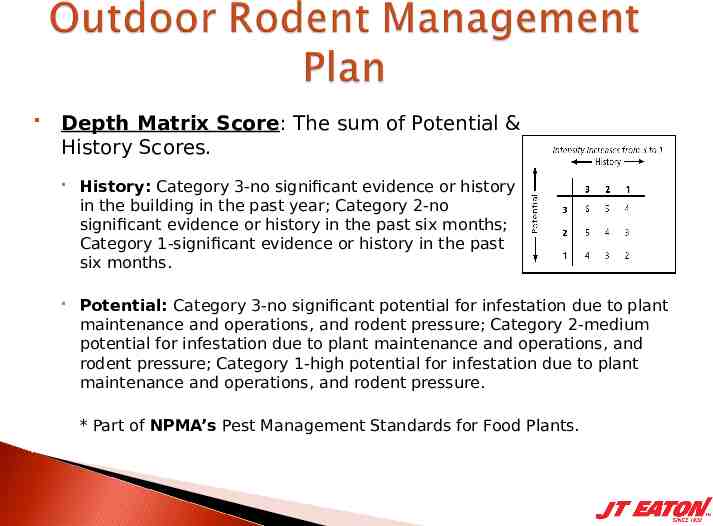
Depth Matrix Score: The sum of Potential & History Scores. History: Category 3-no significant evidence or history in the building in the past year; Category 2-no significant evidence or history in the past six months; Category 1-significant evidence or history in the past six months. Potential: Category 3-no significant potential for infestation due to plant maintenance and operations, and rodent pressure; Category 2-medium potential for infestation due to plant maintenance and operations, and rodent pressure; Category 1-high potential for infestation due to plant maintenance and operations, and rodent pressure. * Part of NPMA’s Pest Management Standards for Food Plants.
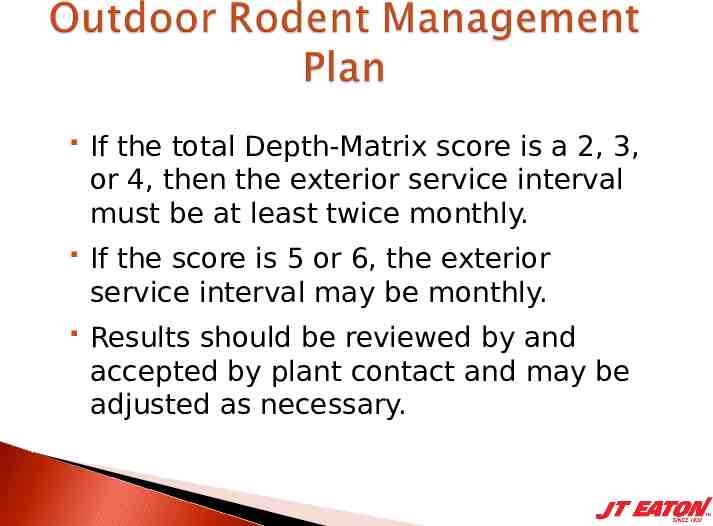
If the total Depth-Matrix score is a 2, 3, or 4, then the exterior service interval must be at least twice monthly. If the score is 5 or 6, the exterior service interval may be monthly. Results should be reviewed by and accepted by plant contact and may be adjusted as necessary.
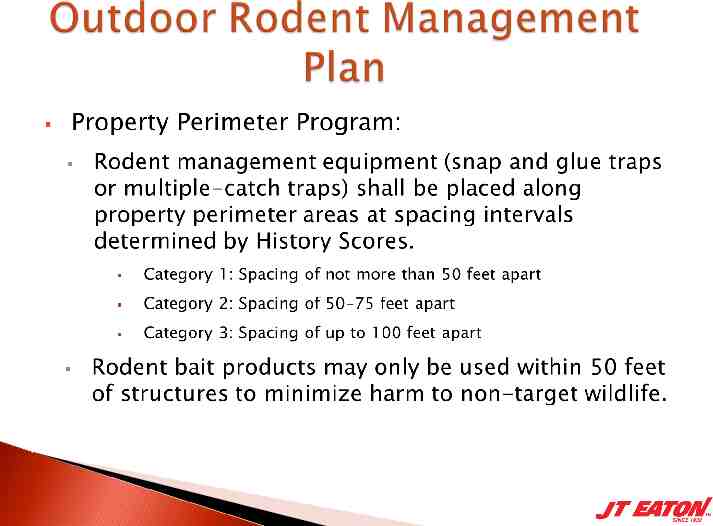
Multiple-catch traps may be supplemented at a rate determined by the technician with snap traps in stations or glue boards if placed into stations or covers (PVC pipes or Bait Stations). The inside of any exterior wall should have multiplecatch traps or glue boards in stations at the rate of one every 20 feet for mice and one every 40 feet or more for rats. Rodenticides shall not be used inside food plants in any area unless approved by the plant contact and permitted by label.
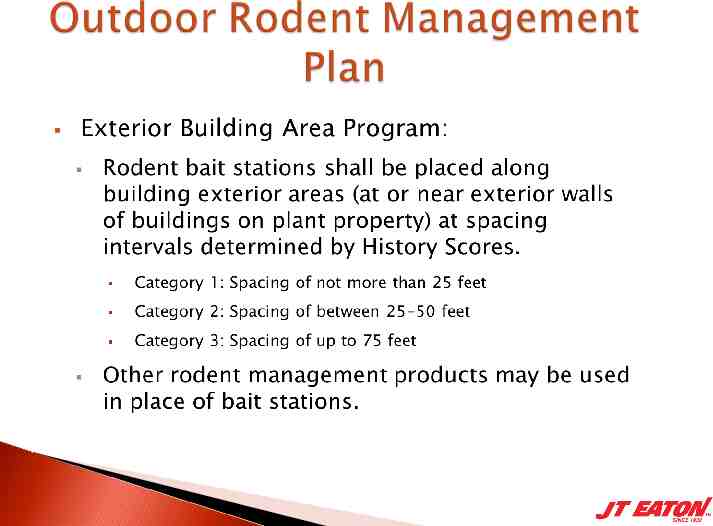
Rodent management devices should be added adjacent to doors, docks, and ramps, but may be placed adjacent to any exterior opening per company practices. Plants must have an inspection aisle of at least 18-24 inches along walls. This area is painted white in order to contrast with droppings or insects. Do not use peanut butter or nut based attractants inside a plant due to allergen concerns. Synthetic peanut butter scents may be approved for use. Rodents must be disposed of in a sanitary method offsite. Rodents, droppings, and any urine deposits or residue must be handled using protective gear.
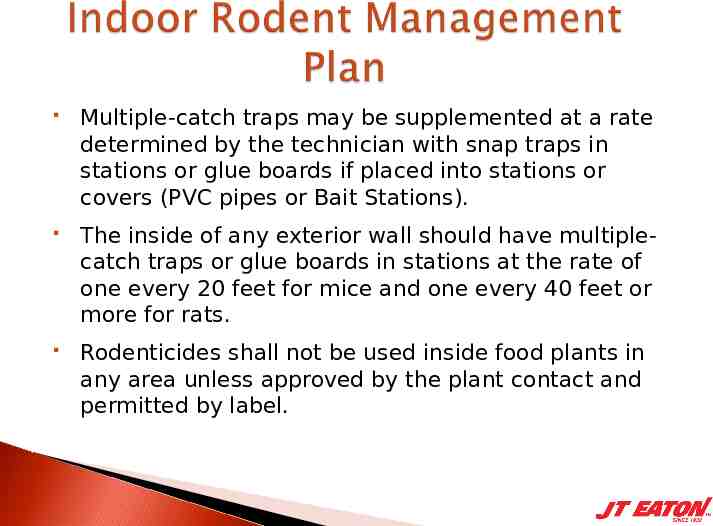
Rodent Bait Stations Bait Blocks Glue Traps Glue Boards Live Catch Mouse Traps Snap Traps
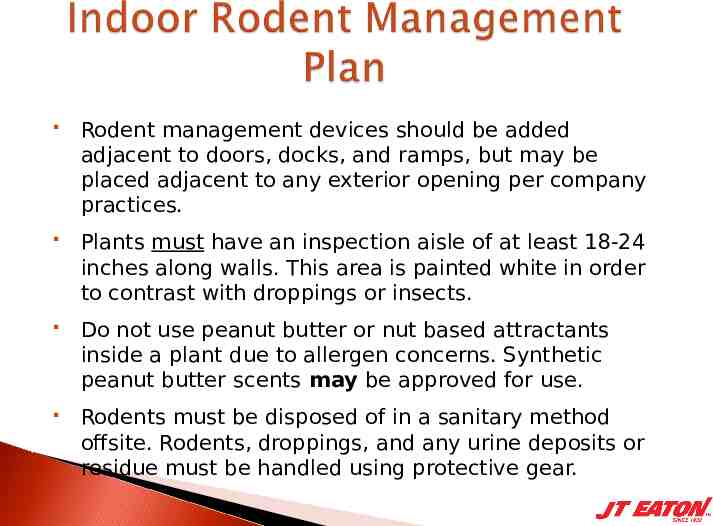
Conduct a thorough inspection of the exterior of the building for signs of rodent and insect activity. Conduct a thorough inspection of the accessible components of the plant not less than monthly. Pheromones and pheromone traps may be used as part of the monitoring and management processes. Insects shall be managed using a product labeled for the site (residual or non-residual). Space treatment may be used to reduce adult populations (including use of insect growth regulators- IGRs) as per label.
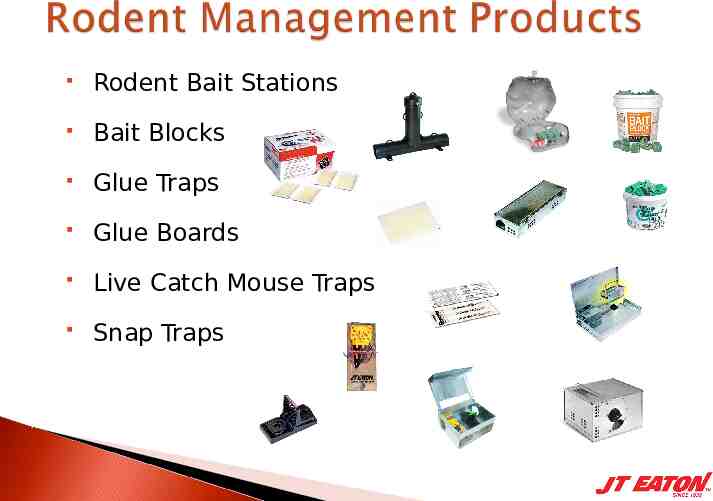
Insect Light Traps and Flying Insect Traps Insect light traps (ILTs) may be installed to monitor and manage certain flying insects (e.g. Indianmeal moths, fruit flies, etc.). Findings and seasonal requirements will dictate frequency of inspection. Placement (2-5 feet above floor level) must be according to manufacturer’s instructions and in compliance with any regulatory policies and guidelines. ILTs must be monitored based upon the contract. Bulbs in ILTs must be changed according to manufacturer’s recommendations (at least annually). Shatter protection must be in place where food or packaging may become contaminated by glass (and other areas dictated by inspectors). Sticky type ILTs must be monitored at least monthly and the sticky board must be replaced if ineffective. Weekly monitoring is suggested. Type of insects on the board must be recorded and categorized.
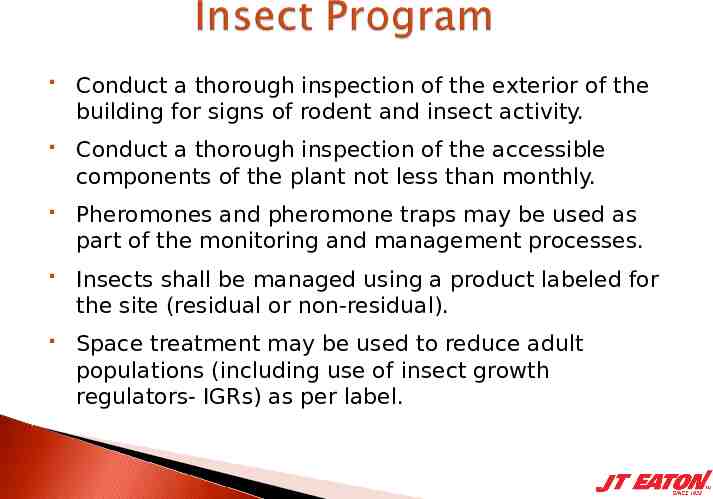
Insect Light Lamps Glue Boards Insecticides Other Traps
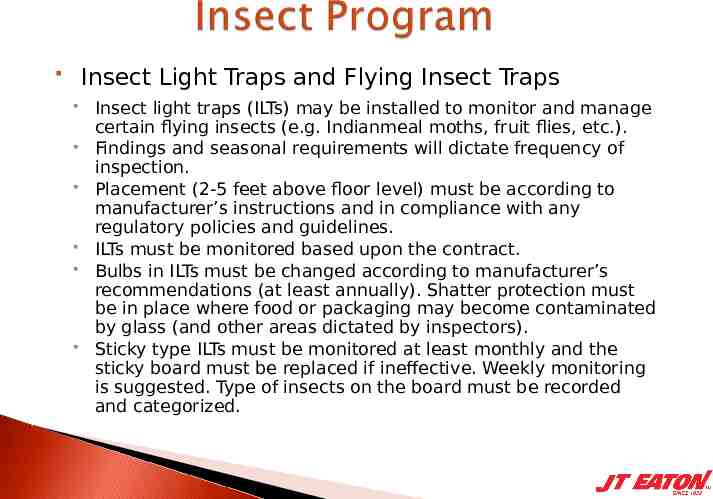
Bird prevention measures may be installed. These shall be any type of wire, net, device, or material to prevent roosting. Any interior bird removal shall be by trapping and removal in accordance with regulations. Exterior infestations such as geese on grounds may be managed by scaring devices or repellents. Use of protective gear shall be required for removal of nests and/or droppings. Any miscellaneous animal removal shall be by trapping and removal in accordance with local regulations. Exterior infestations such as prairie dogs on grounds may be managed by repellents, trapping or other methods according to label or instructions.
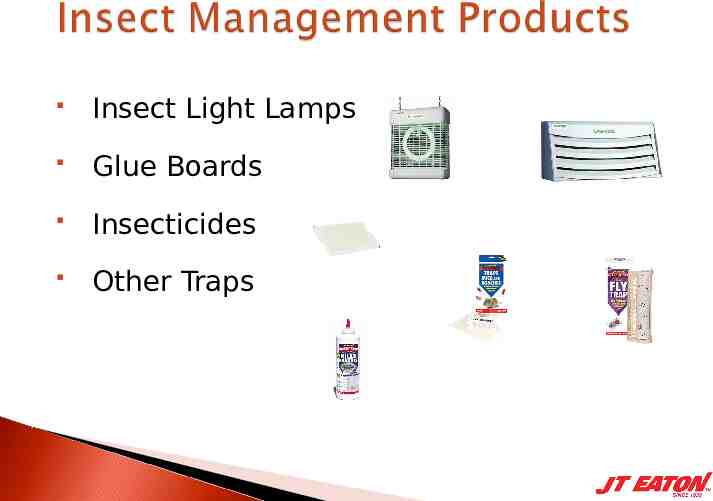
Scaring Devices Netting Devices Poison/Bait Repellants Cages Traps
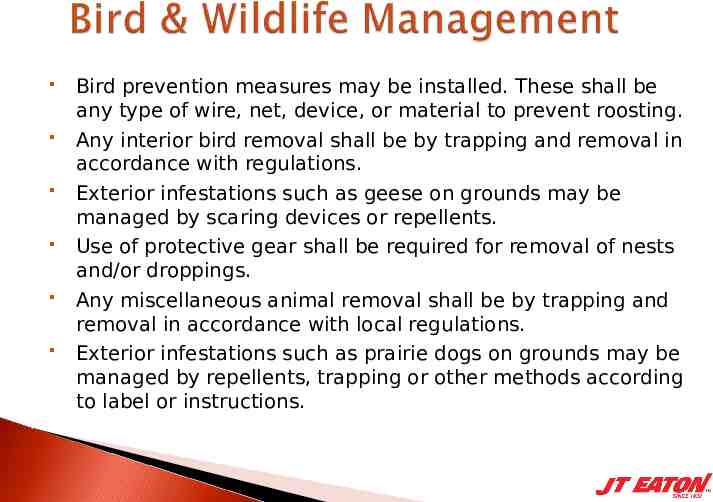
Vegetation should not be planted against the exterior of the buildings as it fosters rodent and insect life. This area can be filled with an 18-24 inch band of stone to prevent rodent burrowing and insect ingress. An inspection band and clear zone adjacent to the building should be encouraged as part of the periodic audit.
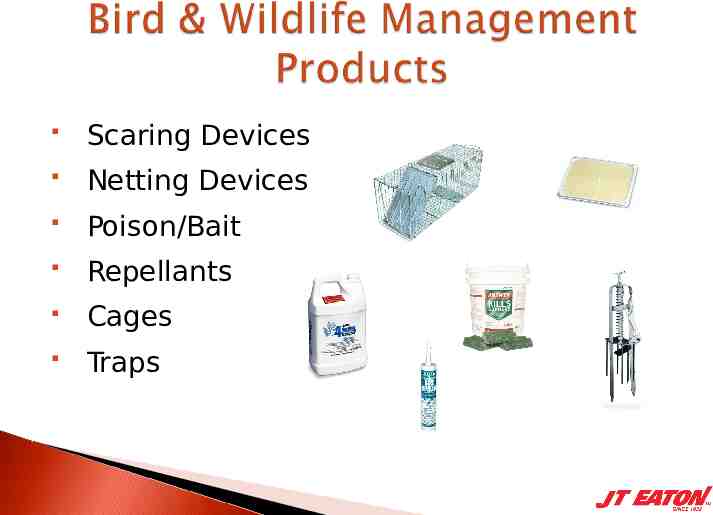
Food Product Table 1-3: Maximum Defect Action Levels for Selected Food Products Maximum Defect Action Level Allspice (ground) Average of 30 or more insect fragments per 10 grams Average of 1 or more rodent hairs per 10 grams Broccoli (frozen) Average of 60 or more aphids, thrips, and/or mites per 100 grams Cocoa beans More than 4% of beans by count are moldy More than 4% of beans by count are insect-infested or insect-damaged More than 6% of beans by count are insect-infested or moldy (NOTE: Level differs when both filth and mold are present) Average of 10 mg or more mammalian excreta per pound Pitted olives Average of 1.3 percent or more by count of olives with whole pits and/or pit fragments 2 mm or longer measured in the longest dimension Pineapple juice Average mold count of 15% or more Mold count of any 1 subsample is 40% or more Tomatoes (canned) Average of 10 or more fly eggs per 500 grams 5 or more fly eggs and 1 or more maggots per 500 grams 2 or more maggots per 500 grams Source: FDA, 2004.
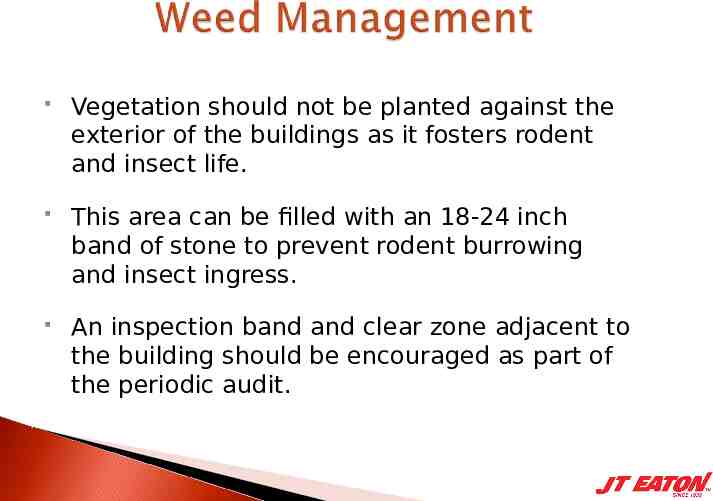
For full details on Food Plant Standards, consult the Pest Management Standards for Food Plants put out by the National Pest Management Association. NPMA 10460 North Street, Fairfax, VA 22030 703-352-NPMA (6762) fax 703-352-3031 www.npmapestworld.org
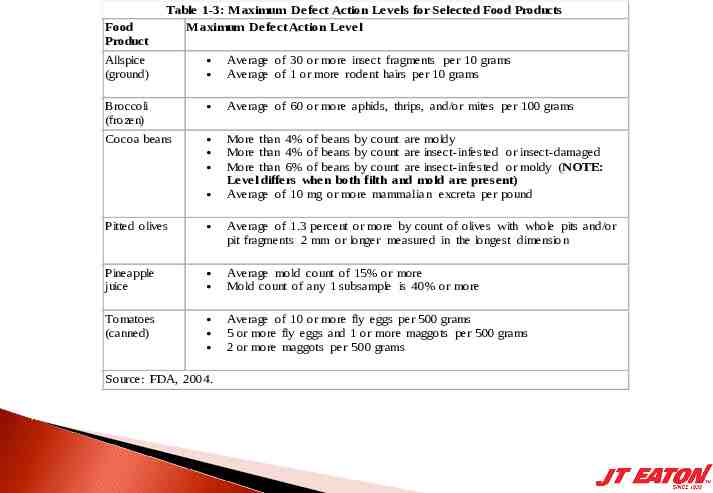
U.S. Food and Drug Administration Good Manufacturing Practices American Institute of Baking Food Safety Audits and Education
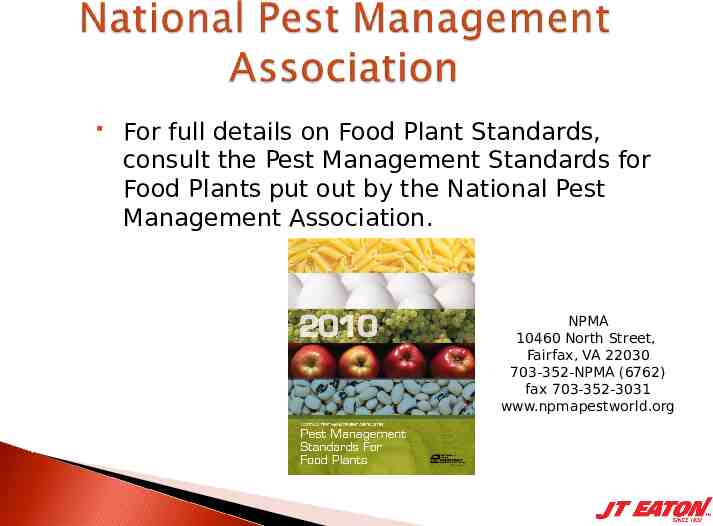
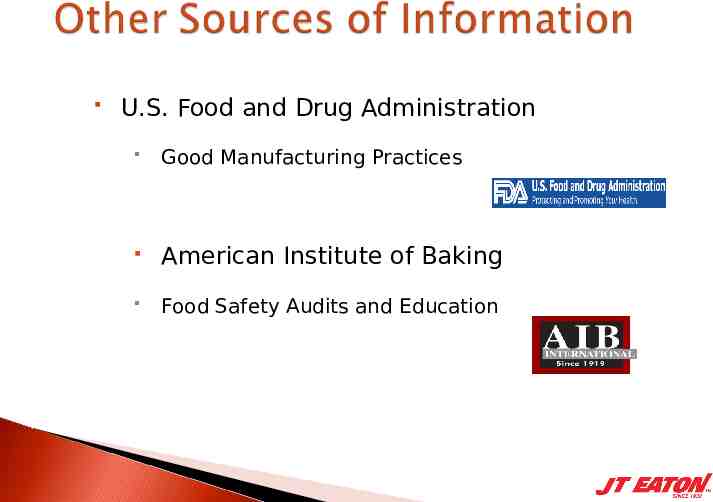
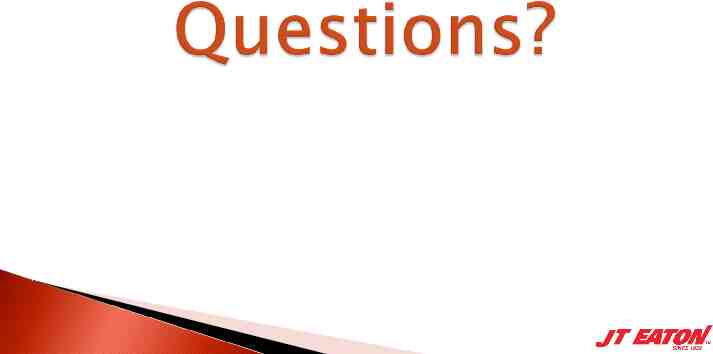