Dynamic Car Planning CSXT’s optimized empty car distribution system
20 Slides1.77 MB
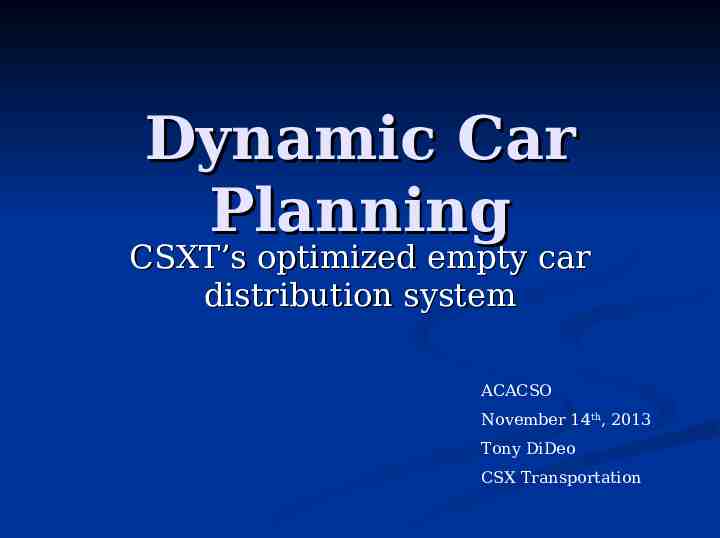
Dynamic Car Planning CSXT’s optimized empty car distribution system ACACSO November 14th, 2013 Tony DiDeo CSX Transportation
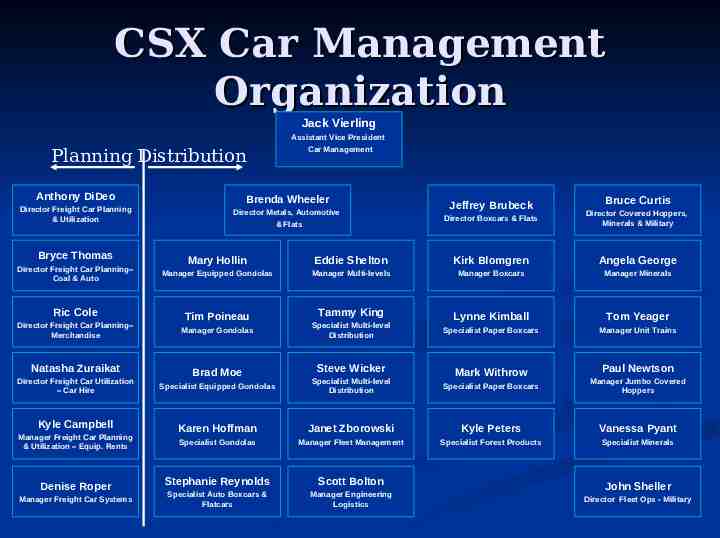
CSX Car Management Organization Jack Vierling Planning Distribution Anthony DiDeo Director Freight Car Planning & Utilization Bryce Thomas Director Freight Car Planning– Coal & Auto Ric Cole Director Freight Car Planning– Merchandise Natasha Zuraikat Director Freight Car Utilization – Car Hire Kyle Campbell Manager Freight Car Planning & Utilization – Equip. Rents Denise Roper Manager Freight Car Systems Assistant Vice President Car Management Brenda Wheeler Director Metals, Automotive & Flats Jeffrey Brubeck Bruce Curtis Director Boxcars & Flats Director Covered Hoppers, Minerals & Military Mary Hollin Eddie Shelton Kirk Blomgren Angela George Manager Equipped Gondolas Manager Multi-levels Manager Boxcars Manager Minerals Tim Poineau Manager Gondolas Brad Moe Specialist Equipped Gondolas Tammy King Specialist Multi-level Distribution Steve Wicker Specialist Multi-level Distribution Lynne Kimball Tom Yeager Specialist Paper Boxcars Manager Unit Trains Mark Withrow Paul Newtson Specialist Paper Boxcars Manager Jumbo Covered Hoppers Karen Hoffman Janet Zborowski Kyle Peters Vanessa Pyant Specialist Gondolas Manager Fleet Management Specialist Forest Products Specialist Minerals Stephanie Reynolds Scott Bolton Specialist Auto Boxcars & Flatcars Manager Engineering Logistics John Sheller Director Fleet Ops - Military
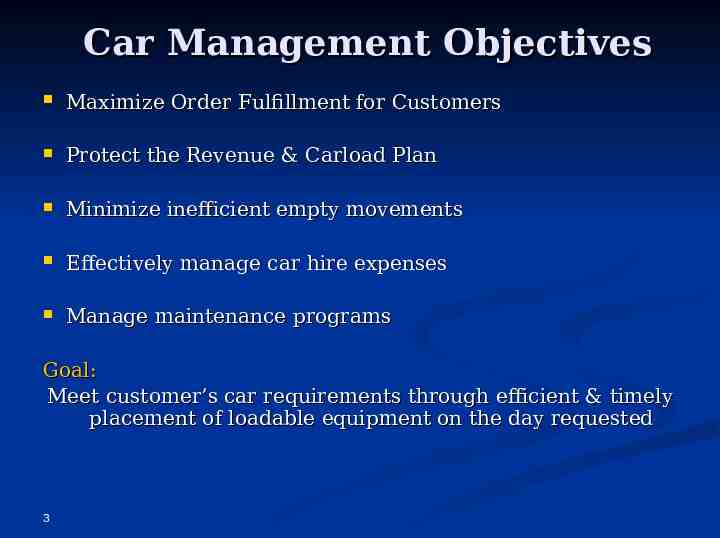
Car Management Objectives Maximize Order Fulfillment for Customers Protect the Revenue & Carload Plan Minimize inefficient empty movements Effectively manage car hire expenses Manage maintenance programs Goal: Meet customer’s car requirements through efficient & timely placement of loadable equipment on the day requested 3

CSX manages 5,000-7,000 empty car orders per week Car orders are entered through our web-based ShipCSX system Online Customers enter orders directly into ShipCSX 84% Online Customers 16% Ordered by Short Line or their customers These orders account for approximately 25%30% of our originated Merchandise carloads Unit Train, Coal, Automotive & Intermodal traffic do not use car order system Orders are placed for railroad controlled cars only (excludes privates) 4
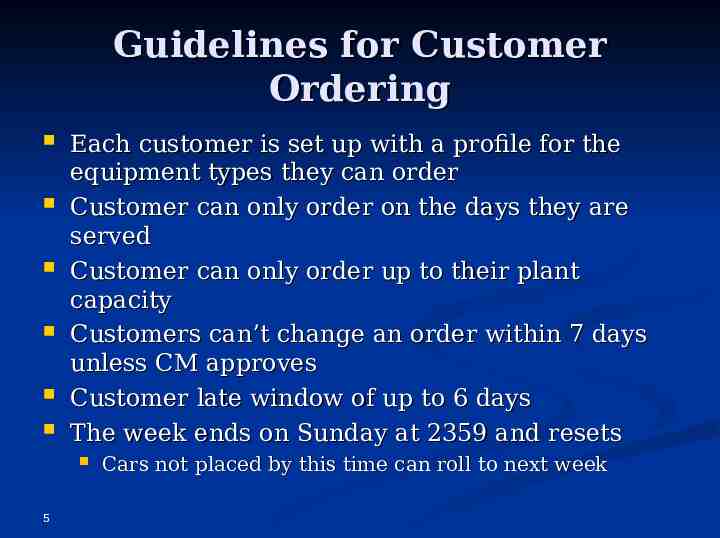
Guidelines for Customer Ordering Each customer is set up with a profile for the equipment types they can order Customer can only order on the days they are served Customer can only order up to their plant capacity Customers can’t change an order within 7 days unless CM approves Customer late window of up to 6 days The week ends on Sunday at 2359 and resets 5 Cars not placed by this time can roll to next week
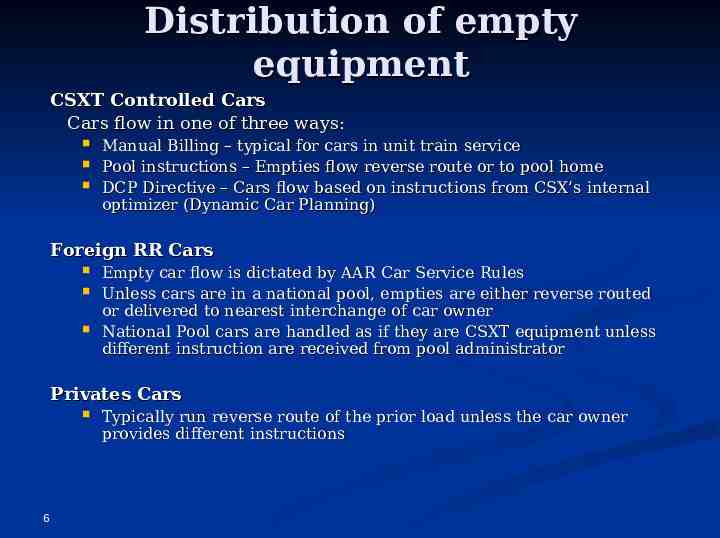
Distribution of empty equipment CSXT Controlled Cars Cars flow in one of three ways: Manual Billing – typical for cars in unit train service Pool instructions – Empties flow reverse route or to pool home DCP Directive – Cars flow based on instructions from CSX’s internal optimizer (Dynamic Car Planning) Foreign RR Cars Empty car flow is dictated by AAR Car Service Rules Unless cars are in a national pool, empties are either reverse routed or delivered to nearest interchange of car owner National Pool cars are handled as if they are CSXT equipment unless different instruction are received from pool administrator Privates Cars 6 Typically run reverse route of the prior load unless the car owner provides different instructions
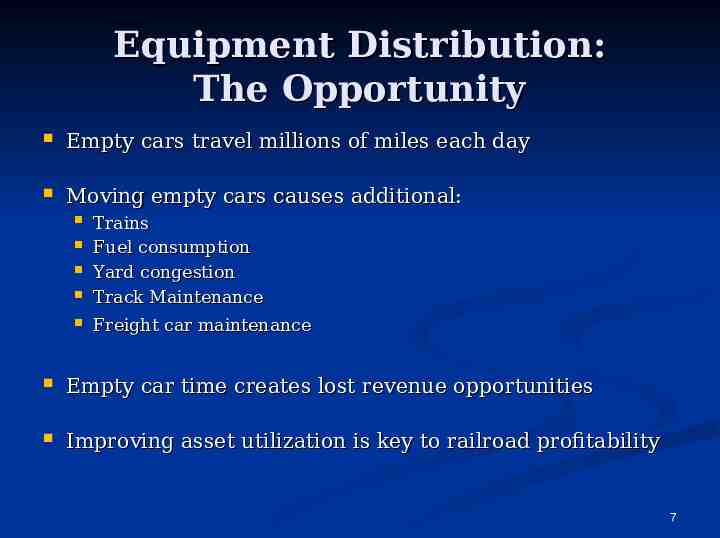
Equipment Distribution: The Opportunity Empty cars travel millions of miles each day Moving empty cars causes additional: Trains Fuel consumption Yard congestion Track Maintenance Freight car maintenance Empty car time creates lost revenue opportunities Improving asset utilization is key to railroad profitability 7
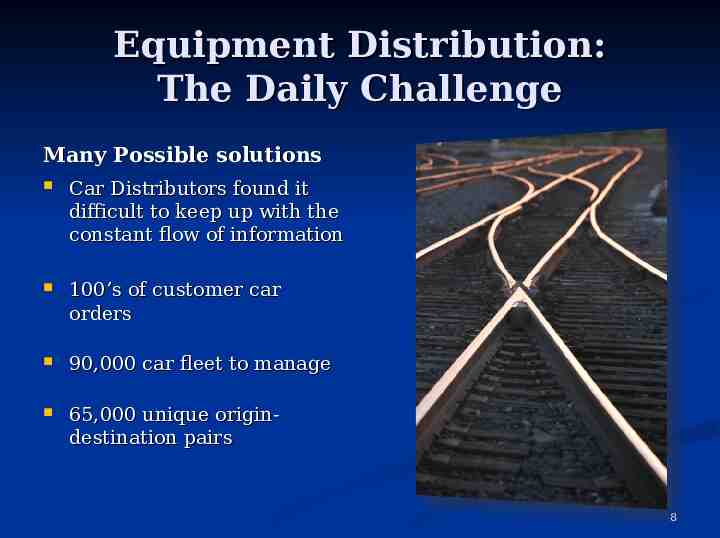
Equipment Distribution: The Daily Challenge Many Possible solutions Car Distributors found it difficult to keep up with the constant flow of information 100’s of customer car orders 90,000 car fleet to manage 65,000 unique origindestination pairs 8
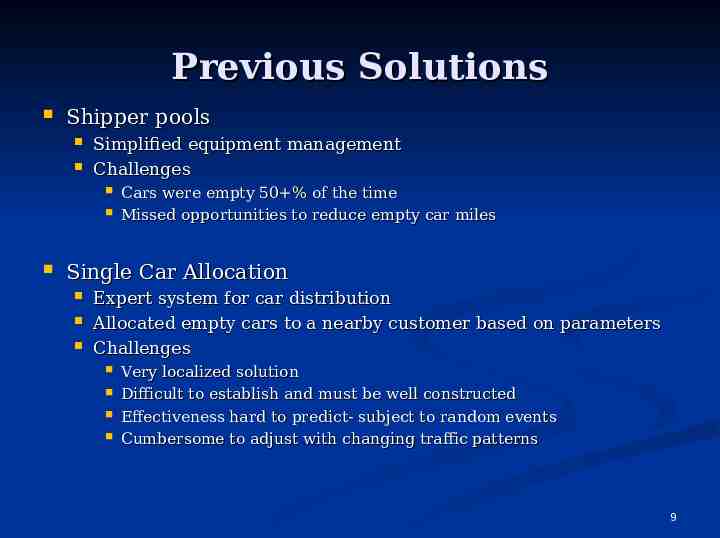
Previous Solutions Shipper pools Simplified equipment management Challenges Cars were empty 50 % of the time Missed opportunities to reduce empty car miles Single Car Allocation Expert system for car distribution Allocated empty cars to a nearby customer based on parameters Challenges Very localized solution Difficult to establish and must be well constructed Effectiveness hard to predict- subject to random events Cumbersome to adjust with changing traffic patterns 9
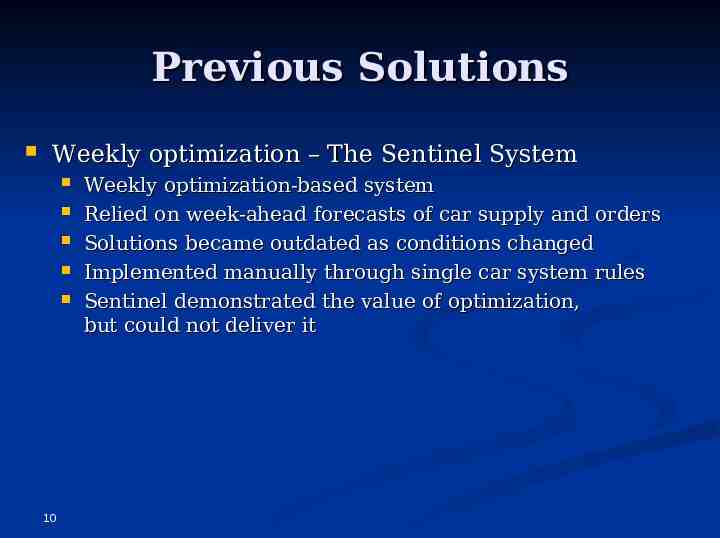
Previous Solutions Weekly optimization – The Sentinel System 10 Weekly optimization-based system Relied on week-ahead forecasts of car supply and orders Solutions became outdated as conditions changed Implemented manually through single car system rules Sentinel demonstrated the value of optimization, but could not deliver it
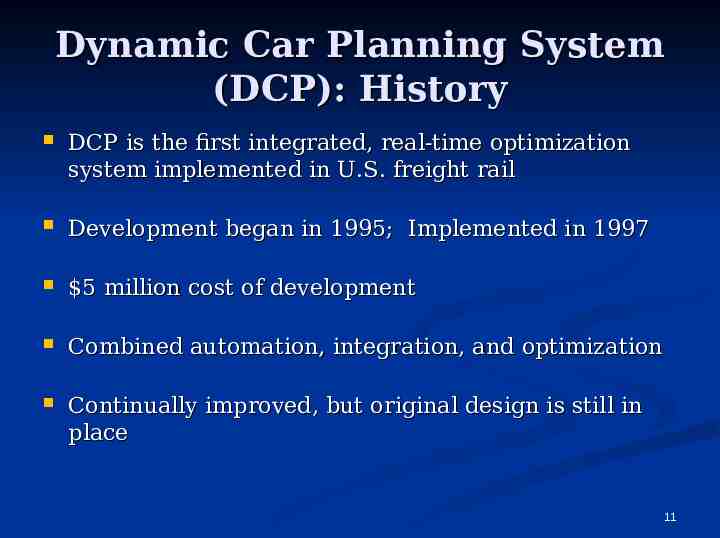
Dynamic Car Planning System (DCP): History DCP is the first integrated, real-time optimization system implemented in U.S. freight rail Development began in 1995; Implemented in 1997 5 million cost of development Combined automation, integration, and optimization Continually improved, but original design is still in place 11
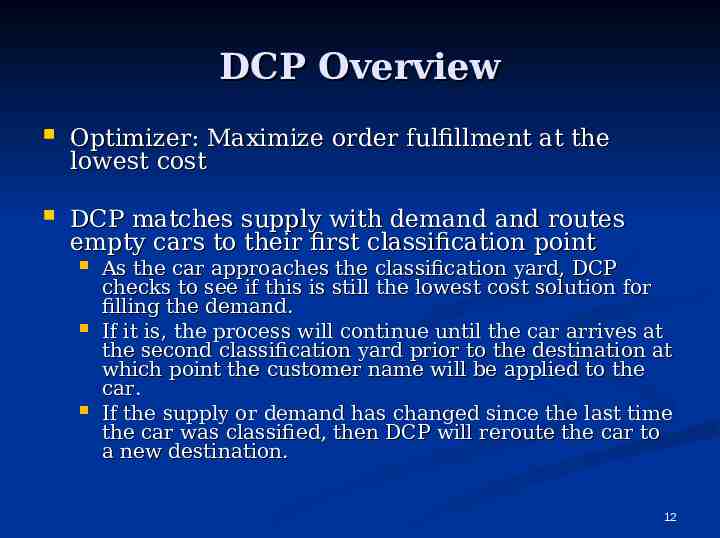
DCP Overview Optimizer: Maximize order fulfillment at the lowest cost DCP matches supply with demand and routes empty cars to their first classification point As the car approaches the classification yard, DCP checks to see if this is still the lowest cost solution for filling the demand. If it is, the process will continue until the car arrives at the second classification yard prior to the destination at which point the customer name will be applied to the car. If the supply or demand has changed since the last time the car was classified, then DCP will reroute the car to a new destination. 12
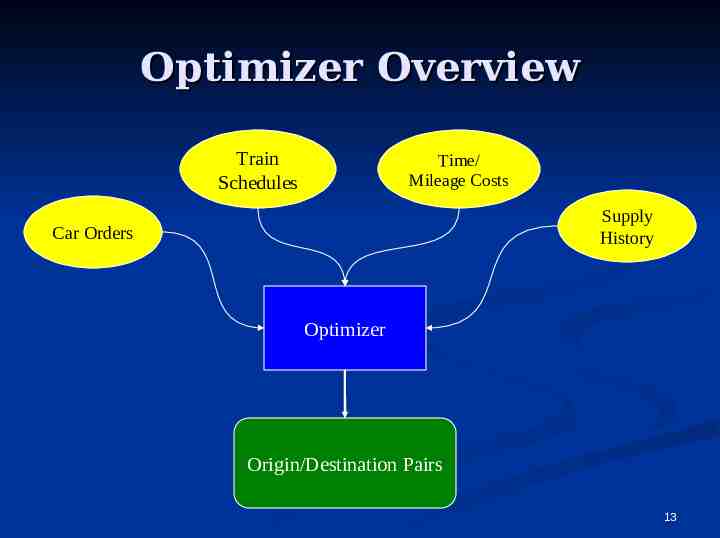
Optimizer Overview Train Schedules Time/ Mileage Costs Supply History Car Orders Optimizer Origin/Destination Pairs 13
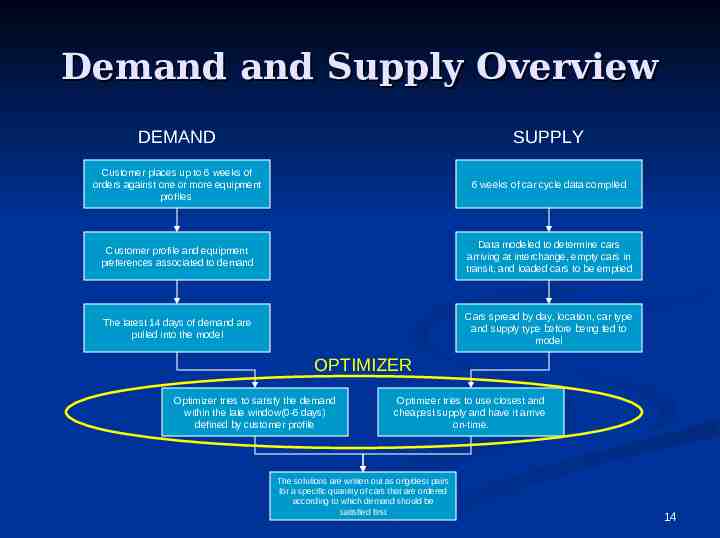
Demand and Supply Overview DEMAND SUPPLY Customer places up to 6 weeks of orders against one or more equipment profiles 6 weeks of car cycle data compiled Customer profile and equipment preferences associated to demand Data modeled to determine cars arriving at interchange, empty cars in transit, and loaded cars to be emptied The latest 14 days of demand are pulled into the model Cars spread by day, location, car type and supply type before being fed to model OPTIMIZER Optimizer tries to satisfy the demand within the late window(0-6 days) defined by customer profile Optimizer tries to use closest and cheapest supply and have it arrive on-time. The solutions are written out as orig/dest pairs for a specific quantity of cars that are ordered according to which demand should be satisfied first 14
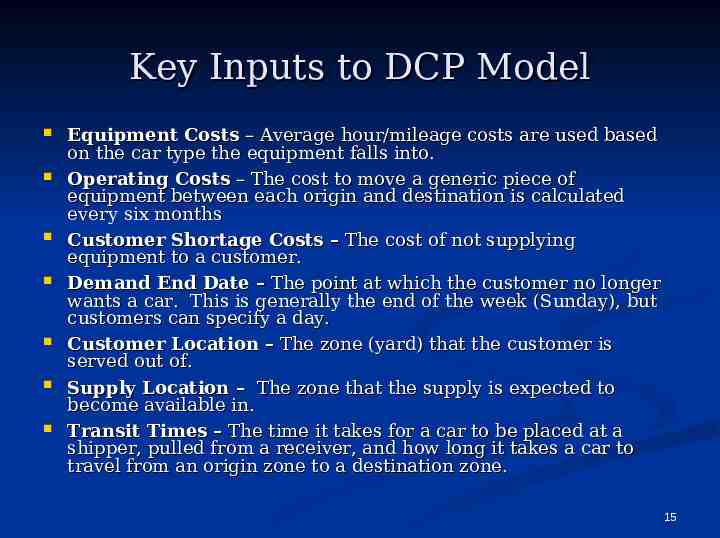
Key Inputs to DCP Model Equipment Costs – Average hour/mileage costs are used based on the car type the equipment falls into. Operating Costs – The cost to move a generic piece of equipment between each origin and destination is calculated every six months Customer Shortage Costs – The cost of not supplying equipment to a customer. Demand End Date – The point at which the customer no longer wants a car. This is generally the end of the week (Sunday), but customers can specify a day. Customer Location – The zone (yard) that the customer is served out of. Supply Location – The zone that the supply is expected to become available in. Transit Times – The time it takes for a car to be placed at a shipper, pulled from a receiver, and how long it takes a car to travel from an origin zone to a destination zone. 15
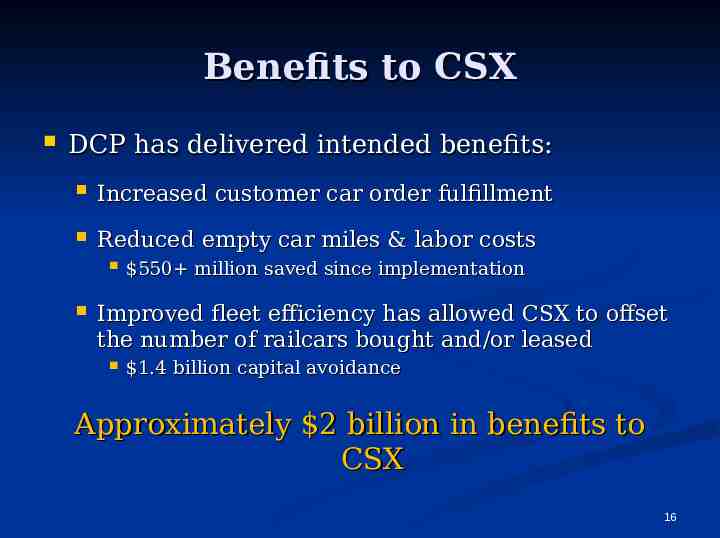
Benefits to CSX DCP has delivered intended benefits: Increased customer car order fulfillment Reduced empty car miles & labor costs 550 million saved since implementation Improved fleet efficiency has allowed CSX to offset the number of railcars bought and/or leased 1.4 billion capital avoidance Approximately 2 billion in benefits to CSX 16
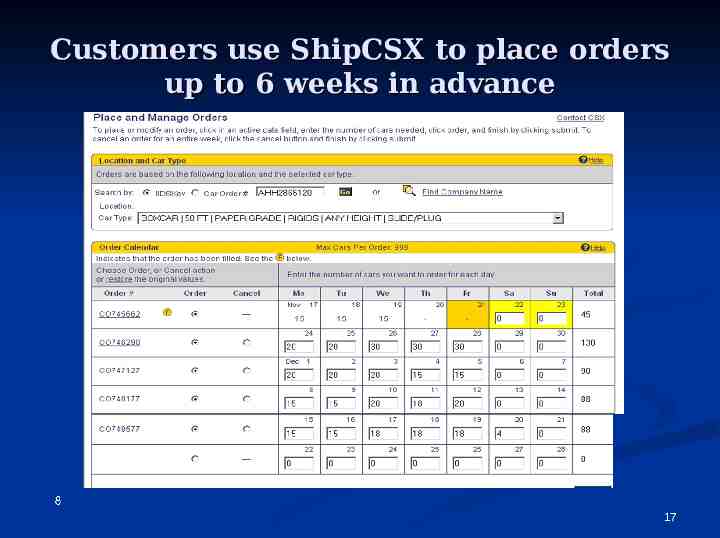
Customers use ShipCSX to place orders up to 6 weeks in advance 17
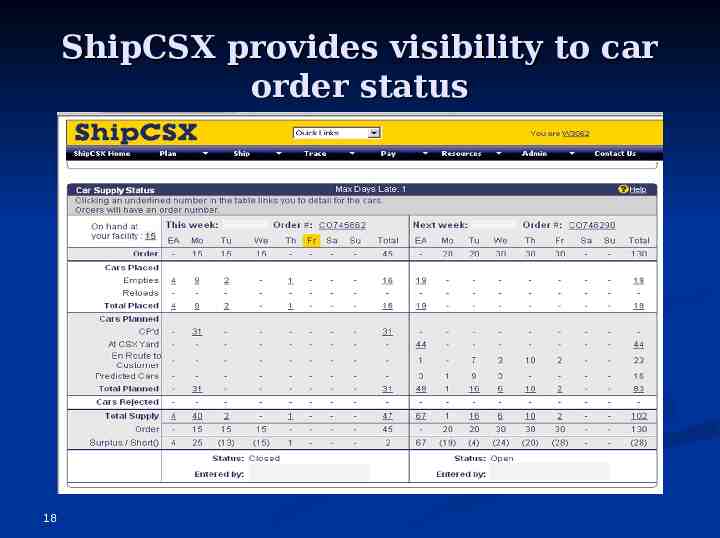
ShipCSX provides visibility to car order status 18
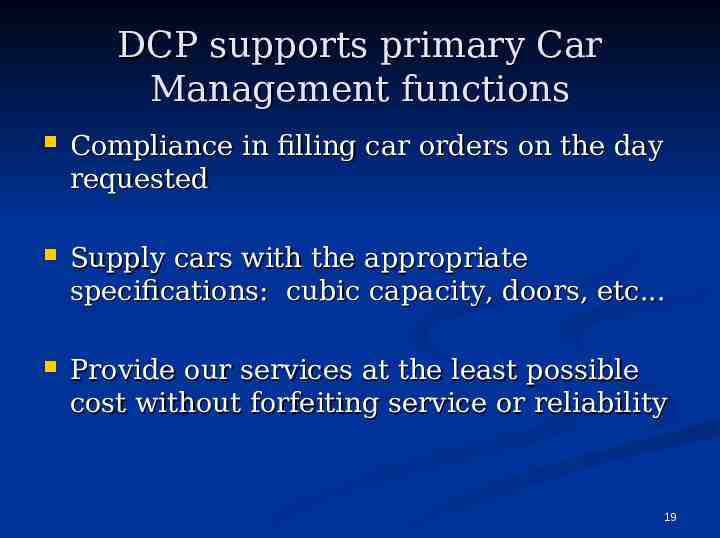
DCP supports primary Car Management functions Compliance in filling car orders on the day requested Supply cars with the appropriate specifications: cubic capacity, doors, etc. Provide our services at the least possible cost without forfeiting service or reliability 19
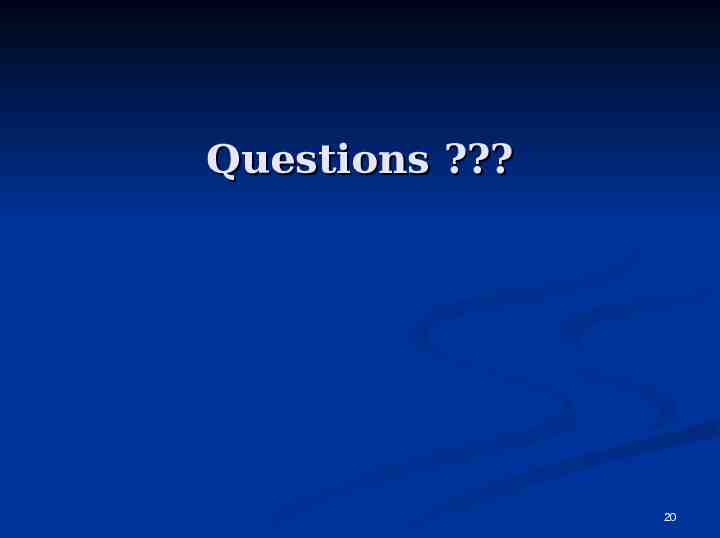
Questions ? 20