Hazardous Materials Certification Training -and- Hazardous
57 Slides6.46 MB
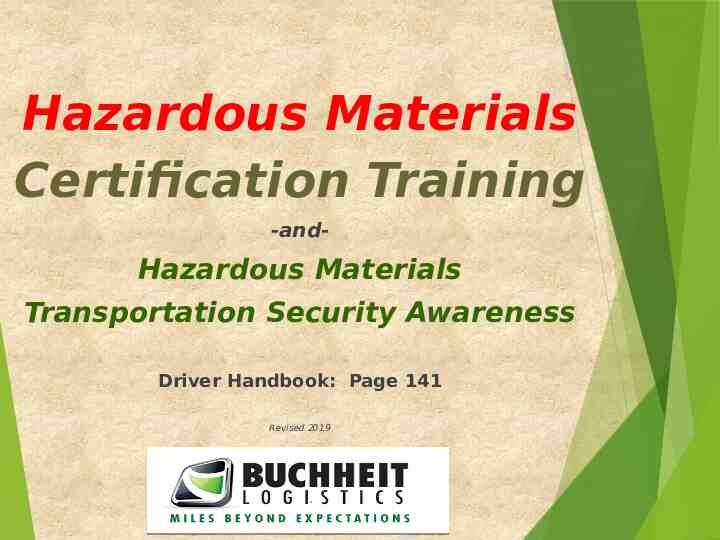
Hazardous Materials Certification Training -and- Hazardous Materials Transportation Security Awareness Driver Handbook: Page 141 Revised 2019

49 CFR Part 172.702 Federal Law dictates that each company involved in the transport of Hazardous Materials must instruct and test its hazmat employees in the rules and regulations concerning the transportation of Hazardous Materials. A Hazmat “employee” is any person employed by a hazmat employer or person who is self-employed (an owner-operator or independent contractor of a motor vehicle that transports hazmat), who directly affects hazmat transportation safety. Training is required within 90-days of being hired, and recertification is required every 3 years. Recertification can be completed by Self Study Guide, online training or by attending formal classroom instruction.

Penalties The penalties for violating a requirement can be up to 250,000.00 for each violation.

Hazard Classes Based on Class/Division number: Classes 1-9 and ORM-D The rules regarding Hazardous Materials can be found in both the Hazardous Materials Compliance Book as well as in the Federal Motor Carriers Safety Regulations Guide.

Class 1 Divisions Division Placard Definition 1.1 Mass explosive hazard 1.2 Projection hazard 1.3 Fire/minor blast hazard 1.4 Minor expl/ hazard (conf. to pkg) 1.5 Insensitive explosives 1.6 Extremely insensitive articles

Class 2 Divisions Division Placard Definition 2.1 Flammable gas 2.2 Non-Flammable, Non-poisonous 2.3 Poisonous by inhalation

Class 3 Divisions Division Placard Definition 3 Flammable liquid 3 Combustible liquid

Class 4 Divisions Division Placard Definition 4.1 Flammable solid 4.2 Spontaneously combustible 4.3 Dangerous when wet

Class 5 Divisions Division Placard Definition 5.1 Oxidizer 5.2 Organic Peroxide

Class 6 Divisions Division 6.1 6.2 Placard Definition Poisonous material Infectious Substance: Label only (No placard)

Class 7 Division Division Placard Definition 7 Radioactive

Class 8 Divisions Division Placard Definition 8 Corrosive

Class 9 Divisions Division Placard Definition 9 Miscellaneous hazardous material

ORM-D Other Regulated Material ORM-D from Class 1 through 9 that is eligible for, packaged, and offered for shipment as a Consumer Commodity suitable for retail consumption. §173.144 Other Regulated Material (ORM)—Definitions. Until December 31, 2020 and for the purposes of this subchapter, “ORM-D material” means a material such as a Consumer commodity, Cartridges, small arms, Cartridges, power devices (used to project fastening devices), Cartridges for tools, blank, and Cases, cartridge, empty with primer, which, although otherwise subject to the regulations of this subchapter, presents a limited hazard during transportation due to its form, quantity and packaging. The article or substance must be a material for which exceptions are provided in Column (8A) of the §172.101 Hazardous Materials Table. [78 FR 65480, Oct. 31, 2013]

Hazmat Communication Hazard Communication consists of 5 steps: Shipping Paper Description Package Marking Package Labeling Vehicle Information found in HM Table Placarding Emergency Response Guidebook

The Hazardous Materials Table contains all hazardous material shipping descriptions and related information Entries are listed alphabetically in column 2. Column Column Column Column Column Column Column Column Column Column 1 2 3 4 5 6 7 8 9 10 Symbols Proper shipping names and descriptions Hazard Class or Division Identification Numbers PG (Packing Group) Label Codes Columns 8, 9 and 10 are in 49 Special provisions CFR Sec 172.101, and not found Packaging (§173.***) not in the “Hazardous Materials Quantity limitations Compliance Pocketbook”. Vessel stowage

! Refer to this table when reviewing your shipping paper and related hazard communication information.

Packing Groups Packing Groups indicate the degree of hazard risk: PG I Great danger PG II Medium danger PG III Minor danger

Offering for Shipment: The Laws The shipper is responsible for: classifying, packaging, marking, labeling and, preparing shipment. the materials for

The Laws §172.204 The shipper is responsible for preparing the proper paperwork for the carrier (driver) to haul the Hazardous Materials. Every shipment must have a Shipper’s Certification statement signed that states they have met and fulfilled all the requirements for the transportation of the Hazardous Materials. The two most important aspects involving the transportation of Hazardous Materials for a driver are: insuring the shipping papers are correct, insuring the placards supplied by the shipper are correct and properly placed on the vehicle.

Shipping Papers §171.2 and §177.817 The carrier (driver) is responsible for: Ensuring the load is properly labeled, marked, not leaking, broken or otherwise improperly blocked and braced during the loading process. Per DOT Regulation §177.817: Drivers have the responsibility, under D.O.T. regulations, to refuse any Hazardous Materials container that is found to have been damaged, is, or appears to be leaking, or that does not match the shipping papers. If the load is sealed by the shipper, and the driver is not authorized to break the seal, then the driver must obtain a statement on the BOL, by the shipper, certifying that the load has been properly loaded, and secured for shipment, S.L.C.S. (Shipper Load Count and Secured).

Marking and Labeling Package marking Proper Shipping Name (including RQ / technical names if appropriate) UN/NA Identification number Special markings (ORM-D, marine pollutant) Orientation markings Package labeling Label for each hazard listed in Column 6 First label code is the primary hazard Additional codes, if listed, are subsidiary hazards. Note that quantity and weight are not required on package markings, labels or placards. This information is found on the BOL.

Shipping Papers Shipping Papers must match the following: Markings on the packages. Labels on the packages. Placards that were supplied by the shipper. 3 ways Hazardous Materials can be indicated on a BOL: Hazardous Materials are listed first on the highlighted BOL. Hazardous Materials have an “X” or “RQ” in HM column. Hazardous Material items are or marked in a contrasting color.

Shipping Papers §172.202 Each Hazardous Material that is offered for transport must be clearly described on the shipping paper using the applicable information from the Hazardous Materials Table. The shipping description must include: Identification Number (UN or NA) Proper Shipping name Hazard Class or Division Number Packing Group (PG)

23.0400 ton, UN 1942, Ammonium Nitrate, 5.1, PGIII, 46,080.00 LBS. I.D. Number Shipping Name Hazard Class Packing Group

Shipping Papers The carrier (Driver) is responsible for ensuring the Shipping Papers are in order, in your possession and immediately available in case of an emergency. When at the driving controls, the shipping papers must be within arms reach while restrained by a seatbelt and visible to anyone entering the vehicle. The usually preferred option is to place the shipping papers (with the ERG) in the holder on the driver’s door. When you exit the vehicle, the paperwork stays in the drivers side door pouch or on the drivers side seat with the engine off, doors locked and freight box locked. When relaying a load, the paperwork should be located in the trailer registration box on the front of the trailer. If dropping the trailer at a secure facility, leave the shipping papers with the guard at the gate.

Shipping Papers Emergency Response Information §172.602 Emergency response information specific to the Hazardous Materials being transported must be presented on the shipping paper or in a separate document in conjunction with the shipping paper such as the Emergency Response Guide (ERG). Emergency Response information must be treated in the same manner as shipping papers regarding availability and placement in the vehicle. The following information is required, as a minimum, by Part 172, Subpart G: - description of the Hazardous Material; - immediate hazards to health; - risks of fire or explosion; - immediate precautions to take in the event of an accident or incident; - immediate methods for handling small or large fires; - initial methods for handling spills or leaks in the absence of fire; and - preliminary first aid measures.

The carrier (Driver) must have a recent copy of the Emergency Response Guide available at all times. It is used for determining the course of action and first aid treatment pertaining to the specific type of Hazardous Material being transported, in the event of an emergency or incident/accident.

Emergency Response Guidebook The Emergency Response Guidebook is color coded: Yellow - ID number is listed numerically. Blue Orange - Guide number. Green - Hazardous Materials listed alphabetically. - Emergency Information. You are looking to identify the proper “guide” number. Once you have found the proper guide number in the Emergency Response Guide, insert your Bill of Lading in that page. The ERG and paperwork stay in the vehicle, within arms reach, at all times.

ERG Section One I.D. Number Listed Numerically

ERG Section Two Hazmat substance listed alphabetically

ERG Section Three Guide Number

ERG Section Four Arsenic trichloride

Placards Placards are used to identify the hazard class of the material being transported. Placards are provided to the driver by the shipper.

Placarding The carrier (Driver) is responsible for ensuring that the proper Placards were provided by the shipper for the Hazardous Material being transported. The placards must be placed by the driver on all 4 sides of the trailer and can be no closer than 3 inches from any other markings on the trailer. All placards must be completely removed after delivery of the Hazardous Materials.

Placards It is the Carriers (Drivers) responsibility to make sure the correct Placards are affixed before the Shipment is transported. Use the Hazmat Pocketbook to verify you were given the correct Placards. If they are incorrect: do not leave the Shipper until you have the proper placards. When in doubt, contact your Fleet Manager or the Safety Department.

Placards Any Hazardous Material weighing 1001 lbs. or more must be placarded. Any Table 1 Material must be placarded no matter what the weight is. All Hazmat placards must be printed and displayed: 1. Horizontally, Square on Point, Reading from left to right. 2. They must not differentiate in size. 3. Must identify multiple hazards. 4. The view must not be obstructed (can not cover the inner border of the placard). 5. The placard must identify the Hazmat you are hauling. 6. The placard must attached securely. 7. The placard must maintained and in good condition. 8. The placard must clear of all advertising, dirt, etc 9. Each side and each end of the vehicle must have a placard. 10. Remove the placards once the Hazmat has been unloaded .

Restricted Hazmat The company does not haul any “Table 1” products, Shipments nor any products that are “Placard any Quantity”. We will not accept the following Classes: Class 1.1, 1.2, 1.3, 1.5 (we will accept 1.4 and 1.6 in Less Than Truckload quantities). Class 2.1 Flammable Gases, 2.2 Poison Gases or 2.3 Toxic Gases (unless approved by management) Class 4.1 Flammable Solid and 4.2 Spontaneously Combustible (unless approved by management). Class 5.2 Organic Peroxides (Temperature controlled). Class 6.1 Toxics by Inhalation (unless approved by management). Class 6.2 Infectious Substances. Class 7 Radioactive Materials (unless approved by management). Any material which has any of the above as a subsidiary hazard.

Dangerous Placard Remember that 1001 lbs. or more of one class requires placards; however, the Dangerous placard may be used as an exception, when two or more Hazardous Classes, with a combined aggregate gross weight (AGW) of all Hazardous Material Classes is more than 1000 lbs. 1001 pound rule (Dangerous Placard Exception): 300 lbs Corrosive combined with 600 lbs Flammable: No placard 1050 lbs Flammable and no other Hazardous Material: Flammable placard 1300 lbs Corrosive plus 600 lbs Flammable: Dangerous placard

2205 Rule When carrying 2 or more Classes of Hazardous Materials, and any Class of Hazardous Material is 2205 lbs or more, that Class requires its own placard. 3 Examples: 1300 lbs Corrosive plus 2600 lbs Flammable 2 Separate Placard Types Dangerous placard for the 1300 lbs Flammable placard for the 2600 lbs 2800 lbs Flammable 500 lbs Oxidizer Flammable and Dangerous placards 4300 lbs Corrosive 2600 lbs Flammable 2 Hazard Placards Corrosive placard (AGW over 2205) Flammable placard (AGW over 2205) The DANGEROUS Placard is not an option!

Large Quantity / Bulk Shipments When there is one item, non-bulk packaging, loaded at one facility and weighing over 8820 pounds, the shipment is considered to be a Large Quantity Shipment, and may contain no other Hazardous or otherwise. material, A common example of this would be a truckload shipment of flammable paint in drums and/ or pails. The Placard provided would have a 4 digit UN or NA number on it that identifies the product being transported and is a Bulk Shipment.

Equipment, Tire and Freight Checks §397.17-Tires Federal laws require the driver to inspect each tire of the both units when transporting Hazardous Materials. The law states tire checks must be done when first picking up the load and every time the vehicle stops. Flat, leaking, or improperly inflated tires must be replaced at the nearest safe place to perform repairs. Overheated tires must be removed and placed away from vehicle immediately. Vehicle must not be moved until the cause for overheating is resolved. Each time you stop or park, you must inspect your equipment. Examine tires, brakes, freight (if not sealed).

Part 392: Driving of CMVs §392.10 —Railroad Grade Crossings; Stopping Required a) the driver of a commercial motor vehicle which, in accordance with the regulations of the Department of Transportation, is required to be marked or placarded shall not cross a railroad track or tracks at grade unless he/she first: Stops the commercial motor vehicle within 50 feet of, and not closer than 15 feet to, the tracks; thereafter listens and looks in each direction along the tracks for an approaching train; and ascertains that no train is approaching. When it is safe to do so, the driver may drive the commercial motor vehicle across the tracks in a gear that permits the commercial motor vehicle to complete the crossing without a change of gears. The driver must not shift gears while crossing the tracks. b) There are 4 exceptions pertaining to railroad crossings: i. If the crossing is clearly marked exempt, ii. If it is marked by an arterial traffic light and it is green, iii. If the crossing is controlled by an emergency official, iv. If a streetcar crossing or switching tracks within a business district.

Part 397: Transportation of Hazardous Materials §397.15 — Fueling When a motor vehicle which contains Hazardous Materials is being fueled — Its engine must not be operating; and A person must be in control of the fueling process at the point where the fuel tank is filled. This means a driver cannot conduct a vehicle inspection during the fueling process or leave the fueling process unattended for any reason.

Part 397: Transportation of Hazardous Materials §397.13 — Smoking No person may smoke or carry a lighted cigarette, cigar, or pipe on or within 25 feet of: (a) A motor vehicle which contains Class 1 materials, Class 5 materials, or flammable materials classified as Division 2.1, Class 3, Divisions 4.1 and 4.2; or (b) An empty tank motor vehicle which has been used to transport Class 3, flammable materials, or Division 2.1 flammable gases, which, when so used, was required to be marked or placarded in accordance with the rules in §177.823 of this title. This rule applies to time in the sleeper too Any time “on” or within 25 feet of the CMV.

Part 397: Transportation of Hazardous Materials §397.11 — Fires A motor vehicle containing Hazardous Materials must not be operated near an open fire unless its driver has first taken precautions to ascertain that the vehicle can safely pass the fire without stopping. A motor vehicle containing Hazardous Materials must not be parked within 300 feet of an open fire.

Security of Hazmat Load The driver must be in attendance of the vehicle at all times when transporting Hazardous Materials. Attendance is defined as: on the vehicle awake, (not in the sleeper berth), or within 100 feet with an unobstructed view of the vehicle at all times. Never leave the vehicle unattended on or near a public street unless performing necessary duties Secure the trailer with a padlock on every hazmat load. For further guidance on en route security, refer to your driver handbook or your Fleet Manager.

Hazardous Materials Transportation Security Plan Statement and Objective: Awareness The events of 9/11 make it clear that all Americans have a responsibility to be diligent in protecting our homeland from attack. There are 800,000 hazardous materials loads moved daily in the United States and 95% are moved by truck. Your responsibility is to protect hazardous cargo from theft, sabotage, and hijacking at all times. Suspicious Activity and Suspicious Activity Reporting Procedures: Team members are expected to use common sense and good judgment when assessing the threat potential of any suspicious activity. Team members are expected to report observed suspicious activity to their immediate supervisor, manager, or local law enforcement and/or fire department.

Hazardous Materials Security Plan All employees are expected to be familiar with the company’s Hazardous Materials Security Plan. See You the Driver’s Handbook will be expected to follow these directives and, under no circumstances, deviate from them.

Hazmat En Route Standard Security Operating Drivers should prepare and execute a trip plan for all Procedures hazmat movements that include: Routing schedules that avoid highly populated areas, bridges, and tunnels when possible. Fueling and break locations (including dates and times for same). Dates and times of daily/routine check calls. Estimated times of arrival to any extra stops and final destination. For all hazardous materials movements, drivers should minimize stops en route. Remember, on all Hazardous Materials loads you must follow company and local routing instructions. If you are detoured, notify your Fleet Manager, with the specifics of where you are being detoured.

Hazardous Materials Transportation Security Plan Operations shall make every effort to arrange hazardous materials delivery schedules that minimize in-transit down time. While in transit, drivers are prohibited from discussing information related to their load, route, or delivery schedule with any unauthorized person(s). Drivers are expected to take all reasonable and responsible precautions to prevent damage to company vehicles and theft of hazardous material(s) cargo while in transit. For personal protection and safety, and the security of the cargo, drivers are expected to park in safe, well-lit, designated truck parking locations only. Drivers shall lock their vehicles and have all windows closed at all times while in transit. When possible, dispatch shall contact receivers for arranging secure overnight or after hours parking for drivers who can safely and legally arrive at the destination ahead of schedule. Upon arrival at the destination or stop off, drivers shall check in with the responsible receiving person(s) to notify them of arrival and receive unloading instructions. The driver, along with a responsible receiving employee, shall verify delivery, inspect the trailer seal(s), match the seal number(s) with those on the shipping papers prior to breaking the seal(s); then open and secure the trailer doors, and inspect the cargo.

Hazardous Materials Spills The driver’s responsibility in the case of a spill: remain with the vehicle, keep unauthorized persons away, notify local authorities and, to prevent the spill from spreading (if safe). When A Hazardous Material Spill Occurs – think G.I.N.: Gather your information and get away, Isolate the area (150 feet minimum), Notify the authorities (911), Call your employer/company immediately!

Hazardous Materials Tips Be proactive. Always Use do a proper Pre/Post Trip Inspection. common sense. Most Hazmat problems can be identified through sight, sound and smell. Do not do anything that you are unsure of: When Call in doubt – communicate! your Fleet Manager or the Safety Department.

QUESTIONS? UN2056, Tetrahydrofuran, 3, PGII UN1179, Ethyl Borate, 3, PGII UN3066, Paint, 8, PGII

To begin the process for obtaining your Hazardous Materials Endorsement (HME) https://universalenroll.dhs.gov/

Hazardous Materials Certification Test Microsoft Word 97 - 2003 Document
