FLASH BUTT WELDING OF RAILS 1
14 Slides2.72 MB
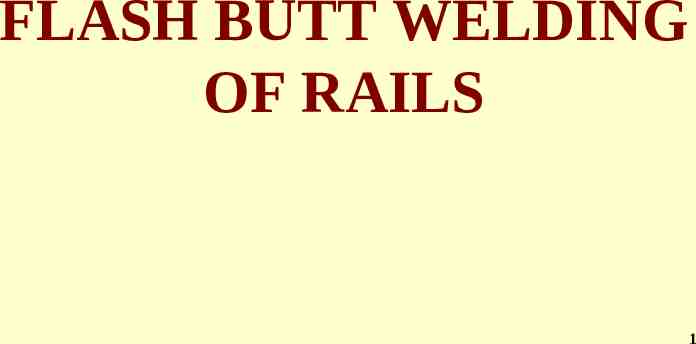
FLASH BUTT WELDING OF RAILS 1
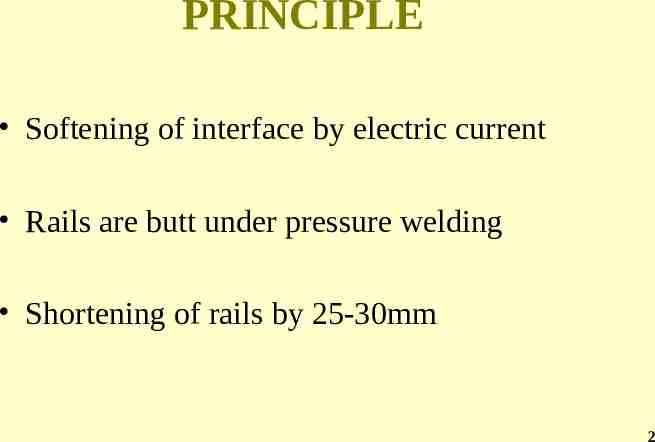
PRINCIPLE Softening of interface by electric current Rails are butt under pressure welding Shortening of rails by 25-30mm 2

COMPONENTS OF MACHINE Clamping mechanism Forging mechanism – Bring the rails in contact at low force – Application of high force on completion of welding cycle Step down voltage from 400-500V to 4-12V and current between 30,000Amp to 80,000Amp 3
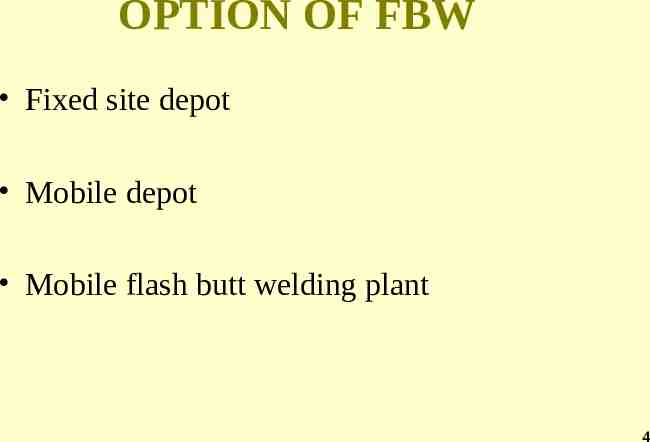
OPTION OF FBW Fixed site depot Mobile depot Mobile flash butt welding plant 4
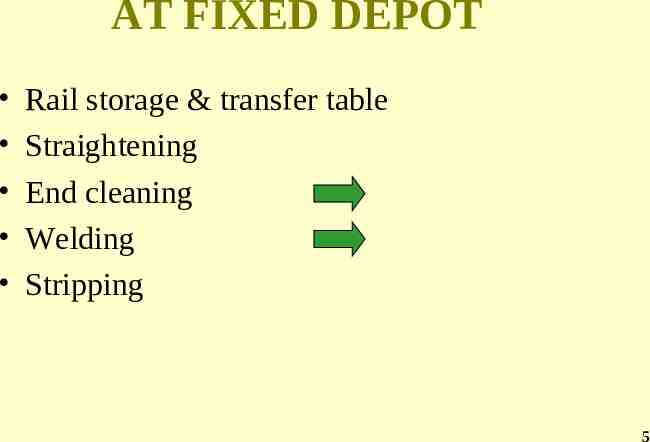
AT FIXED DEPOT Rail storage & transfer table Straightening End cleaning Welding Stripping 5
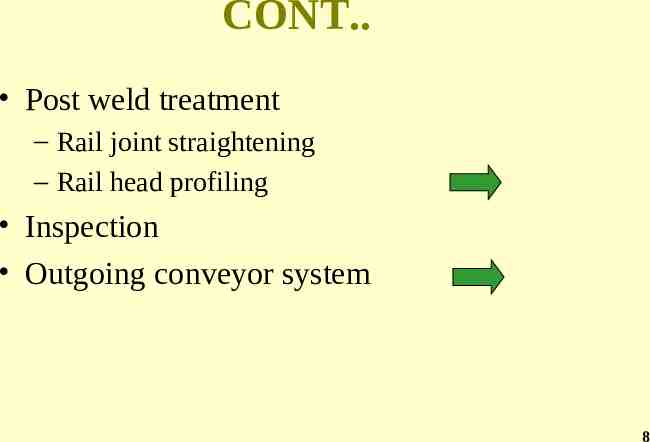
CONT. Post weld treatment – Rail joint straightening – Rail head profiling Inspection Outgoing conveyor system 8
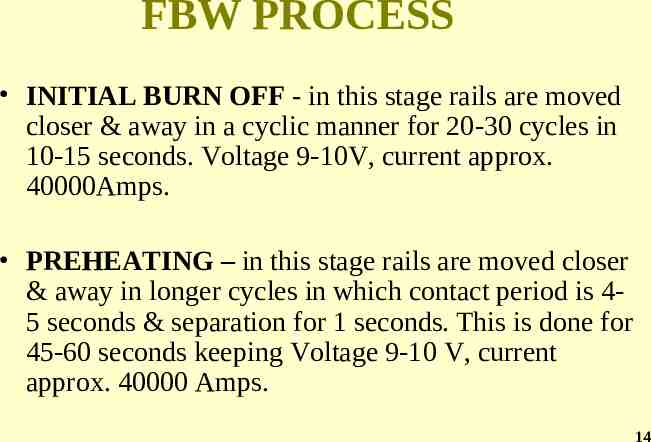
FBW PROCESS INITIAL BURN OFF - in this stage rails are moved closer & away in a cyclic manner for 20-30 cycles in 10-15 seconds. Voltage 9-10V, current approx. 40000Amps. PREHEATING – in this stage rails are moved closer & away in longer cycles in which contact period is 45 seconds & separation for 1 seconds. This is done for 45-60 seconds keeping Voltage 9-10 V, current approx. 40000 Amps. 14
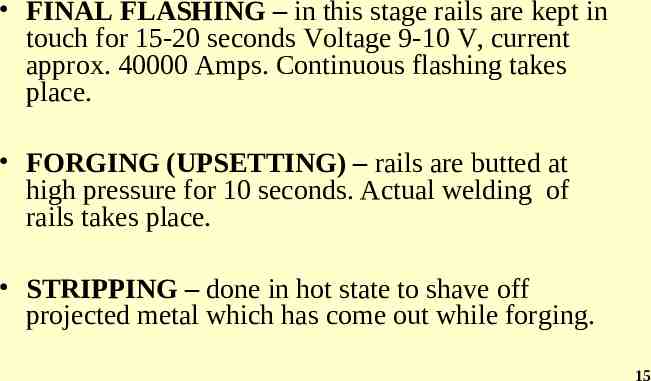
FINAL FLASHING – in this stage rails are kept in touch for 15-20 seconds Voltage 9-10 V, current approx. 40000 Amps. Continuous flashing takes place. FORGING (UPSETTING) – rails are butted at high pressure for 10 seconds. Actual welding of rails takes place. STRIPPING – done in hot state to shave off projected metal which has come out while forging. 15
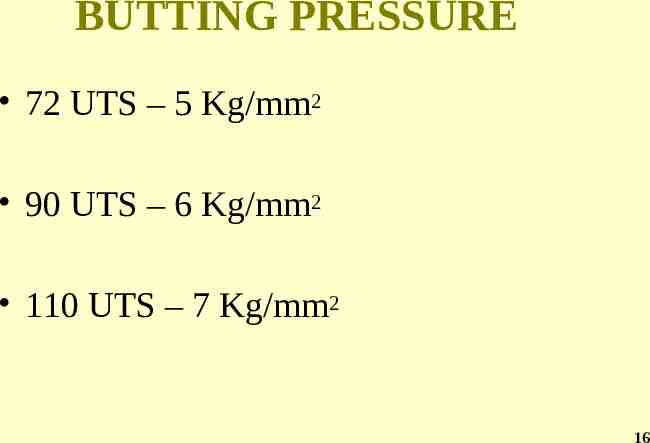
BUTTING PRESSURE 72 UTS – 5 Kg/mm2 90 UTS – 6 Kg/mm2 110 UTS – 7 Kg/mm2 16
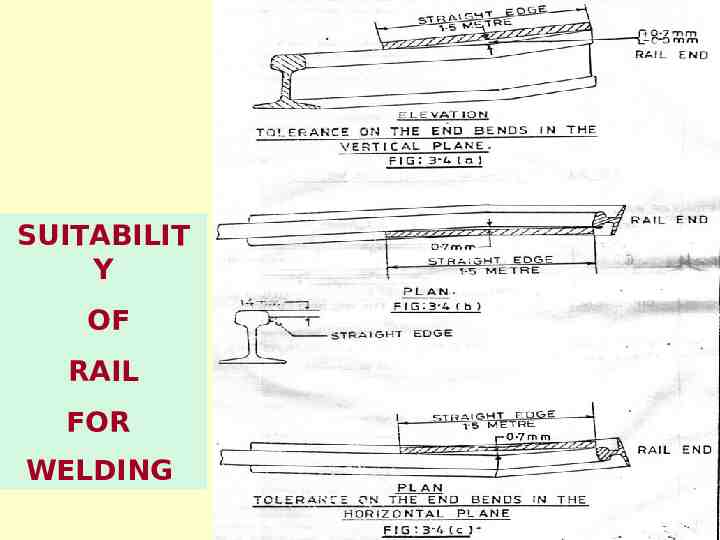
SUITABILIT Y OF RAIL FOR WELDING 17
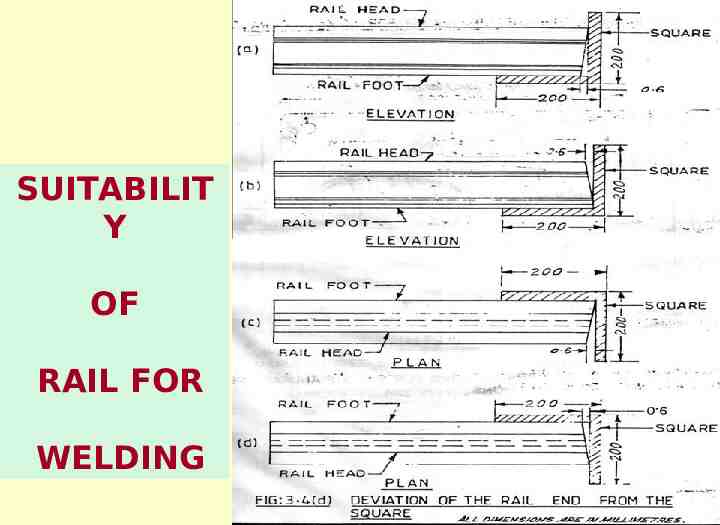
SUITABILIT Y OF RAIL FOR WELDING 18
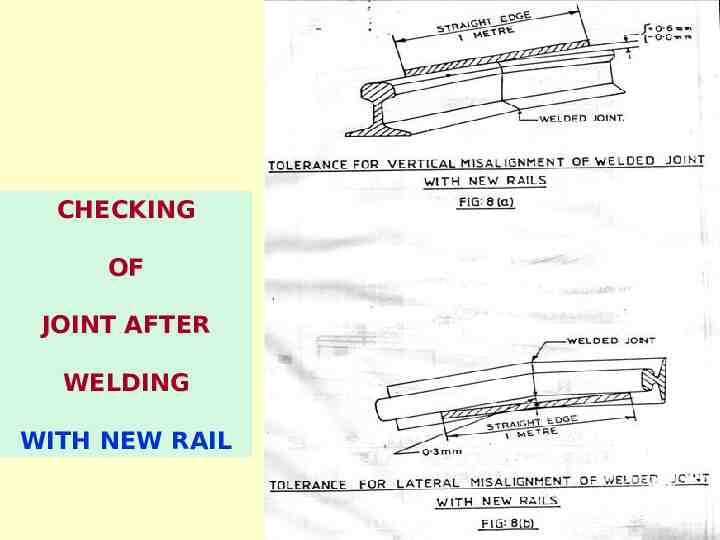
CHECKING OF JOINT AFTER WELDING WITH NEW RAIL 19
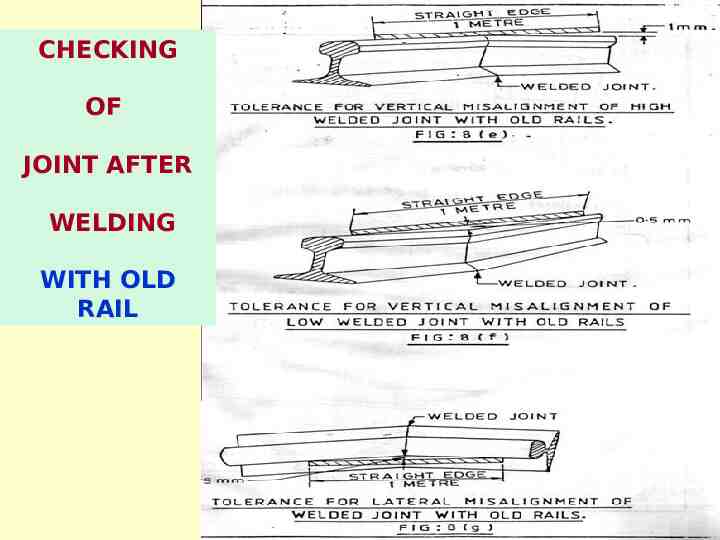
CHECKING OF JOINT AFTER WELDING WITH OLD RAIL 20
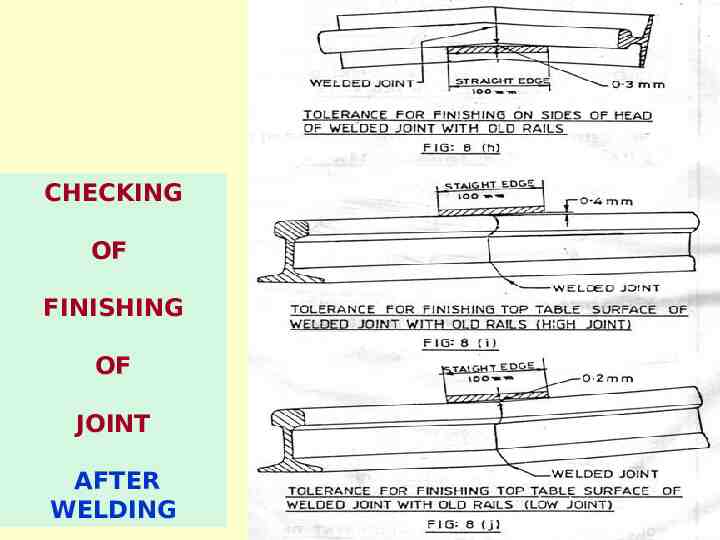
CHECKING OF FINISHING OF JOINT AFTER WELDING 21