Basics of Lean How to See and Eliminate Waste Slides courtesy of Doug
21 Slides111.50 KB
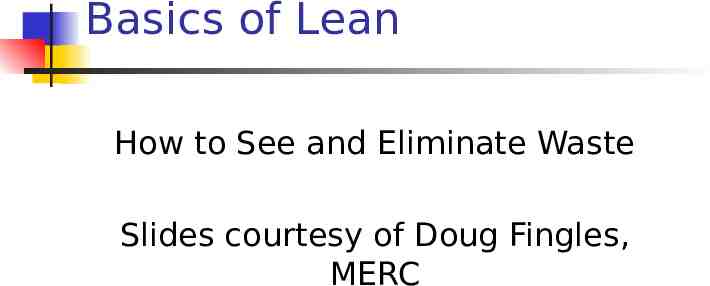
Basics of Lean How to See and Eliminate Waste Slides courtesy of Doug Fingles, MERC

Concept “Lean” is not an acronym Most processes in North America are 95% waste It means to do more with less waste Actual hands-on time is only 5% The largest production gains will be made in reducing the waste in a process

Why Lean? Competition is world-wide and growing Companies that meet customer needs and are more efficient than their competitors will survive “You can have any color you want, as long as it’s black” is a dead philosophy

History of Lean Henry Ford Taiichi Ohno and the Toyota Production System “The Machine that Changed the World” “Lean Thinking” Automotive industry Aerospace industry And beyond

8 types of waste Injuries Defects Inventory Overproduction Waiting time Motion Transportation Processing

5 Key Principles Value Value Stream Flow Pull Perfection

What is Value? Specific product that meets a customer’s needs at a specific price and specific time What is important to the customer What the customer is willing to pay for Put yourself in the customer’s shoes Use the customer’s words to describe the product

What is the Value Stream? Set of specific actions required to bring a specific product through 3 critical management tasks of all businesses Problem Solving task (design, engineering) Information Management task (order taking, scheduling, planning) Physical Transformation task (from raw material to finished product)

What is Flow? Parts “flow” through a Value Stream Upstream is the beginning or “head” of the flow Downstream is the “mouth” of the flow, where the part is pulled by the customer Materials and parts are the “parts” in manufacturing Customer’s needs are the “parts” in service industry Same for administration

What is Pull? “It has become a matter of course for customers, or users, each with a different value system, to stand in the frontline of the marketplace and, so to speak, pull the goods they need, in the amount and at the time they need them.” Taiichi Ohno, “Toyota Production System” “ Nothing is produced by the upstream provider until the downstream customer signals a need” Womack and Jones, “Lean Thinking”

What is Perfection? The complete elimination of all waste, so that all activities along a value stream add value to the product Ideal State Map
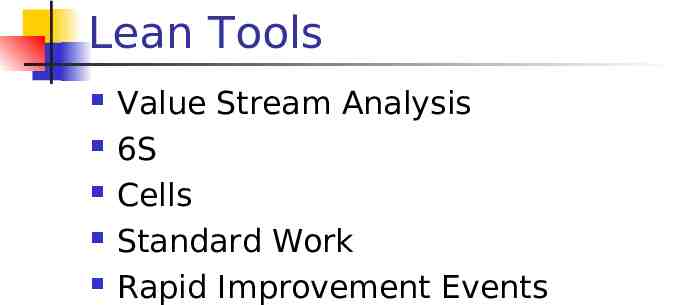
Lean Tools Value Stream Analysis 6S Cells Standard Work Rapid Improvement Events

Value Stream Analysis Use Value Stream Analysis as a planning tool Break down the Value Stream in manageable sections Communicate the “flow” with maps Information Material Use Value Stream Analysis to create 3 maps Current Ideal Future (near time-within a year)

6S Often confused with Lean, because you are “doing” something Second step, after Value Stream Analysis

6S A tool to organize the workplace Sort—Keep what you need, get rid of the rest Straighten—Organize what’s left Scrub—A clean workplace is more efficient Safety—Without our people, nothing gets done Standardize—Find a best way and have everyone do it that way Sustain—Don’t let up

Cells Natural groups of parts or steps that add value to a product Single piece flow inside the cell One at a time If possible, one operator per cell U-shaped to maximize human efficiency Multi-skilled people required Layout is based on the flow steps

Standard Work The precise description of each work activity specifying cycle time, takt time, the work sequence of specific tasks, and the minimum inventory of parts on hand to conduct the activity Everyone knows what they are supposed to do at any moment in time

Rapid Improvement Events A seven week cycle of preparation, action, and follow-up to improve one area or fix a problem People: work leaders, mechanics, workers, supervisor, and a Lean Change Agent Led by the supervisor or work leader Guided by the Lean Change Agent

Review Concept Principles History and reasons why Value, Value Stream, Flow, Pull, Perfection Tools Value Stream Analysis, 6S, Cells, Standard Work, Rapid Improvement Events

Acknowledgements “Lean Thinking” by James Womack and Daniel Jones “Toyota Production System” by Taiichi Ohno Simpler Business System, www.simpler.com
